What’s New in Moldex3D R15
Simulation can help you make quick and informed decisions in the early design phase. But problem is, simulation preprocessing is all too often time consuming and laborious.
Moldex3D R15.0 offers enhanced performance, accuracy and better usability to streamline simulation workflow and provide faster turnaround times with added efficiency.
Here’re the top most exciting features in Moldex3D R15.0 that will enhance your next simulation projects and results, saving you significant time and effort. Get your next simulation project done faster, more efficiently with Moldex3D R15.0.
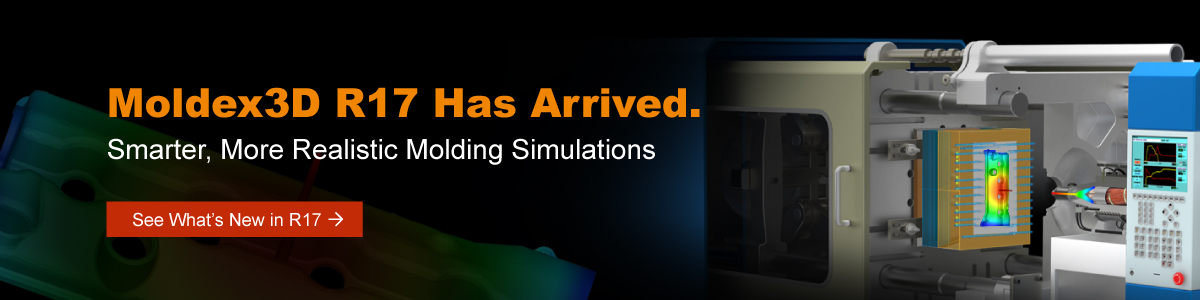
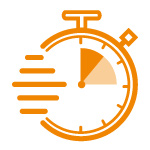
Sharply Reducing Pre-processing Time in Half
While Maintaining The Highest Accuracy
|
Achieve High-quality Runner Mesh in Significantly Less Time
Runner modeling is critical to simulation accuracy. New Moldex3D runner meshing technology enables automatic generation of hexahedral meshes to reduce time and manual effort required to obtain a high-quality mesh as well as the intended geometric shape.
|
|
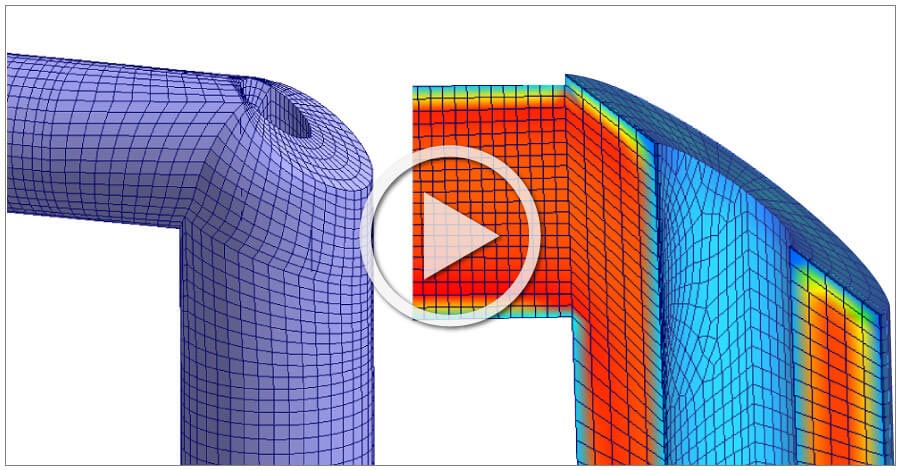 |
|
|
|
Generate a Complete Mold Mesh Faster and Easier
Automatic creation of non-matching mesh connections between part and part insert /mold base to obtain simulation results faster with minimal effort. Learn more>>
|
|
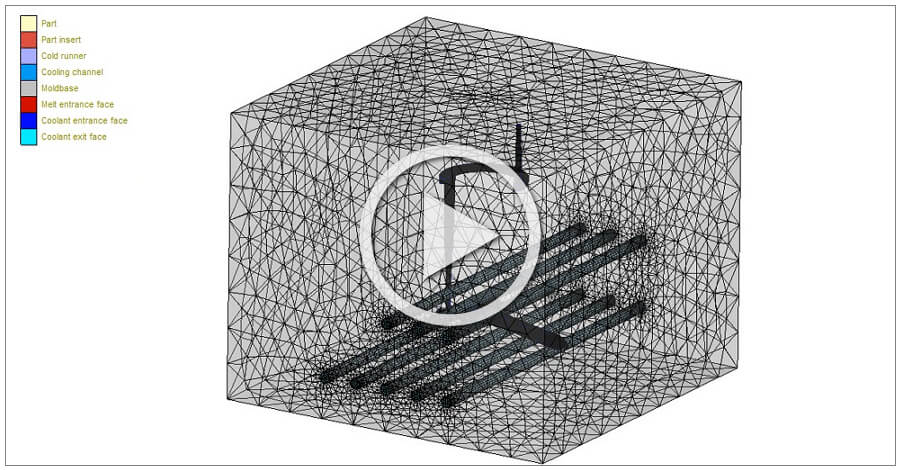 |
|
|
|
One Platform to Speed Up Simulation Workflow and Efficiency
Moldex3D Studio offers you a choice to streamline all phases of your simulation workflow- from pre-processing to post-processing onto an intuitive, ribbon-style interface. The new platform also enables users to compare various design iterations simultaneously to shorten product development time.
