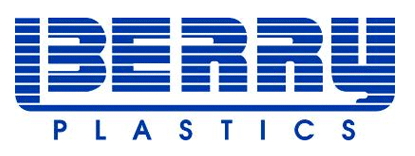
- Customer: Berry Plastics (Now has been renamed as Berry Global)
- Country: India
- Industry: Plastic Material
- Solution: Moldex3D Advanced Package; Flow, Pack, Cool, Warp, Advanced Hot Runner
- View PDF Version
Executive Summary
This case study focuses on saving manufacturing time by adjusting just one parameter. Moldex3D is used for not only optimizing product design but also dealing with the basic issues. Berry Plastics needed to reduce the cycle time of the covers molded in multiple cavities without making modifications to the tooling. The filling time, the only modified parameter, was reduced in the process setting and the result was validated through Moldex3D. The reduction of filling time then further saved around 1 second per molding cycle as well as lots of time and human effort in the overall production (Fig. 3).
Challenges
- The need to change the product design in the very early stages to avoid future problems in the tooling and manufacturing
- With the traditional practice, the troubleshooting process costs lot of human effort.
Solutions
Moldex3D is utilized to evaluate the impact of changing the process parameters.
Benefits
- Optimized process conditions to reduce costs.
- Streamlined the product development process.
Case Study
Berry Plastics used a simple case of covers molded in a multiple cavity system (Fig. 1) to prove the basic concept of “time will save money” by adjusting just one parameter (reducing the filling time). They also utilized Moldex3D to calculate the benefits of reducing the mold trial and cycle time.
Fig. 1 A simple plastic cover molded in a mutiple cavity system
The purpose of this case was to have the parts formed earlier and reduce the filling time. However, the cost of changing the tooling is very high. The fill time can be reduced in the processing side using the same tooling. The filling time was reduced from 1.6s to 1.2s with the same mold and part design. As a result, the simulation showed that the overall molding time had been reduced by almost 1s and the part was still fully filled successfully (Fig. 2).
Fig. 2 Validating the flow patterns through Moldex3D after moldifying the process condition, shorter filling time
By transferring the time reduction of the molding process to the total time of manufacturing, it shows a massive time reduction and thus expense savings when manufacturing a large amount of products (Fig. 3). With the help of Moldex3D simulation, Berry Plastics found significant benefits for real world manufacturing.
Fig. 3 With reducing the filling time, we can find big savings with massive manufacturing
Results
Moldex3D is used for troubleshooting in every aspect of product development and different stages in the manufacturing cycle. From the product design to tool making to the process engineering, Moldex3D can make a big contribution. The product design changes have to be made through Moldex3D in a very early stage so that many future problems in the tooling and manufacturing can be avoided. After making the tool, Moldex3D is still useful for adjusting process conditions to improve product quality.