Product Portfolio and Features
Standard Injection Molding
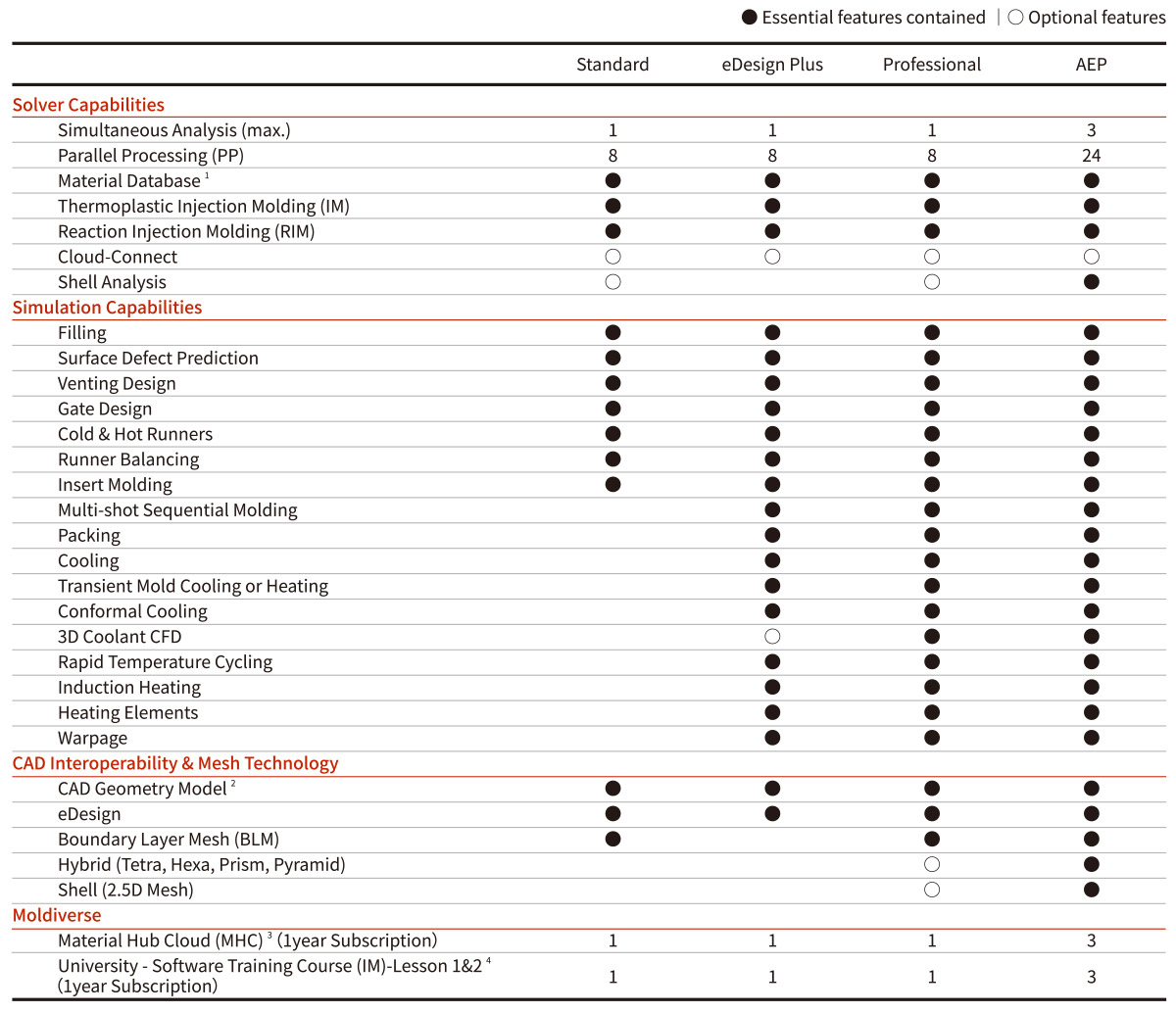
Solution Add-on
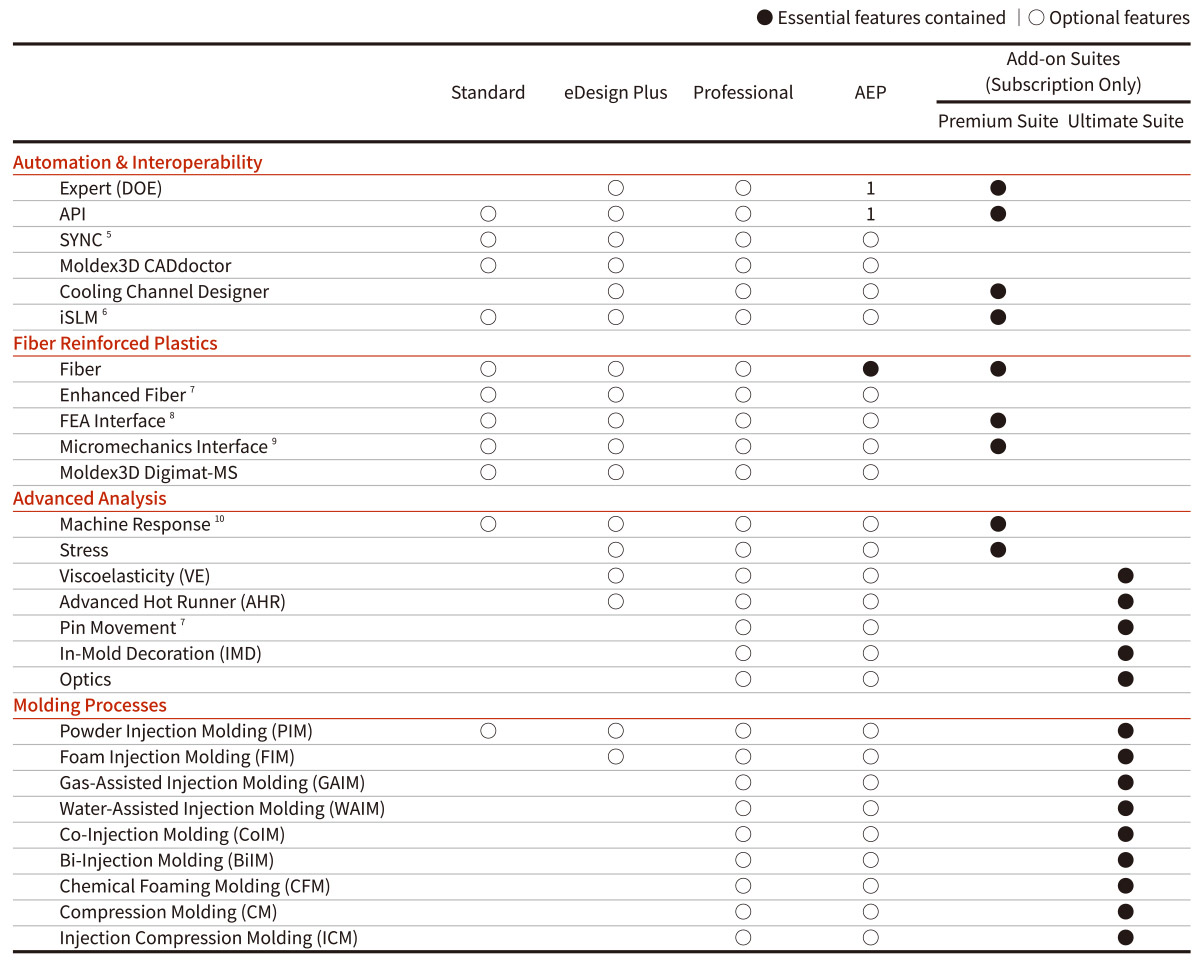
- Material Database: thermoplastics materials, thermoset materials, molding materials, coolant materials, and mold materials.
- Import geometry from CATIA V5, PTC® Creo®, NX, SOLIDWORKS® and Rhino, as well as STEP, IGES, Parasolid and STL files.
- Material Hub Cloud (MHC) is a subscription-based service offering the most up-to-date material properties for users to find suitable materials and alternatives.
- The best on-line practical guide and demo videos by Moldex3D software experts. (Subscription-based service)
- Moldex3D SYNC supports PTC® Creo®, NX, and SOLIDWORKS®.
- iSLM is an intelligent and interactive data management platform for plastic product development lifecycle.
- Prerequisite license is required.
- Moldex3D FEA Interface supports Abaqus, Ansys, MSC Nastran, NX Nastran, LS-DYNA, MSC Marc, and OptiStruct.
- Moldex3D Micromechanics Interface supports Digimat and CONVERSE.
- Machine Response function requires the machine file received from the Machine Characterization Service.
System Requirements
A. Supported Platform
Windows |
Windows 10, Windows 11, Windows Server 2019, Windows Server 2022 |
Linux |
Rocky Linux 8.10 and higher, Rocky Linux 9.4 and higher |
B. Hardware Recommendation
Minimum | |
CPU | CPU speed 2 Ghz |
RAM | Main memory 16 GB |
HDD | 20GB free disk space (at least 2 GB for installation) |
Recommended | |
CPU | AMD EPYC™ Milan / Milan-X series, Intel® XEON® Gold / Platinum / Bronze series |
RAM | 16GB x 8 With ECC / 3200Mhz |
HDD | 4 TB SSD (For Project Management) |
Graphic Card | OpenGL 4.3 or higher, 512 MB or larger DRAM graphic cards |
Screen Resolution | 1920 x 1080 |
- Linux platform is used for calculation resource only. Moldex3D Pre/Post-processor does not support Linux platform.
- To increase calculation efficiency and stability, it is recommended to switch off Hyper-Threading under RC/DMP structure. For the 12th Gen Intel® Core™ processors, only performance cores are used in default. For memory population rules, please refer to your CPU processor type for optimized performance.