- Customer: Delta Group
- Industry: Electronics
- Solution: Moldex3D Advanced Package
- Country: China
Executive Summary
When a computer is operating, waste heat will be generated, produced by computer components. In order to reduce the temperature, cooling modules have been widely used to provide cooling for the computers. Delta Group has been cultivating its expertise in developing innovative products for decades. Delta adopted Moldex3D injection molding simulation solutions years ago for design validation and process optimization. In this case, Delta used Moldex3D to predict potential molding problems of the cooling fan bracket before production, and further optimized process parameters to improve part quality and reduce production costs.
Fig. 1 The fan bracket in a computer’s cooling module
Challenges
- Severe part deformation caused by residual stress
- Failed to meet the flatness requirement of 0.2mm
Solutions
Delta Group utilized Moldex3D eDesign to quickly diagnose the root cause of part deformation and obtained feedback on product design changes. With that, Delta was able to determine the optimal design with minimum deformation through mold trials.
Benefits
- Reduced deformation from 0.3mm to 0.15mm
- Decreased defect rate from 45% to 16%
- Shorter cycle times and lower costs
Case Study
The function of a cooling fan bracket is to mount and support cooling components. Its flatness is critical to the success of the assembly operation. In this case, the shrinkage caused the corners of the cooling fan bracket to collapse, which failed to meet the required dimensional specs of 0.2mm. Therefore, the main purpose here is to improve the dimensional stability.
Fig. 2 Shrinkage caused the corners of the cooling fan bracket to collapse and exceeded the dimensional tolerance
Fig. 3 The warping deformation of the part is 0.3 mm
In order to effectively improve the product quality, Delta Group’s R&D Team utilized Moldex3D’s filling, packing and cooling analysis modules to identify and address problems in the original design.
Figure 4 shows the filling analysis result of the original design. The part had strength issues due to structural inconsistency. The corner was filled at the end of filling and resulted in poor packing. This can lead to part shrinkage and affect the part strength.
Fig. 4 The filling analysis result
As shown in Figure 5, the temperature distribution analysis result showed the end of packing temperature is still higher than 230℃ (yellow color). This would lead to non-uniform shrinkage induced by internal heat concentration in the thick region.
Fig. 5 The packing temperature distribution analysis result
Figure 6 shows the cooling analysis result. It shows heat concentration at the end of cooling (red color), which might cause warped part and prolong the cooling time.
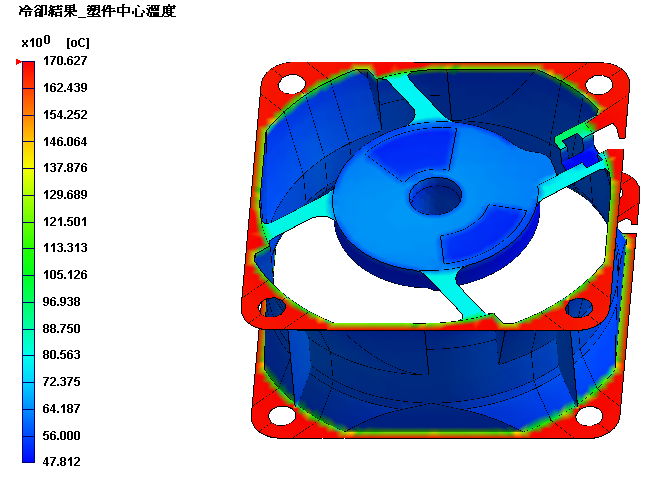
Fig. 6 The cooling analysis result
After identifying the root cause of the problem, Delta Group leveraged Moldex3D Warp analysis to compare the revised designs with the original one; they are rib (Original Design), double ribs design (Revised Design 1) and double ribs with cylinder (Revised Design 2). The comparison between the three different designs helped Delta Group observe Z-displacement changes, which became a valuable reference for evaluating the deformation of bracket corners. The analysis result showed that Revised Design 2 is the best possible design, which kept warpage at the minimum, between -0.39mm to 0.36 (Fig. 7 and 8).
Original- Single Rib |
Design change 1. |
Design change 2. |
![]() |
![]() |
![]() |
Z-axis deformation: -0.57~0.38mm |
Z- axis deformation: -0.41~0.37mm |
Z- axis deformation: -0.39~0.36mm |
Fig. 7 After comparing 3 designs through Moldex3D, Delta Group was able to determine Revised Design 2 as the most optimal design with minimum Z-displacement.
Fig. 8 Delta group was able to determine that double ribs plus cylinder is the optimal design with the help of Moldex3D simulation software.
Results
Moldex3D simulation solution has proven to be a highly reliable asset for Delta Group by finding that simulation results are highly correlated with real-world results. The Z-displacement was reduced by 20%, from 0.3mm to 0.15mm. In addition to saving time and money, the defect rate was reduced from 45% to 16%, shortening the development cycle by three days.