Authored by
Venny Yang, President at CoreTech System (Moldex3D)
Sam Hsieh, Senior Deputy Technical Manager at CoreTech System (Moldex3D)
In 2016, ANSYS has become the first engineering simulation software company to achieve annual revenue of over $1 billion. This revenue scale not only surpasses most CAD/CAM software companies but also officially declares the era of CAE-driven design has arrived. In February 2017, Hexagon AB, the world-leading company of precision measuring machines, acquired MSC Software, one of the most experienced companies in CAE software industry, for $834 million. This acquisition represents a big step for hardware companies to enter the digitalized design, and it indicates the measurement data in real manufacturing environment will be closely integrated with the simulation analysis to help the enterprise break the limits in part design optimization and traditional production and leads the manufacturing industry to boldly set foot on the journey to Industry 4.0. These transitions and integrations will continuously drive creation and innovation in global electromechanical and related industries, containing all parts in a small scale. The same design optimization and the evolution of simulation technology also take place in a circular process in the world of injection molding and mold design.
Role transition of mold filling analysts
In the beginning, mold filling simulation was only applied to the diagnosis of plastic part design to solve production problems. Currently, it has evolved into a tool that is massively used on early design, verification, and optimization of part and mold development and plays an essential role in design and manufacturing processes in most enterprises. During the process of this evolution, the widespread application of full-3D CAD software for part and mold design contributes the most, but it can never be successful without the automatic mesh generator. In the early days, it usually required analysts to spend hours, even days, on modeling and meshing before analyzing. Now, with the fully automatic eDesign and Boundary Layer Mesh (BLM) mesh generator, meshing can be done with only one click and the mesh can be updated synchronously with part modification. Therefore, the task of standard mold filling analysis has gradually shifted from the professional CAE analyst to the mold designer, even to the product designer at the upper stream. Product and mold designers are used to relying on the analysis software to determine the position of sprue, balance the runner design, optimize the cooling channel deployment, solve warpage, etc. Moreover, many companies have started to embed the core of mold filling analysis in their internal design guide platforms to realize the design quality management ideal in which every part is processed by mold filling analysis to automatically inspect the upper limit of injection pressure, shrinkage, and warpage. Meanwhile, by working with a parallel computing cluster on the private cloud, the computing time can be significantly reduced, and the response speed is improved.
To help users save considerable time as well as generate the appropriate 3D runner mesh for mold filling analysis, a new generation of automatic high-quality runner mesh generator is developed in Moldex3D R15.0. The new runner mesh technology can automatically create hexahedral mesh with high resolution, provide users with various node types to connect line runner junctions, truly reflect the original geometric shape of runners, and further save computing time as well as improve simulation accuracy.
