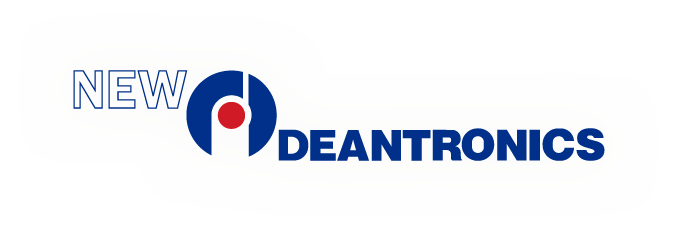
Founded in 1985 in South San Fransico, New Deantronics is the world’s leading medical device manufacturer and developer. With an impressive 25% electrosurgical pencils market share in worldwide medical device market, New Deantronics successfully gained a foothold in global medical devices market with an uncompromising insistence on product quality. The company’s core competency lies in manufacturing and developing high quality RF and high energy based medical devices and accessories.
As the major supplier and partner of world-renowned healthcare companies, including Johnson & Johnson, Philips Medical Systems, and Covidien, New Deantronics put product quality in top priority. New Deantronics aims to provide not only medical products, but a valuable business built on improving people’s healthcare.
Challenges
As New Deantronics is ready for making international expansion move, automatic mass production and cost efficiency will be the essential keys to succeed in the increasingly demanding market. Moreover, due to the global surge in demand for medical devices, how to achieve time-to-market without sacrificing product quality becomes the great challenge of business continuity.
In addition to demanding market challenges, there are still many manufacturing constraints lying ahead. Since healthcare is a highly regulated industry, effective and precise quality control is essential and indispensible to ensure product quality and maintain its high standard. How to manufacture prime quality products within time and cost constraints has raised another challenge for New Deantronics.
Solutions
Verifying design challenges in early stage, however, has demonstrated its competitive edge by meeting high industry standards while minimizing the manufacturing costs. To overcome design challenges and ensure product quality, Moldex3D helps detect the problems in early development stage and present solutions targeting each cause.
Moldex3D targeted design challenges and delivered solutions for a specific design of RF surgery device. Through Moldex3D flow simulation tool, flow hesitation and race phenomenon were observed due to uneven thickness product design. By examining the melt front of original runner design, it was found that when plastic melt enters the cavity, it contacted both thick and thin sections at the same time. Due to material’s heat conductivity, melt temperature in thin section dropped significantly upon completion of filling in the thick section, potentially resulting in short shot. In addition, Moldex3D flow simulation detected high filling pressure from original single inlet runner layout.
In order to prevent short shot and decrease filling pressure without changing the product design, Moldex3D presented design modifications by adding additional inlet and changing the gate locations in runner layout, allowing melt fills in thick section before contacting the thin section (see Fig.2). This can eliminate problem of melt temperature drop and flow hesitation due to uneven thickness, ensuring smooth and uniform fill in the cavity.
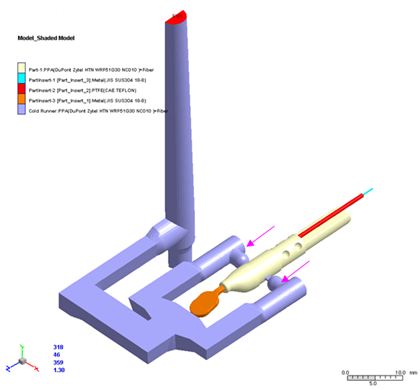
Fig. 1 Design 1 adding additional inlet Design 2 changing the gate location
With the design modifications performed by Moldex3D, New Deantronics gained more ideal and balanced filling pattern but also decreased the overall required fill pressure. The solution helped prevent short shot and enhance product manufacturability effectively. By utilizing Moldex3D simulation capabilities, potential problems such as short shot can be visualized without performing trial-and-error molding tests repetitively. In addition to detecting problems in original design, Moldex3D is able to verify multiple design modifications by conducting simulation iteration to achieve optimized design in timely manner. Moldex3D has delivered solutions and technical supports to fulfill New Deantronics’ product standard and maintain its high quality as the world’s leading medical device developer.Results and Value Derived