Jasmine Ho, Engineer at Technical Support Team, Moldex3D
Formosa University upholds its motto of “Integrity, Righteousness, Mastery, and Diligence” while prioritizing student-centered education. The university aims to cultivate practical professionals urgently needed by society, equipping them with skills with interpersonal interaction, self-growth, cultural literacy, global mobility, creativity, interdisciplinary integration, information technology and technical expertise. By fostering industry-academia collaboration and strengthening national competitiveness, NFU addresses future addresses future challenges through talent and research development, campus culture.
Summary
This study utilized Moldex3D to optimize the design of a large storage basket, aiming to reduce product thickness and refine parameters to improve warpage and volume shrinkage rate. After optimization, the rib size was reduced from 3 mm to 2.5mm, achieving a 20% reduction in warpage and 7% decrease in volume shrinkage rate while still supporting a 35 kg load capacity, successfully meeting the optimal design goal.
Challenges
- Design a thinner rib structure to reduce thickness while addressing volume shrinkage rate and warpage.
- Maintain the same loading capacity as the original product while reducing injection molding time and cost.
Solutions
The National Formosa University team employed Moldex3D’s Expert Simulation to determine the optimized solution, which was integrated with Abaqus’s Finite Element Analysis to simulate product’s load-bearing capacity. Final validation was achieved through injection molding production results.
Benefits
- Improved product quality, reduced warpage and volume shrinkage rate
- Meet the load capacity specifications
- Lowered production costs and time
Case Study
Initially, this study began by reducing rib size from original design 3mm to optimized design 2.5mm (as shown in Fig 1). Using Abaqus structural analysis, a 35kg distributed load was applied internally. The original design was 22.7 MPa
The original design employed a stress of 22.7 MPa, while the optimized design reached 36.3 MPa, both below the material’s yield strength, confirming safety. The reduction led to a 22.75% decrease in part volume. Figure 2 presents Abaqus stress analysis results for 3mm and 2.5 mm rib thicknesses.
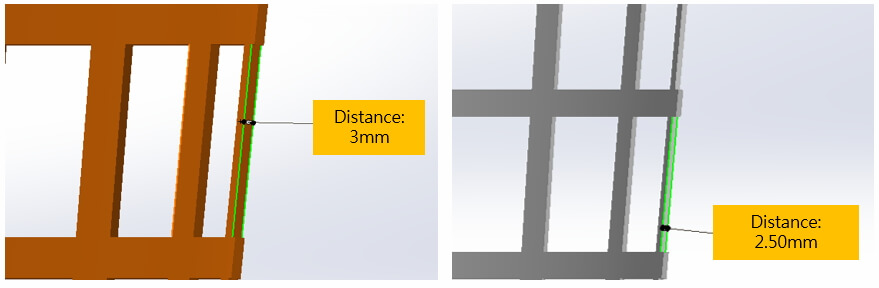
Fig 1. Large storage basket rib thickness–original design: 3mm, optimized design: 2.5mm
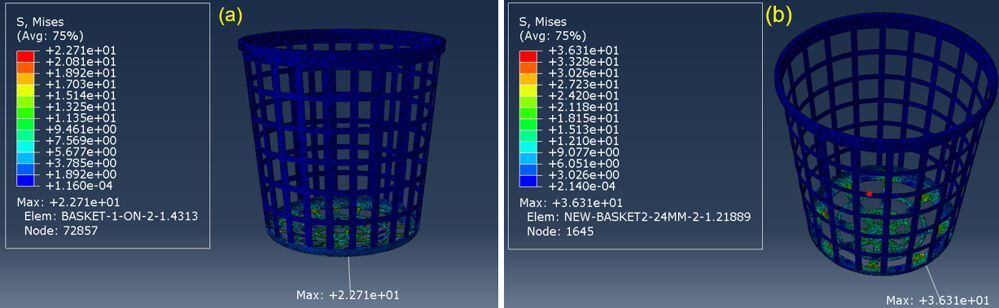
Fig 2. Abaqus stress analysis results for large storage basket : (a) 3mm rib thickness (b) 2.5 mm rib thickness
To further reduce warpage and identify optimal process parameters, the NFU team utilized Moldex3D Expert Simulation, setting total displacement and volume shrinkage rate as quality factors, aiming to minimize both. Six key parameters were selected as control factors: plastic temperature(A), mold temperature(B), maximum injection pressure (C), maximum packing pressure(D), cooling time(E), and packing time(F). These were analyzed for the 2.5mm rib thickness design using the L18 Taguchi Method.