Learn more>>
|
|
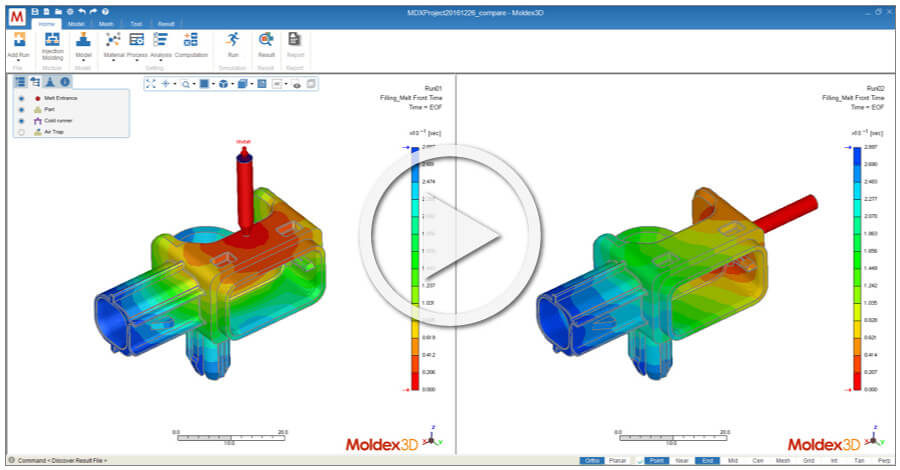 |
|
|
|
Enhanced In-mold Decoration (IMD) Simulation
Boundary condition type is now available in the pre-processor to help you prepare decoration layers for simulation faster without a ton of manual effort. The new “Wash-out Index” feature will enable designers to better predict washout of the ink of the decoration film to ensure successful decorative products.
|
|
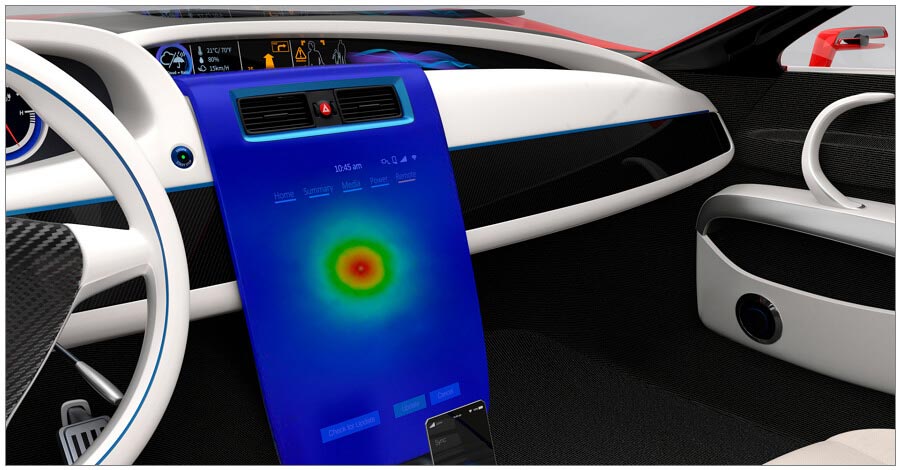 |
|
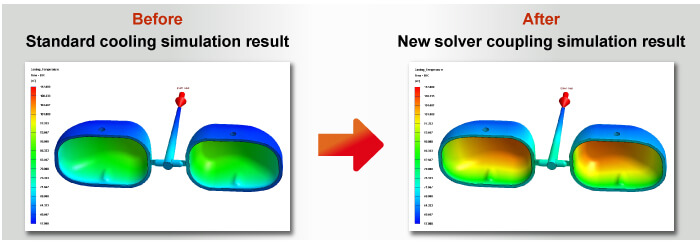 |
Fully Coupled Process Simulation to Satisfy Specific Needs for High-precision Plastic Parts
Users can perform high-end simulations to enable more realistic results using the new Fully Coupled Process Simulation technology, which can run Flow/Pack/Cool/Warp solvers simultaneously to yield optimal accuracy.
