- Customer: BASF
- Country: Germany
- Industry: Consumer Products
- Solutions: Moldex3D Advanced Package; Flow, Pack, Warp, Gas-assisted Injection Molding (GAIM), FEA Interface
The approximately 122,000 employees in the BASF Group work on contributing to the success of their customers in nearly all sectors and almost every country in the world. Their portfolio is organized into six segments: Chemicals, Materials, Industrial Solutions, Surface Technologies, Nutrition & Care and Agricultural Solutions. (Source: https://www.basf.com/global/en/who-we-are.html)
Summary
A designer chair made of fiber-reinforced plastics (FRP) from BASF was manufactured using GAIM (Gas-assisted injection molding). However, the gas fingering problem occurred during production and led to reduced strength. Since design changes were not allowed, BASF engineers were tasked with optimizing the GAIM process conditions to reduce part weight without sacrificing strength.
Challenges
- Gas fingering
- Poor mechanical properties
- Not allowed to make any design changes
Solutions
With the use of Moldex3D, BASF engineers were able to minimize gas fingering by optimizing process conditions. As a result, the chair met the weight requirement and gained better structural integrity at the same time.
Benefits
- Predicted gas fingering
- Increased part strength by 60%
- Met weight and load requirements
Case Study
In this project, BASF used Moldex3D to run a prospective simulation of gas-assisted injection molding (GAIM) to analyze a designer chair. They faced a major problem of gas fingering inside the sitting surface and the backrest of the chair. The structural integrity of the chair would cause it to fail with loadings. As the chair is a designer chair, the mold is already manufactured, and there is no room for mold modification development in the design end. Thus, to make the chair take prescribed loads, the task was to only optimize the processing parameters.
In the results original design, the center temperature at GAIM switchover has less than 2 °C of difference between the thick region and the thin region (shown in Fig. 1). In other words, gas enters easily into the thin region (causing the gas fingering effect) due to similar resistance to flow as the thick regions. It indicates that the gas will not enter the thin region when the temperature difference between the two is significantly larger. Thus, increasing the gas delay, filling and packing time could help in optimizing the process.
Fig. 1 The simulation results of the center temperature
They optimized the process with various combinations to improve the results, which are increasing the filling time to 6 sec, packing time to 10 sec and gas delay time to 15 sec. Fig. 2 shows the optimized result in which the gas core confines in the required area only.
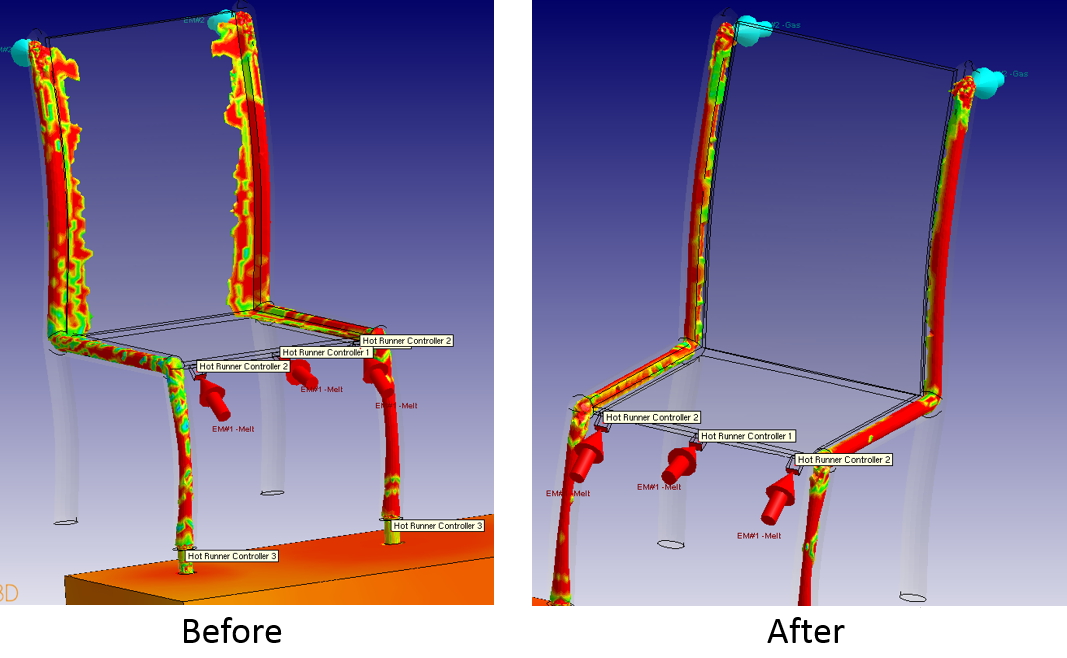
Fig. 2 The tendency of the gas core before and after the optimization
With the optimized setting, the difference of center temperature between the thick region and the thin region is 7 to 10°C (Fig. 3), which means the gas cannot enter the thin regions and travels in the region with higher temperature (thick region) due to the least resistance to flow.