Table 1: Taguchi Methods for Design of Experiments (DOE)
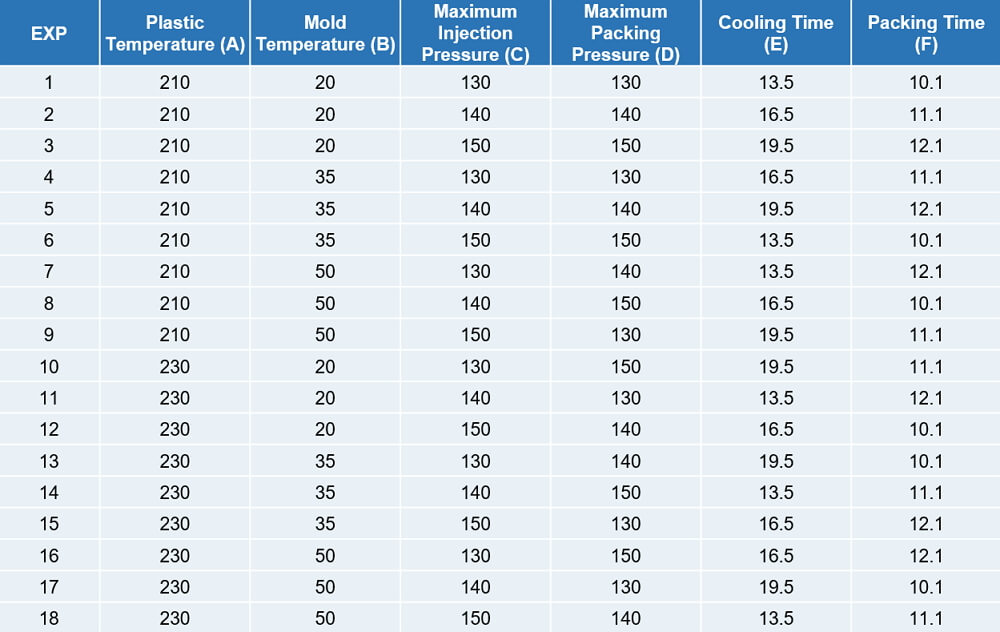
Analysis revealed the control factors in the following orders: plastic temperature, packing pressure, injection pressure, packing pressure, cooling time, mold temperature. The optimal parameters are displayed in table 2.
Table 2. Optimized molding parameters
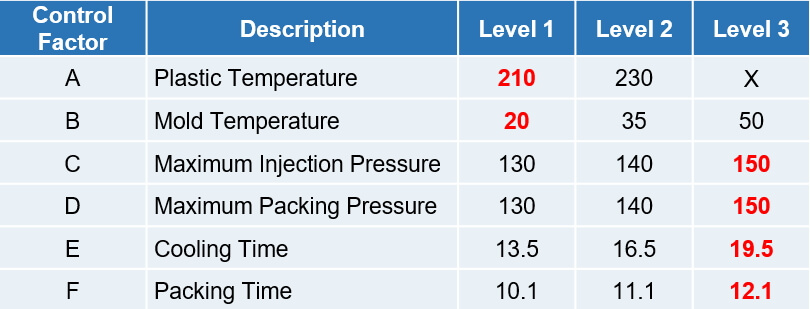
Implementing these optimized parameters, the maximum displacement dropped from 8.063 mm to 6.29 mm; a 28.1% reduction. The maximum volume shrinkage rate decreased from 10.557% to 9.436%, an 11.8 % reduction.