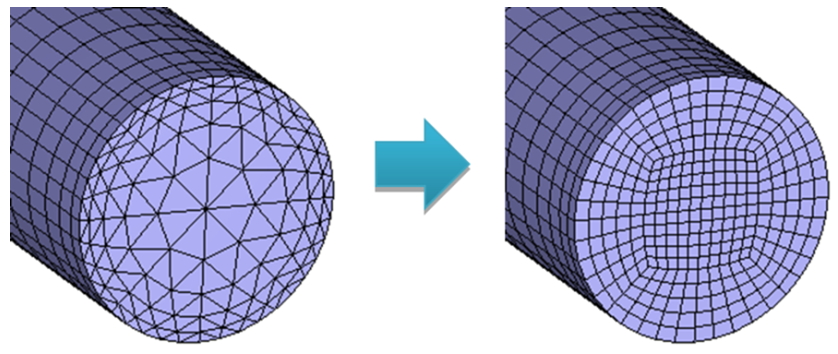
Fig. 1 Hexa-based solid mesh
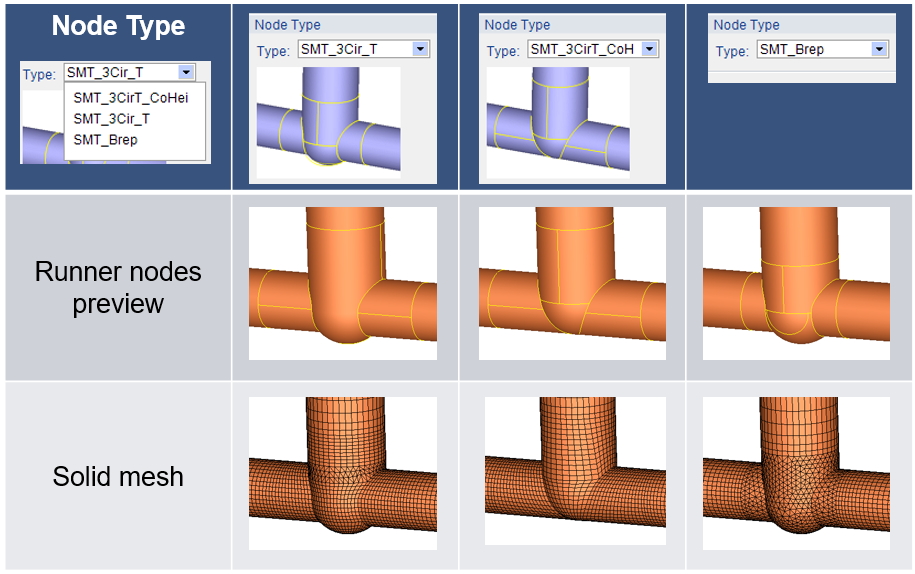
Fig. 2 Various features, such as node types and node preview
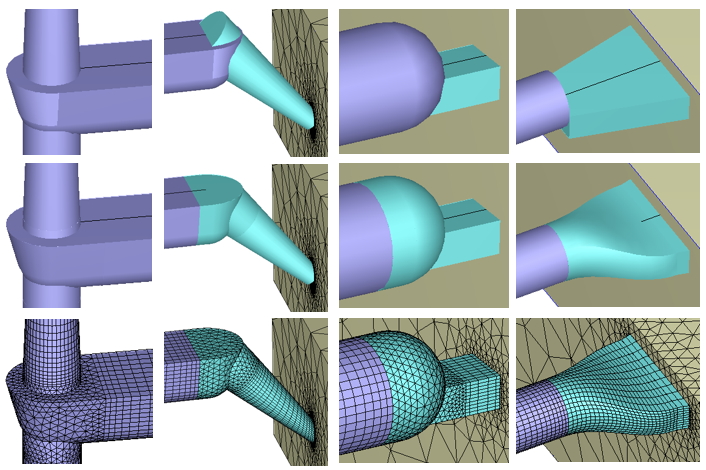
Fig. 3 Enhanced functions for sprue design; users can create mesh by choosing commonly-used node types
With the emergence of “non-matching mesh” technology, users can go straight to the simulation analysis to get accurate simulation result and the deformation prediction of interconnected parts even when the mesh interface between the part and the part inserts does not continuously match the quantity. In Moldex3D R15.0, the non-matching mesh technology, which used to support the part inserts only, is now extended to support the mesh of mold base as well. This technology surmounts the restriction that a 3D solid mold base mesh cannot be pre-processed automatically when mesh nodes of the part and the part inserts are not matching and enables users to accelerate mold base mesh preparation and experience efficient and accurate simulation analysis realized by high-quality mesh technology.
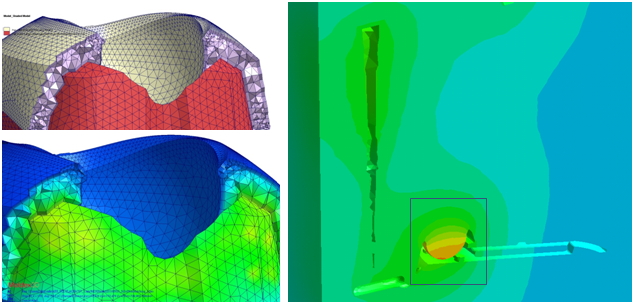
Fig. 4 Non-matching mold base mesh and analysis result
From simulation to perfect emulation
The demands and expectations from engineers to CAE software are endless. Besides the simulation analysis of standard injection molding process, the mold analysis function also covers special processes, for example, injection compression molding, compression molding, and metal injection molding. As the proven functions of Moldex3D, fiber orientation and FEA-integrated analysis of short and long Fiber Reinforced Plastics (FRP) during the injection molding process are approved and introduced by automobile manufacturers using advanced technologies and the leading manufacturers of engineering plastics all over the world. In Moldex3D R15.0, these benefits are further extended to the compression molding process analysis of FRP to assist users in designing and optimizing the manufacturing process of large-scale FRP.
In addition to the full support of FRP processes, as the requirements of lightweight and fuel-efficient vehicles keep increasing in recent years, Moldex3D has already integrated advanced molding technologies, such as gas-assisted injection molding, water-assisted injection molding, microcellular foam injection molding (typical technology: MuCell® by Trexel), and chemical foaming of thermoplastics into the scope of simulation prediction and obtained excellent verification data and user experience. Furthermore, the latest R15.0 chemical foaming module additionally supports PU (polyurethane) foaming process and considers the curing kinetics when the glue is in the die cavity and the computing of foaming kinetics. Through PU foaming simulation analysis, users can have a clearer insight into the manufacturing process, accurately predict the dynamic behaviors during filling and foaming stages, identify the optimized control of injection conditions and material injection, refine the part design, and evaluate and determine the ideal manufacturing conditions easily.