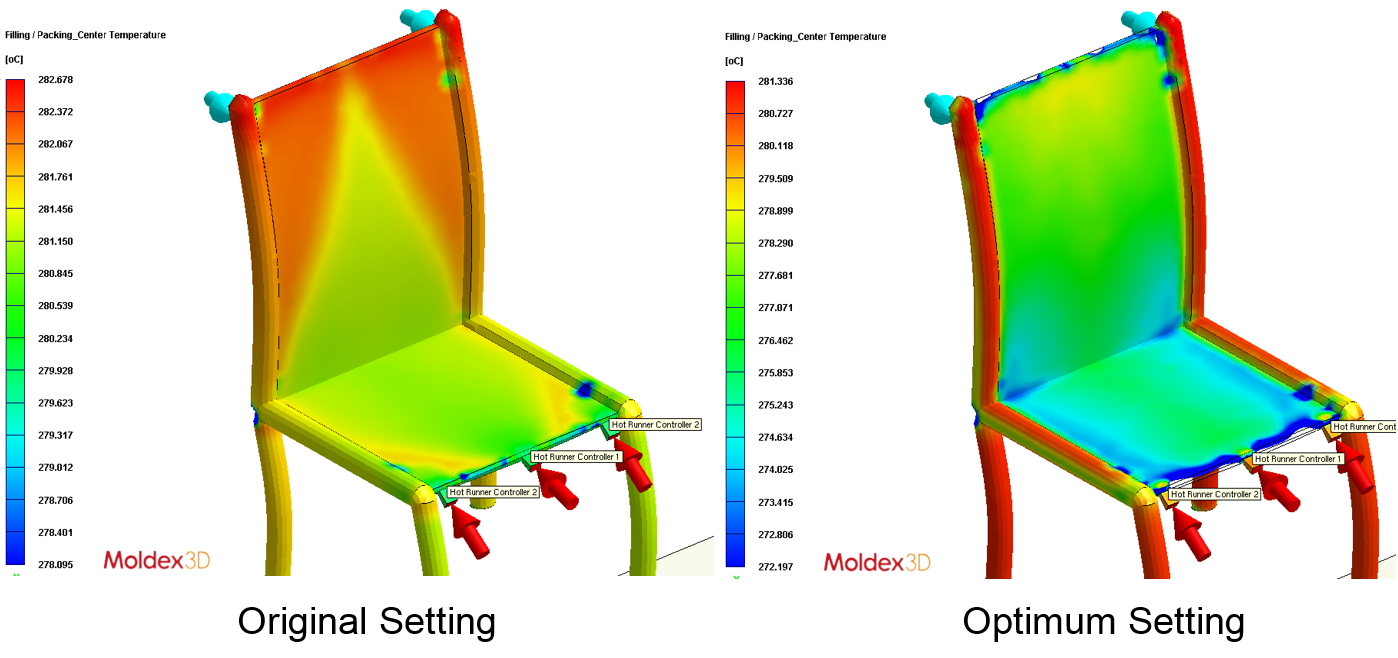
Fig. 3 Comparison of the center temperature between the original and optimized settings
Moldex3D supports exporting the simulation data to other FEM software with further structural simulation. In this case, BASF used the simulation results from Moldex3D to validate the problem statement that the chair manufactured with the given process settings fails mechanically in Abaqus. Fig. 4 shows the force at failure for the chair with the optimum setting is 60% higher than the original setting. It also illustrates that the displacement at failure for the chair with the optimum setting is 11.5% higher than the original setting.
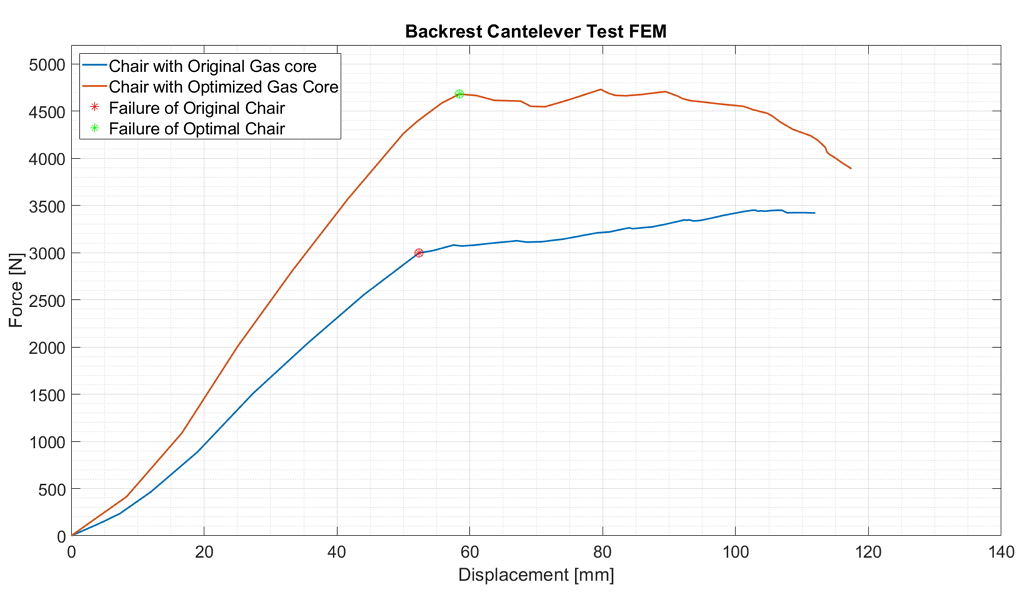
Fig. 4 Displacement vs Force comparison using Abaqus
Results
With Moldex3D, the gas-assisted injection molding can be easily simulated and optimization studies could be carried out. The feature of the center temperature simulation is especially useful for GAIM process. Moreover, the FEA interface in the Moldex3D helps in acquiring data for further complex FEM processes used in the industry and the exported data could be read easily by other programs and worked upon.