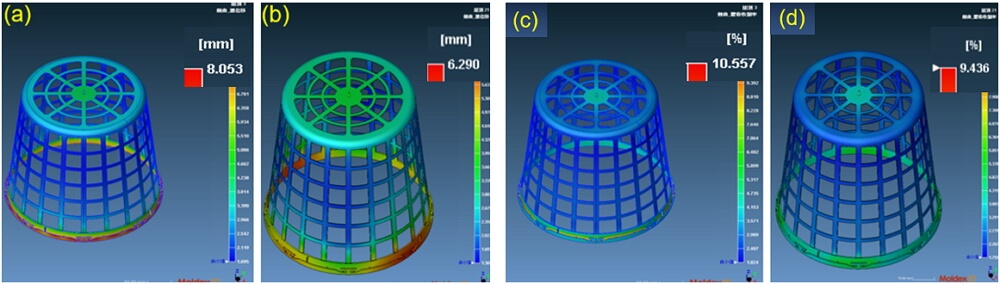
Fig 3. The design of a large storage basket 2.5mm rib thickness (a) original condition total displacement (b) optimized condition total displacement (c) original condition volume shrinkage rate (d) optimized condition volume shrinkage rate
This study verified the accuracy of simulation using real injection molding results. A measuring tape was utilized to measure the total displacement at five diagonal red points (as shown in Fig 4), with four sets of data recorded (as shown in Table 3)
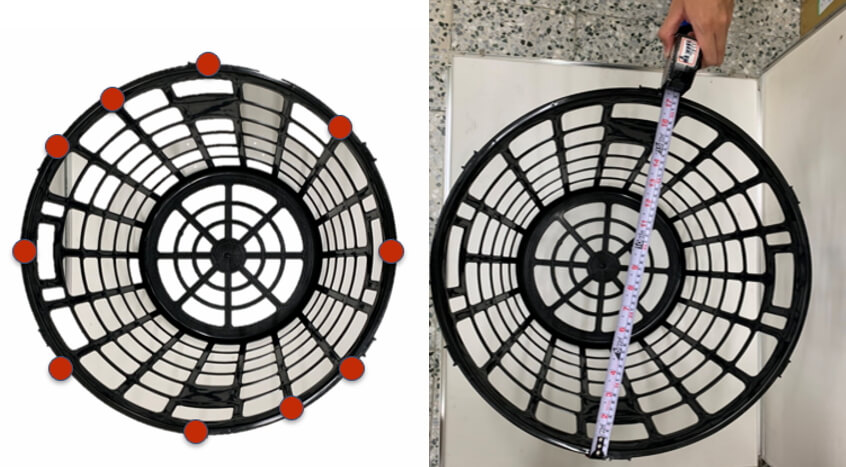
Figure 4. Warpage measurement diagram of actual injection part
Simulation predicted a warpage magnitude of 6.29 mm. Given the basket’s designed width of 535 mm, the post-injection predicted dimension was 528.71 mm. The average measured value from the experimental data in Table 3 was 529.4 mm, which falls within the design range of 528.71 mm to 535 mm, confirming the high accuracy of the simulation in this study.
Table 3: Measured warpage data of real injection molding product
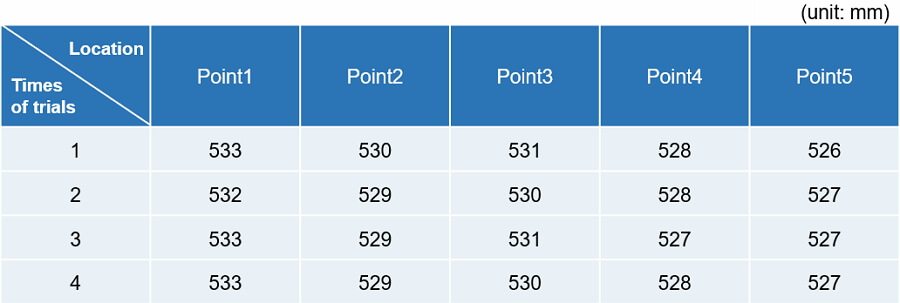
Conclusion
This study successfully optimized a large storage basket using the Moldex3D simulation software, reducing rib thickness from 3mm to 2.5mm and achieving thickness reduction and parameter optimization. The optimized product could still withstand a 35 kg load, with a 22.75% reduction in volume, a decreased warpage of 28.1%, and a volume shrinkage reduction of 11.8%. Integrating Abaqus Finite Element Analysis with physical injection molding experiments, the validated results matched the set goals, providing strong evidence and confidence for designs balancing lightness and structural strength.