Consulting Service
Moldex3D specializes in developing professional CAE for injection molding. With the complete understanding of CAE technologies, we know how to get the most out of CAE. Furthermore, Moldex3D cooperates with many solution providers, such as material suppliers, sensor/instrument suppliers…etc., to provide not just a CAE report, but a complete solution proposal to our customers. Up to now, Moldex3D has provided more than 8,000 consulting service projects to worldwide customers.
If you have any complex product and process development problems, contact us today!
Consulting Service for Plastic Product Design
We could combine our Moldex3D CAE tools with practical experience for a unique approach to customer’s product development. Plastic product designs must be connected with mold design, materials, process conditions…etc. Our case study service can provide precise analysis results from Moldex3D Flow, Pack, Cool, and Warp simulations for a optimized solution suggestion on product design and process.
Up to now, we have studied over 8,000 industrial cases. This proven technology can help identify production and performance problems while still in the product design stage, eliminating potential problems before the tool is released. Engineering changes can be evaluated to study the effects before production.
The products developed and analyzed by Moldex3D generally perform better and can be molded more profitably. Clients are enjoying the competitive advantage needed to meet aggressive design goals and launch products on time.
Advanced Development Project Service
Based on our expertise in plastic processing, Moldex3D has been helping worldwide users in various kinds of special projects that involve polymer science, compounding, material characterization, process design and optimization…etc.
Successful Cases include
- Development of special mixing device for two-liquid reactive materials: Improvements of a two-liquid static mixing device to enhance homogeneity and reducing pressure drops.
- Optimization and tool design for plastic biological consumables application: Reductions of cycle time and tooling cost for price-sensitive plastic consumables by 40% and 30%, respectively.
- Diagnosis of material degradation in connector manufacturing: Developments of a standard material quality check procedures for virgin and regrind material to guarantee production consistency.
- Identification of plastic composition for better electromagnetic performance: Assistance in plastic characterization of a microwave transmission device that improve quality.
- Balance runner designs of multiple cavity geometrically balanced molds: Implementation of MeltFlipper technology in geometrically balanced mold designs for rheological balance and improved quality.
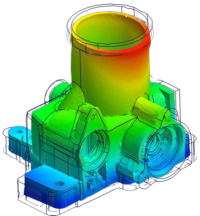
All columns marked with * are mandatory fields to be filled in.