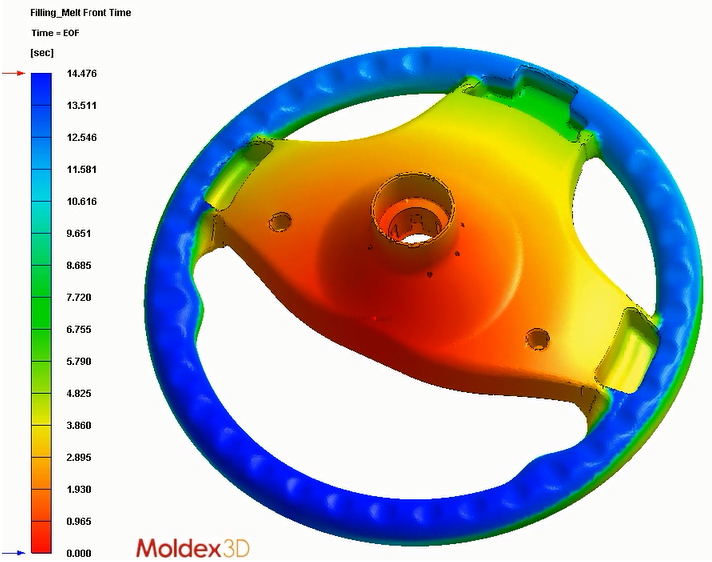
Fig. 5 Application of PU chemical foaming process
Though the manufacturing of In-Mold Decoration (IMD) injection molding is getting popular in recent years, it still faces challenges from molding processes, such as ink wash-off and wrinkle deformation, which result in a higher cost and delay of product development schedule. Moldex3D R15.0 offers professional analysis functions to support boundary options of thin films in the preprocessing procedure in IMD simulation and helps users process the mesh layer of decorative pieces with the fastest, simplest, and the most accurate approach. Furthermore, this latest version also provides “wash-out index” to enable designers to predict washout status and ensure the output of high-quality in-mold decorative products.
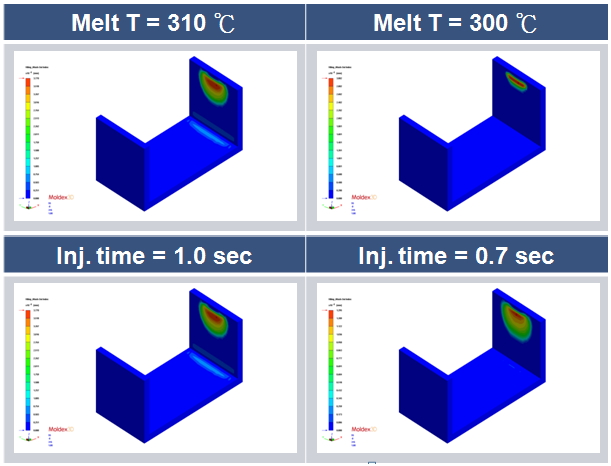
Fig. 6 Comparison of the wash-out index results under different molding conditions
With the analysis, users can predict the flow front identical to actual results, and gain insight to the heat hesitation during the molding process by considering the heat transfer effect of thin films; this phenomenon is caused by a weaker heat transfer ability of the decoration layer.
