Industry Challenges
Plastic materials are widely used in medical devices industry. The applications of plastic injection molding range from surgical, diagnostic testing, drug delivery, geriatric care, self-treatment, preventative medicine, and etc. In recent years the development of plastic application in prosthetic device and invasive surgical instrument has drawn lots of attention due to its cost-effectiveness and better antiseptic. Due to delicacy and defect-free requirements for medical devices, quality control is the key for manufacture procedure. Also, because of the small part size, many medical devices are manufactured in multi-cavity injection molding to increase productivity. It is critical to have all cavities fill uniformly to ensure even products quality and high yield rate. Traditionally, trial-and-error method is applied to test and verify design. However, it results in long product manufacturing cycle time and high production costs. Moreover, many medical devices are made of fabricated components. To be fabricated seamlessly, warpage of each molded part should be controlled precisely. To overcome all the design problems within time and cost constraints is a great challenge for medical-device industry.
Image courtesy of ADVANGENE
Moldex3D Solutions and Benefits
Moldex3D professional CAE simulation software can be utilized in different product development stages.
During pre-development stage, the mold has not been manufactured yet, and engineers can use the simulation tool to verify their designs such as potential short shot and weld line locations. In additional to detecting problems in advance, Moldex3D can help verify and optimize design. Users can use simulation tool to compare many different designs such as number of gates, runner system and cooling system layouts by generating iterated simulation run to achieve the optimized design without wasting time and money on trial-and-error experimental methods.
Moldex3D provides simulation for Fill, Pack, Cool, and Warpage, a complete simulation solution for injection molding manufacture process of medical product. Moldex3D aims to add value to each company by presenting problems and solutions, contributing to reduced time-to-market and prime product standard.
Moldex3D Solves Tough Problems
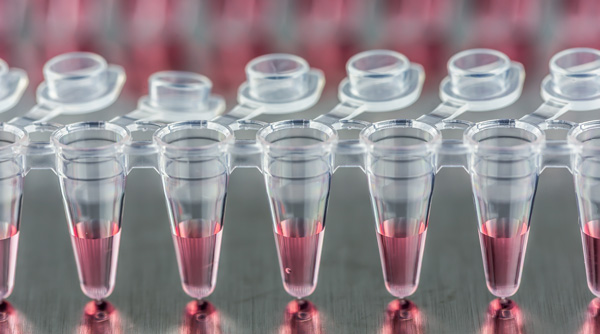
Multiple cavities product
-
Challenges
-
Solutions
-
- Multiple cavities product is the widest application of plastic product in medical industry. In multi-cavity molding, attaining uniform and balanced flow of material to each cavity is a frequent challenge.Imbalance could still occur in a geometrically balanced runner design due to the viscous heating effect, so how to optimize the runner system will be a big problem in this topic.
-
- Multiple cavities product: Moldex3D molding simulation helps users to predict the uneven flow and short shot issues in advanced. Users can modify the runner layout by referring to simulation results, and then the product quality would be better by optimizing manufacturingprocess.Moldex3D uses true 3D runner mesh for molding analysis. Due to the boundary which is one of the most important areas forcomputation during the injection molding process, Moldex3D buildsboundary layer mesh(BLM) for more accuracy simulation results.
Multiple component product
-
Challenges
-
Solutions
-
- Since healthcare is a highly regulated industry, effective and precise quality control is essential and indispensible to ensure product quality and to maintain its high standard. How to manufacture prime quality products within time and cost constraints has raised the great challenge for New Deantronics.
-
- Via Moldex3D, accurately predicts the behavior of melt front.Modifies runner and gate system design, and allows melt filling in thick section before contacting the thin section. This can eliminate problems of melt temperature drop and flow hesitation due to uneven thickness, ensuring smooth and uniform to fill in the cavity. Furthermore, Moldex3D provides fully fluid structure interaction analysis for users and plays a chief role in the production of these manufactures.
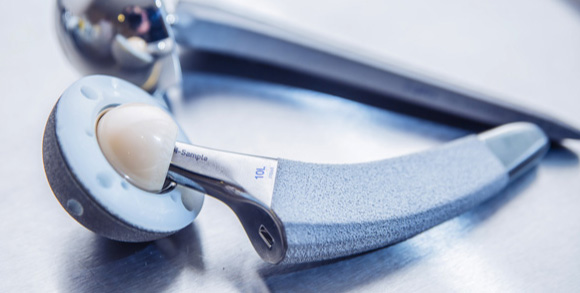