|
|
|
Continuing Advancements in Simulation for
Lightweight, High-performance Plastic Products
|
New Simulation Capability for Polyurethane (PU) Chemical Foaming Process
In addition to the already existing microcellular foaming process analysis, Moldex3D R15.0 introduces new capability for simulation of polyurethane (PU) chemical foaming process, enabling product engineers to predict the density distribution of the final part before production, ensuring a desired volume-to-weight ratio. Learn more>>
|
|
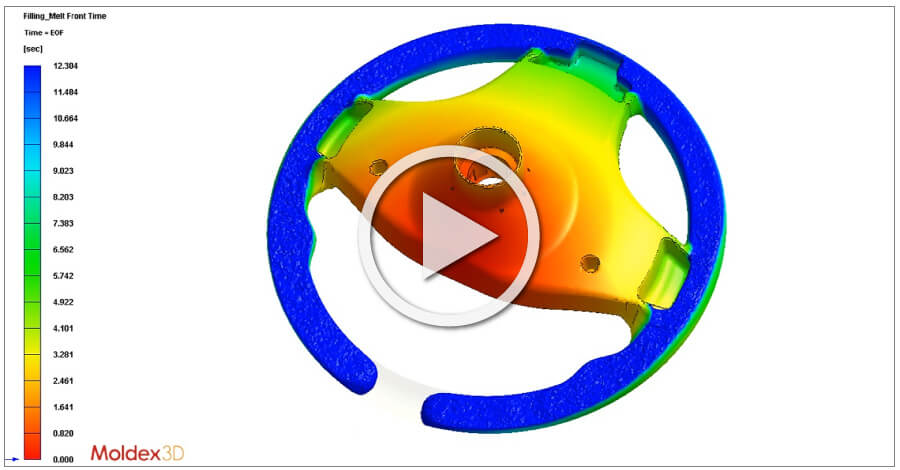 |
|
|
|
Extended Simulation Capability for Compression Molding of Sheet Molding Compound (SMC)
Moldex3D R15.0 also includes enhancements in the compression molding analysis of sheet molding compound (SMC) to enable a more accurate simulation of the full compression molding process- going from solid to molten and back to solid state, through a tighter integration between Moldex3D and LS-DYNA.
