Andy Tsai, Engineer at Material Science Research Center of Moldex3D
In practice, to fully replicate the complete injection molding results, we recommend utilizing Moldex3D to conduct a complete molding analysis to capture all details. However, before investing time on molding and analysis, scientists in the past calculated theoretical values for specific conditions and transformed them into standard calculation formulas. For example, calculating the shear rate for non-Newtonian fluids under specific gate sizes and surface roughness at different flow rates, or calculating the cooling time and temperature distribution of the plate with a specified thickness. MHC integrates these theoretical formulas into an interactive interface for convenient theoretical calculations. We illustrate this with two examples.
Fig 1 Using MHC design estimator that can immediately obtain the theoretical values of specific parameters based on classical theory
Theoretical calculation of plastic part cooling time
In injection molding, cooling time is a crucial factor in product quality and product capacity. In molding parameters, mold opening and taking out the mold will occupy the majority of the cycle time. If cooling time can be accurately evaluated, it will effectively increase the product capacity and reduce the time cost. Plastics are poor conductors of heat, and the thickness of plastics part will affect cooling efficiency. To correctly assess the cooling time of plastic parts with different thickness, scientists conducted a complete analysis of cooling behavior of plate parts in the mold, including the time required for the average temperature in the plastic parts to drop to ejection temperature, and so on. The derived formula for plate cooling time is shown in Figure 2.

Fig 2 The theoretical formula for the average temperature of plate reaching to ejection temperature
The Plastic Part Cooling Time function in the MHC design estimator is a convenient tool for theoretically calculating cooling time of plastic parts. Users can directly import material parameters from material database including material thermal properties and processing conditions. The calculation can also be customized to specific part thickness ranges. The estimator will calculate the time it takes for parts to reach ejection time at different thicknesses and plot the temperature distribution curve showing the temperature at different distances from the center at that time instant.
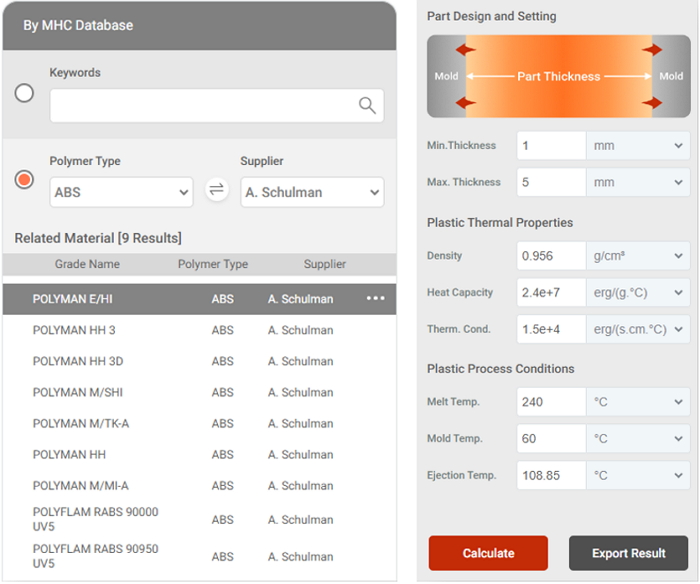
Fig 3 In the Plastic Part Cooling Time feature of the MHC Design Estimator, material data can be directly imported.