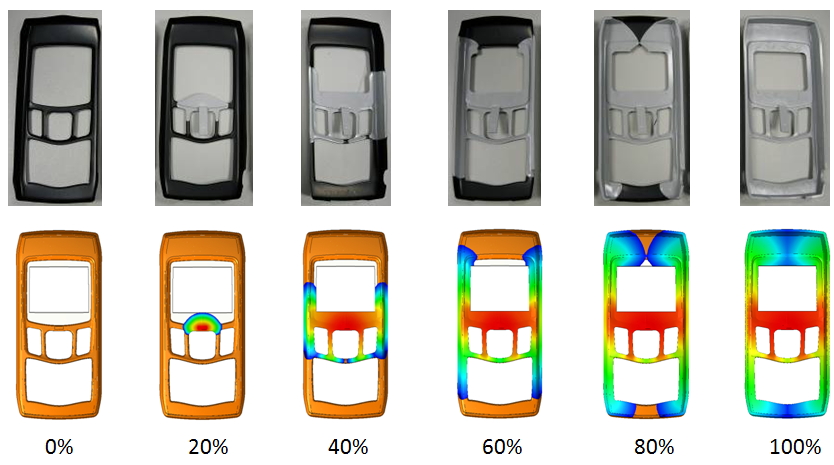
Fig. 7 Comparison of melt flows and experiment results
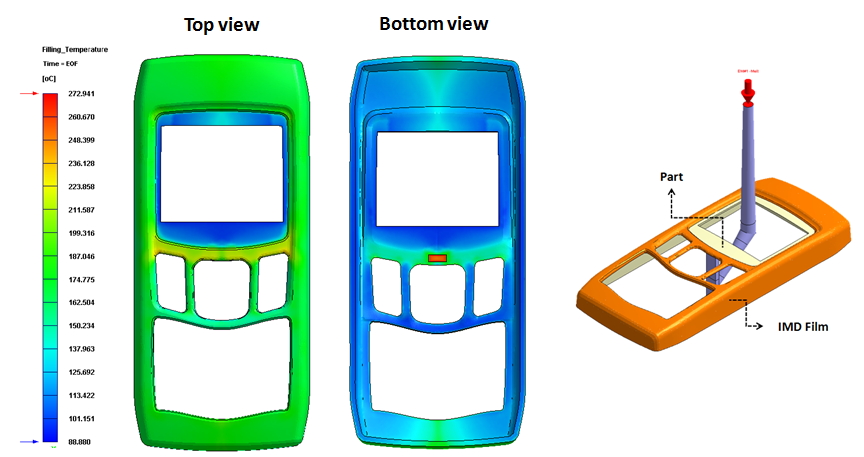
Fig. 8 IMD analyzes the temperature distribution on part surface
3D printing is another new technology that has started to change mold design. As there are more and more suppliers all over the world investing in this market, the price of a 3D metal printer is becoming cheaper and the cost of metal powder is decreasing yearly. The printing of small- and medium-sized molds is not a dream anymore. Heat power accumulation that often occurs around the ribs and holes of medium- to large-sized molds can also be eliminated by integrating traditional mold manufacturing processes and 3D printing. Besides remarkably decreasing the types and numbers of required processing equipment, the biggest benefit is the flexible cooling channel design. 3D conformal cooling can easily cool all corners of the mold; it can significantly save cooling time and decrease the warpage and sink mark on product surface. In the design stage, the conformal cooling channel designer offered by Moldex3D can save the time for creating cooling channels, utilize 3D CFD to check if the turbulent flow in every channel is sufficient to ensure the cooling efficiency and evaluate the required pressure and specification of cooling pump. The traditional and conformal cooling channels in the mold are then evaluated by the combination of cooling and warpage analyses to assess the manufacturing cost of mold, cooling time reduction under mass production, and the manufacturing cost with enhanced stable quality and efficiency. As stated previously, the widespread utilization of 3D printing technology on mold manufacturing is rapidly changing the landscape of mold manufacturing and leading the popularization of conformal cooling channels.
The emerging trend of “cloud” Embrace Industry 4.0
The emerging trend of cloud computing substantially drives the development of e-commerce and AI, gradually makes it one of the important options when CAE software suppliers and users consider the investment and deployment of next-generation computational resources. As the confidentiality of design information stored in public clouds is still questionable, many enterprises have introduced cluster computing architecture internally to correspond to the requirements of macro memory and computing time of CAE computing. For example, the well-known CAE software, like ANSYS and ABAQUS, has already provided support to cluster computing. The use of parallel processing capability of LS-DYNA to simulate vehicle crash on thousands of cores is a routine analysis and verification task for the automotive industry. Similarly, as the leader of mold filling analysis software, Moldex3D can easily satisfy the computing requirements of 10 million-level project by making the computing over 10 times faster through the serial connection of several standard PCs. When the same configuration is deployed on the cloud, it can meet the computing requirements of numerous users immediately. Users with less or unexpected usage demand can take advantage of the flexible pay-per-use license to obtain the software and hardware resources necessary for computing. As the technologies like intellectual property protection, network security, and transmission bandwidth are getting more mature, enterprises start to open their minds viewing the benefits brought by cloud computing more. The coming cloud computing by Moldex3D is a capability that all enterprises should keep an eye on.
When there are more and more members using mold filling analysis to improve the business competitiveness in design, manufacturing, and production processes, it means more computing data will be generated; this data, through the integration with various data measured on site and being imported to the big data base containing valuable manufacturing experiences, forms the essential base for enterprises on the journey to Industry 4.0. The iSLM module in Moldex3D R15.0 will help users manage and analyze this data as well as explore more priceless design, manufacturing, and production experience.