Industry Challenges
Today’s optics industry does not only face shorter time-to-market pressure, but also with more challenging requirements on product qualities: dimensional stability and birefringence issue. Since more and more optics manufacturers have chosen plastics as preferred alternative, the capability of optimizing plastics injection molding process becomes your absolute advantage in this competitive industry.
Thermally induced fringed order and pattern
Moldex3D Solutions and Benefits
Moldex3D Solutions is able to provide optics manufacturers and design engineers with analysis results to verify complex designs based on true 3D technology. With Moldex3D, optics designer and makers can find out certain potential problems at early stage through the visualization of the entire injection molding process. Therefore, Moldex3D is very powerful and effective in obtaining suitable solutions. Furthermore, it can help optimize part/mold designs or process conditions to improve quality of optical parts. In addition, Moldex3D Optics module can export deformed shape and refractive index data for optical analysis in CodeV. This integration allows designers to confirm or revise their designs. On the other hand, Moldex3D Optics can extend to non-traditional injection process. This feature provides extensive applications on optical parts using injection compression molding (ICM) or multiple components molding process (MCM).
Moldex3D Solves Tough Problems
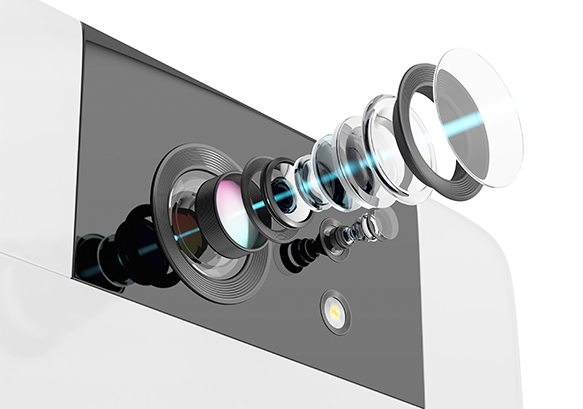
Optical parts
-
Challenges
-
Solutions
-
- Birefringence problems with various optical lenses due to residual stress.
- Dimension control and warpage problems are encountered for light guide plate, optical disk and so on.
-
- Using Moldex3D Advanced Packge to analyze the main source of dimension variation and warpage, and to provide directions to revise part design or mold design, or to optimize process parameters.
- Applying Moldex3D Viscoelasticity Module to trace flow-induced residual stress at different stages and then modify process conditions.
- Using Moldex3D Optics Module to investigate photoelastic fringe patterns from thermal and flow-induced residual stress to find out the root cause of birefringence.
- Applying Moldex3D ICM Module to explore optical properties on optical parts using injection compression molding process and then to optimize the designs or compression parameters.