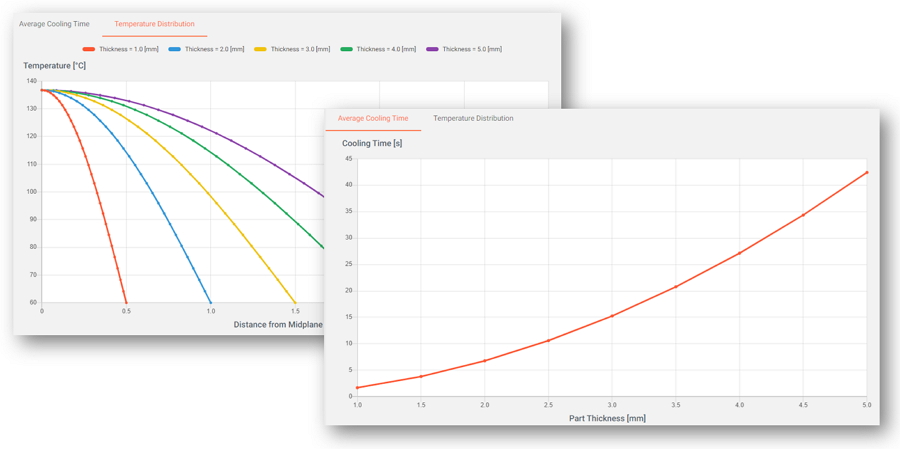
Fig 4 MHC estimator can plot :(1) cooling time estimation for plastic parts of different thicknesses (2) Temperature distribution when the cooling time is reached
The theoretical calculation of gate shear rate
During the filling process of plastics, shear heat will be generated. Excessive shear rate will cause the plastics to be abnormally high temperature or may even cause degradation and/or yellowing. The gate’s cross-sectional is typically the smallest cross-section of the entire part, so the maximum shear rate often occurs there. Therefore, in the optimization of gate size, one of crucial considerations is the maximum shear rate at the gate. When selecting the gate size, if the gate size is too large, it will lead to an increase in cooling time, thereby affecting productivity. Conversely, if gate is too small, it will decrease the packing effect and increases the likelihood of excessive shear rate during flow through the gate. Therefore, evaluating maximum shear rate is crucial when designing gate size. In the “Gate Shear Rate” feature in MHC Design Estimator, users can adjust gate size to calculate the gate type under different flow rates using formulas. The calculation formulas for round gate are shown in Fig 5.
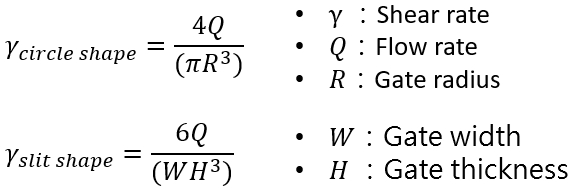
Fig 5 Theoretical formula for the shear rate of round and slit gate
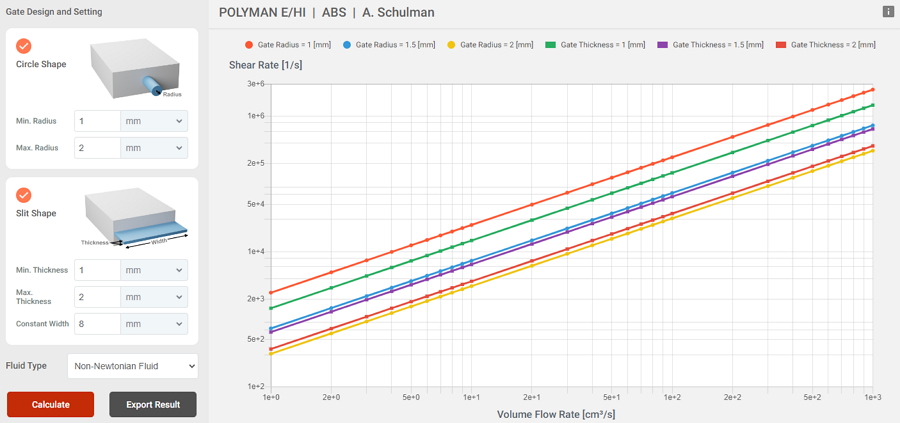
Fig 6 Calculation results of shear rate under different flow rate and gate surface/ sizes
Conclusion
Through the design estimator, users can utilize classical theory to preliminarily evaluate theoretical values of problems such as gate size and cooling time before building a model and conducting a complete molding simulation. MHC visually presents the results calculated by various classical theory formulas and is equipped with simple input surface. It is convenient for users to quickly calculate theoretical values without the need to deeply understand the theoretical basis, so as to facilitate the preliminary evaluation of various molding parameters before CAE simulation.