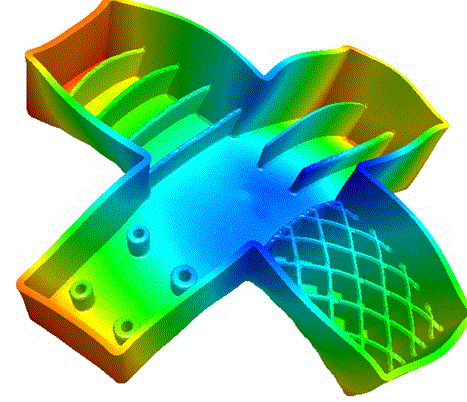
Warp
Warpage is one of the most apparent and critical phenomenon that affects product quality, by reducing product warpage, yield rate is improved, therefore reducing company costs.
Moldex3D Warp allows users to perform dynamic warpage analysis on thick parts and those parts that have extreme dimension changes. With Warp, users can easily validate part deforming ratio of shrinkage effect and efficiently identify warpage causes. For fiber-filled material, Warp incorporates fiber composite theories and fiber orientation results to predict its anisotropic shrinkage, residual stress on warpage. Furthermore, Warp can link through FEA Interface module, which integrated with most leading structure software to perform more realistic structural analysis.
Capabilities
- Predict final part shape before actual molding and identify warpage root causes.
- Evaluate displacement, volumetric shrinkage, density, , fiber orientation(with Fiber module), thermally / flow-induced residue stress, differential shrinkage effect, differential temperature effect, flatness
- Consider material property, flow/pack/cool process, in-mold constraint (IMC) effect on warpage.
- Enhanced Warp analysis base on transient history effect and couple 3 real physics phenomena:Viscoelastic effect during solidification process, Temperature transient effect, In-Mold constraint in cooling phase. which provide more accurate residual stress of parts in warpage analysis
- To better evaluate large deformation on thin shell part nonlinear Warp analysis with buckling analysis can be applied.
Features
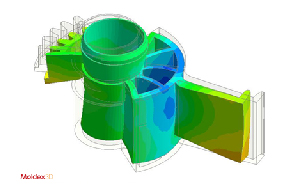
Part Warpage Analysis
- Calculate final part shape due to material shrinkage as the temperature and pressure changes from the process settings to room conditions.
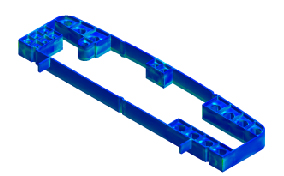
Residual Stress Analysis
- After part ejection, the part shrinks and deforms to an equilibrium shape. At this moment, the remaining stress inside the part is called process-induced residual stress
- Calculate residual stresses developed during the entire molding cycle, including effects of temperature and pressure distributions, material orientation and geometric features
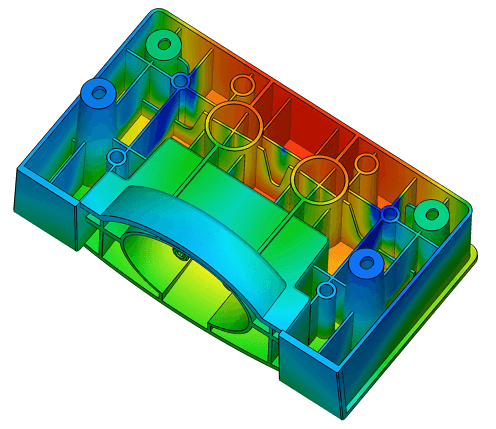
In-mold Constraint Effect Analysis
- Before the part is ejected, the deformation of warpage has been developed inside the mold. However, it cannot shrink and deform freely due to constraints by the rigid mold
- Calculate the part warpage with in-mold constraint to enhance the analysis accuracy