Learn more>>
|
|
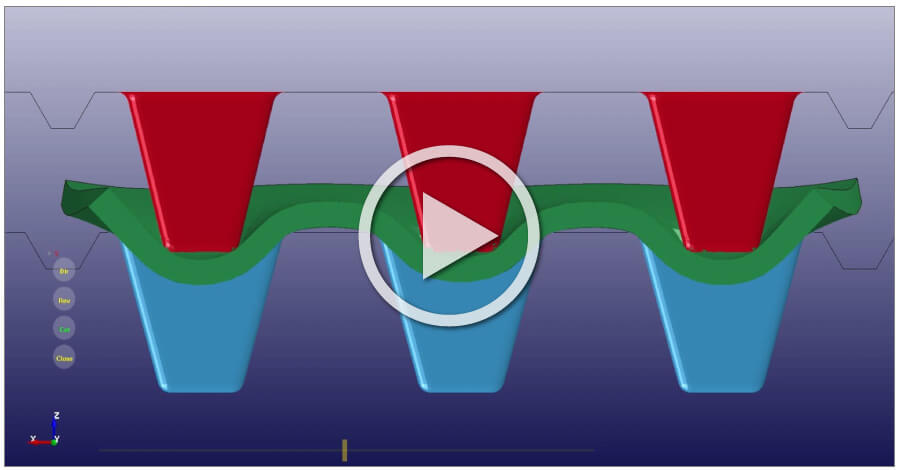 |
|
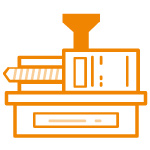
Bridges the Gap between Simulation and Shop Floor
|
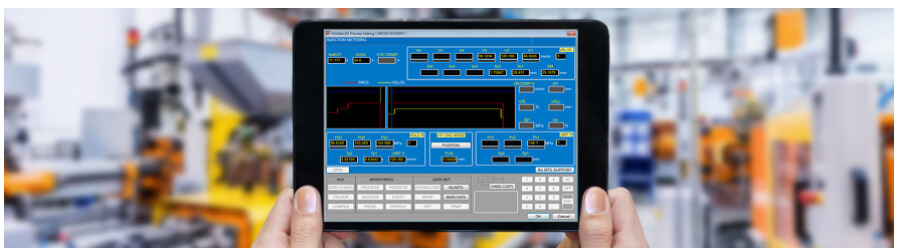 |
Synchronize Simulation Process Parameters with Real-world Molding Machines
Moldex3D R15.0 features an expanded machine interface database with over 15 mainstream injection molding machine manufacturers, including Arburg, ENGEL, Sumitomo, TOSHIBA, Mitsubishi, NISSEI, etc., to shorten the gap between predicted and real-life process parameters, while streamlining the communications between the engineering side and the manufacturing production side. Learn more>>
|
|
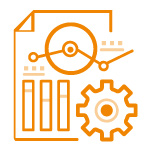
Effectively Manage the Big Data for Your Simulations
|
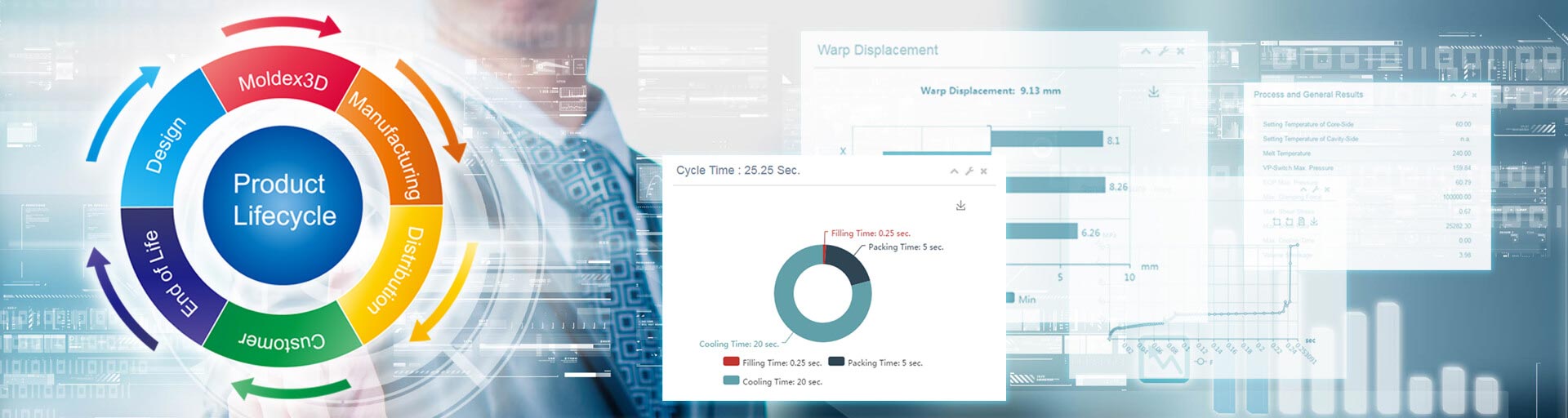 |
intelligent Solution Lifecycle Management
Struggling to manage increasingly vast volumes of simulation data? Now with Moldex3D intelligent Solution Lifecycle Management (iSLM) solution, an intelligent, single point entry for all simulation data, organizations can effectively capture, share and reuse simulation data across teams at different geographic locations, speeding up the development process while significantly reducing management time. Want to find out how to turn your data into a valuable asset? Learn more>>
|
|