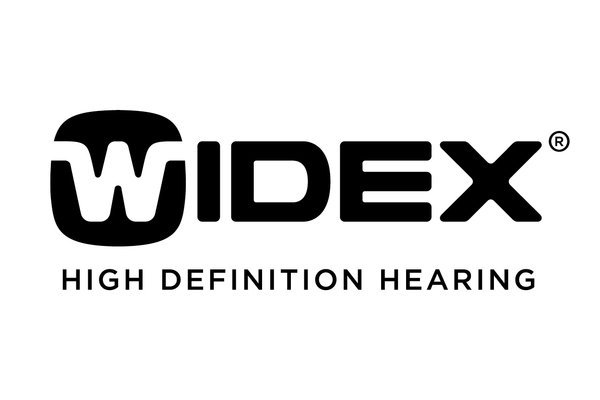
- Customer: WIDEX
- Industry: Medical
- Solution: Moldex3D eDesign Package
- Country: Denmark
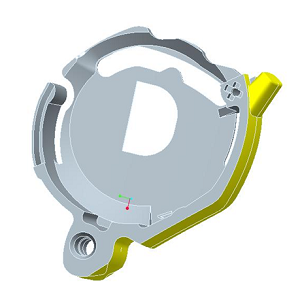
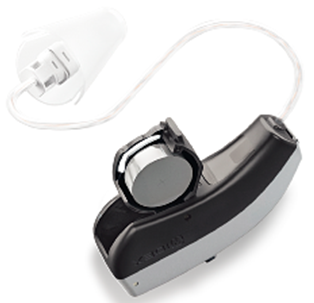
Fig. 1 CAD model of the battery drawer
Project Summary
Hearing aid products are usually very small and delicate. In this example, Widex used Moldex3D eDesign to evaluate various gate locations and part thickness designs on different parts. Moldex3D assisted in investigating the flow behavior during the filling phase and reducing sink marks and warpage severity. Widex could optimize their designs before running mold test by checking the full analysis results. The revised gate location improved the distribution of volumetric shrinkage, making it more uniform; the final warpage tendency can also be accurately predicted.
Challenges
- Complex geometry and moulds
- Maintaining fine tolerances
- Keeping good surface finish
- Easy flowing materials
- Small and discrete components
- Multiple components (polymers and metals) increase molding difficulty
Solutions
Moldex3D eDesign provides an easy and quick meshing technique, and therefore multiple designs and verifications can be achieved in the shortest timeframe possible. The true 3D simulation results, such as weld line, volumetric shrinkage or warpage, help Widex to accurately and efficiently predict potential problems.
Benefits
Widex used Moldex3D eDesign to perform gate location optimization and achieved the following benefits:
- Decrease development time and costs
- Fewer mold-trial times and faster time to market
- Improve product quality: Minimizing warpage and removing sink marks and stresses
- Enlarge process window or use materials that is difficult to process
- Cycle time and material savings
This case involves multiple components designs related to one hearing aid product: The battery drawer, battery connector and the topshell.
The battery drawer is composed of several thin curved designs and the yellow surface will be exposed outside in the final assembly as shown in Fig. 1. Since the weld line location and sink marks often occur on these parts, Widex has to adopt Moldex3D eDesign to create the gate and runner for the part and perform 3D calculations to predict volumetric shrinkage problems.
Fig. 2 Three gate location designs and the related weld line regions predicted by Moldex3D
Fig. 2 shows three different gate locations. Gate Location 1 is the original gate design. Gate Location 2 is the second option, and Gate Location 3 is the combination of the two previous choices. The simulation results revealed that Gate Location 2 will end up in a weld line directly on the critical area which is not acceptable because of reduced mechanical properties.
The original Gate on Location 1 showed that a flow leader was needed, but the weld line location was acceptable. The volumetric shrinkage was very high and sink mark problems became obvious (Fig. 3). By adding a second gate, the location of the weld line was kept but the maximum volumetric shrinkage could be reduced to an acceptable value (Fig. 4).
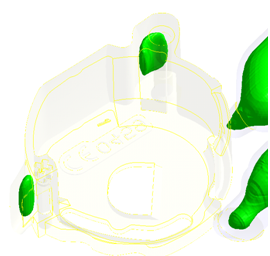
Fig. 3 Gate Location 1 results Fig. 4 Gate Location 3 results
The problem in the battery connector was that the metal insert was not centered (see Fig 6). Flash was observed near the gate as seen in figure 5 meaning that the metal insert will be moved if the flow is not balanced during filling. After performing Moldex3D simulations, the analysis result revealed that the filling pressure was high and that the material entering the cavity flows on the lower side of the metal and thereby pushing the metal upwards (see Fig. 6).
Fig. 5 Flash near the gate area
Fig. 6 High filling pressure near gate area predicted by Moldex3D
As to the topshell, the main issue was how to control the shrinkage which resulted in sink marks and warpage problems. By using Moldex3D, Widex has tested several design modifications (Fig. 7 ) and successfully improved the sink mark problems (Fig. 8 ) and accurately predicted the warpage tendency.