Why Fiber Analysis?
Fiber reinforced plastics (FRP) have been widely applied in industries as a major material in order to reinforce thermal and mechanical properties of plastics with small changes on weight. Fiber length, orientation and concentration have a great impact on these properties. Part strength can be highly enhanced by raising the fiber length; simultaneously, fiber orientation induced by the flow shear in the molding process causes anisotropic properties to plastics. To maintain the stability of product quality, the predictions on fiber length and orientation become very important for users to obtain the optimal designs and process conditions.
Moldex3D Fiber provides accurate and detailed simulations of 3D fiber orientation, which helps users control anisotropic shrinkage for fiber-reinforced parts. Mechanical properties due to fiber orientation can also be visualized and analyzed for warpage prediction. With its accurate fiber orientation and anisotropic shrinkage predictions, users can achieve warpage control, cost reduction and strength improvement.
Challenges
- Predict fiber orientation, length breakage and concentration for short and long fiber reinforced plastics
- Define fiber length, diameter, and concentration in evaluating shrinkage and warpage
- Control the strength of parts and welding line regions
- Support orientation simulation for different types of filler (short/long fiber, flake, etc.)
- Consider anisotropic thermal and mechanical properties
What Can Moldex3D Fiber Do?
-
Predict anisotropic property distributions using fiber reinforced composite models: elastic modulus, linear thermal expansion coefficient (CLTE), mechanical properties
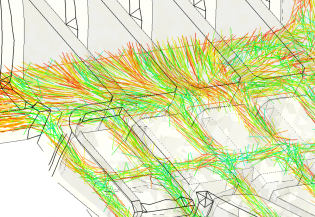
Fiber orientation prediction
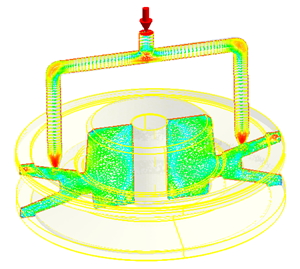
Dynamic slicing of fiber orientation
-
Support 3D fiber orientation analysis with the Folgar-Tucker model, ARD model and iARD-RPR model
- Apply Improved Anisotropic Rotary Diffusion (iARD) technique combined with the Retarding Principal Rate (RDR) model
- iARD-RPR is a modeling methodology with patent protection registered under Moldex3D
- Accelerating computation: A new closure form of the fourth-order orientation tensor is developed to accelerate fiber orientation computation by at least 40-50%, without requiring user-specified inlet-condition
- Evaluate significant characteristics of long fiber orientation considering matrix structure, fiber flexibility, etc.
- Focus on fewer model parameters, provide friendly suggestion of optimal default parameters for short/long fibers
- Especially enhances the core region with a perfect accuracy
Fiber orientation prediction: great agreement between results by Moldex3D and experiment
-
Predict fiber length distribution
- Visualize fiber length distribution of the part after the filling phase
- Allow to observe fiber breakage phenomena around the gate region
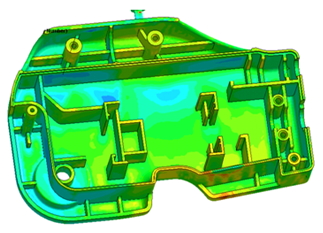
Long fiber distribution (initial fiber length: 8.5 mm)
-
Support flake orientation analysis
- Predict mechanical properties and warpage based on flake orientation
- Predict flow marks and welding lines on the surface of the part
Dynamic slicing of flake orientation
-
Output anisotropic thermo-mechanical properties through Moldex3D FEA Interface and Moldex3D Digimat Interface to be utilized by mainstream structural analysis programs.
Applicable Industries
- Electronics
- Automotive
- Medical
- Consumer Product
Applicable Moldex3D Package
- Moldex3D eDesign Basic Package
- Moldex3D eDesign Package
- Moldex3D Professional Package
- Moldex3D Advanced Package