Cindy Teng, Engineer at Technical Support Division
- Customer: Feng Chia University
- Industry: Educational/Academy
- Solution: Moldex3D Advanced Package; Designer BLM; Flow; Foam Injection Molding
In 1961, the Feng Chia College of Engineering and Business was established. University status was granted in 1980 and renamed Feng Chia University (FCU). The long-term vision for FCU is to establish itself as a prestigious Asia Pacific university characterized by continuous excellence in education and breakthrough research. FCU, furthermore, strives to cultivate the next generation of leaders by maintaining a broad worldview and equipping students with professional knowledge and skills, as well as an appreciation for the arts and humanities. (Source)
Summary
This study demonstrates the lightweighting trend of shoe structure in the current footwear market. Using foam injection molding (FIM) in Moldex3D, FCU used recyclable molding material (SEBS elastomer) to predict the configuration influence of the gate and the change of molding pressure for hot melt with micro bubbles in the filling process. By integrating simulation and experimentation, they verified the impact of gate location and thickness variation on bubble structure and distribution. The final results showed that using foam injection molding can replace foaming agents and reduce product weight by 10%.
Challenges
- Study the impact of the gate design on melt flow and molding quality
- Overcome potential surface defects that may occur in the traditional molding process.
- Predict the growth of bubble structure and reduce the material usage
Solutions
In this case study on insole products, SEBS elastomer was used to reduce the weight of products and overcome the defects of product surface shrinkage. SEBS elastomer could also be recycled and reused to fulfill the demand for a green circular economy. To analyze the impact of different gate designs and uneven product thickness on flow behavior and foaming characteristics, experiments and simulations were conducted using Moldex3D.
Benefits
- Highly consistent results in simulation and experiment, achieved integration between virtuality and reality
- The product weight is reduced by 10%, achieving product lightweighting.
- Realizing a green circular economy, product lightweighting, and understanding the FIM process
Case Study
In the traditional shoes industry, insoles are made from plastic and chemical foaming agents pouring into molds, which has higher manufacturing and material cost. With the development trends of lightweight products and green economy, FIM with addition of gas mixture can simultaneously reduce the material usage and product weight. In this case, the FCU research team used SEBS elastomer to carry out the research, where the target was to find out appropriate gate location, optimizing bubble distribution and verifying the simulation and experimental results. A ready-made mold base with six available gate location is shown in Fig. 1. The FCU research team built the 3D model and Boundary Layer Mesh of the product and analyzed the flow behavior and foaming characteristics using Moldex3D.
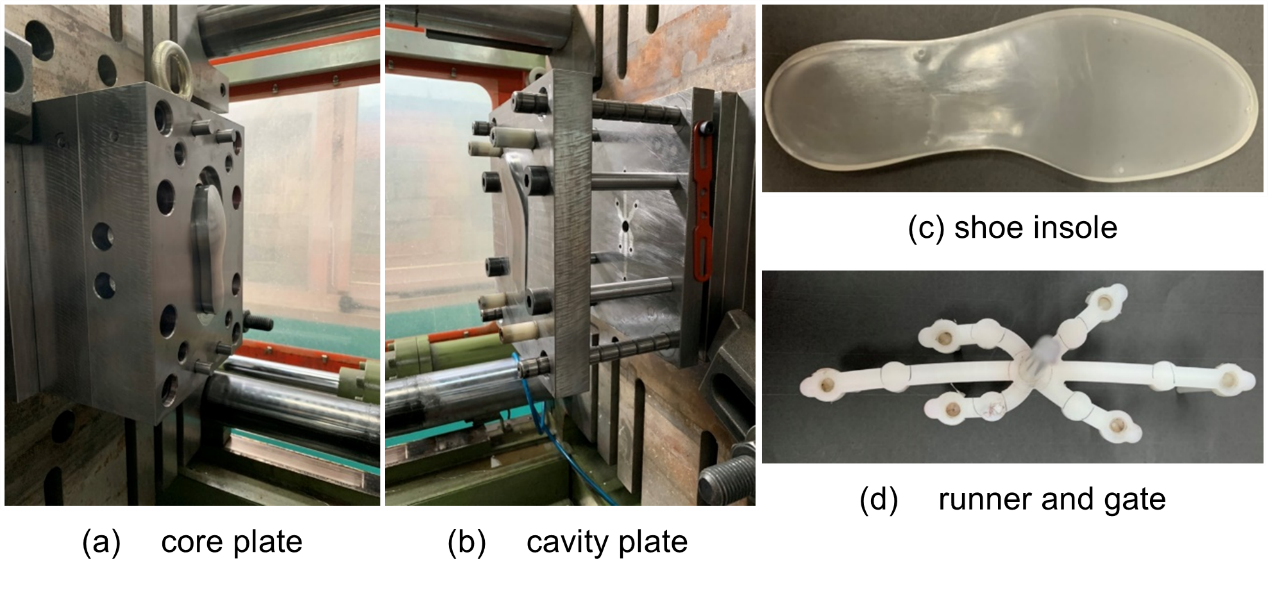
Fig. 1 Mold base and products of shoe insole
Different gate locations led to variations in sprue pressure, cavity pressure and the size of bubbles(Fig. 2 and Fig. 3). When the plastic was injected from thick-walled area, sprue pressure and cavity pressure increased at the end of filling stage since the thickness of product decreases along the flow direction. High cavity pressure limited the growth of bubbles. By contrast, gating at the thin-walled area had lower pressure at the end filling stage, leading to better foaming results.
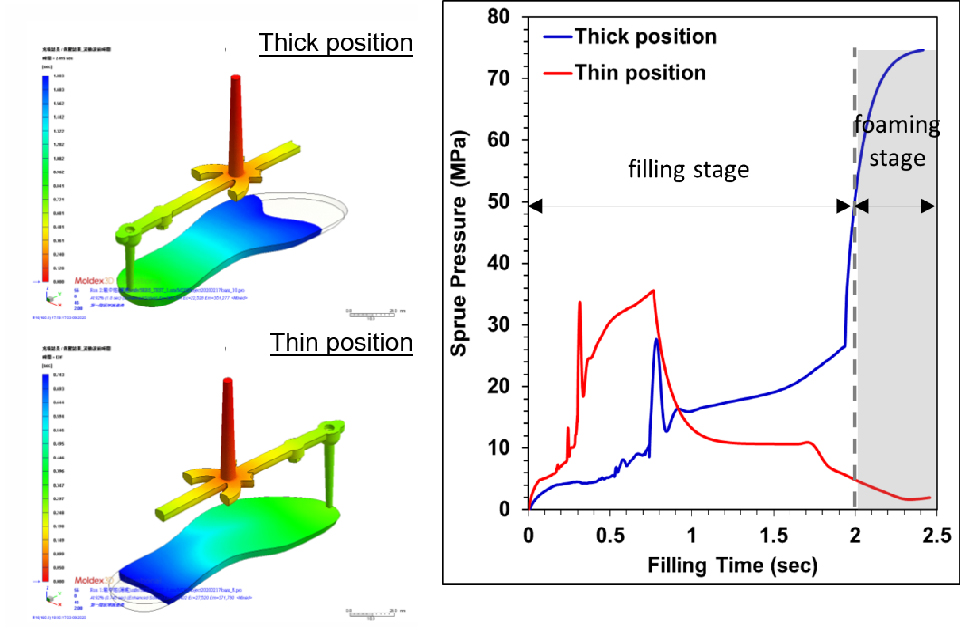
Fig. 2 Sprue pressure of different gate locations
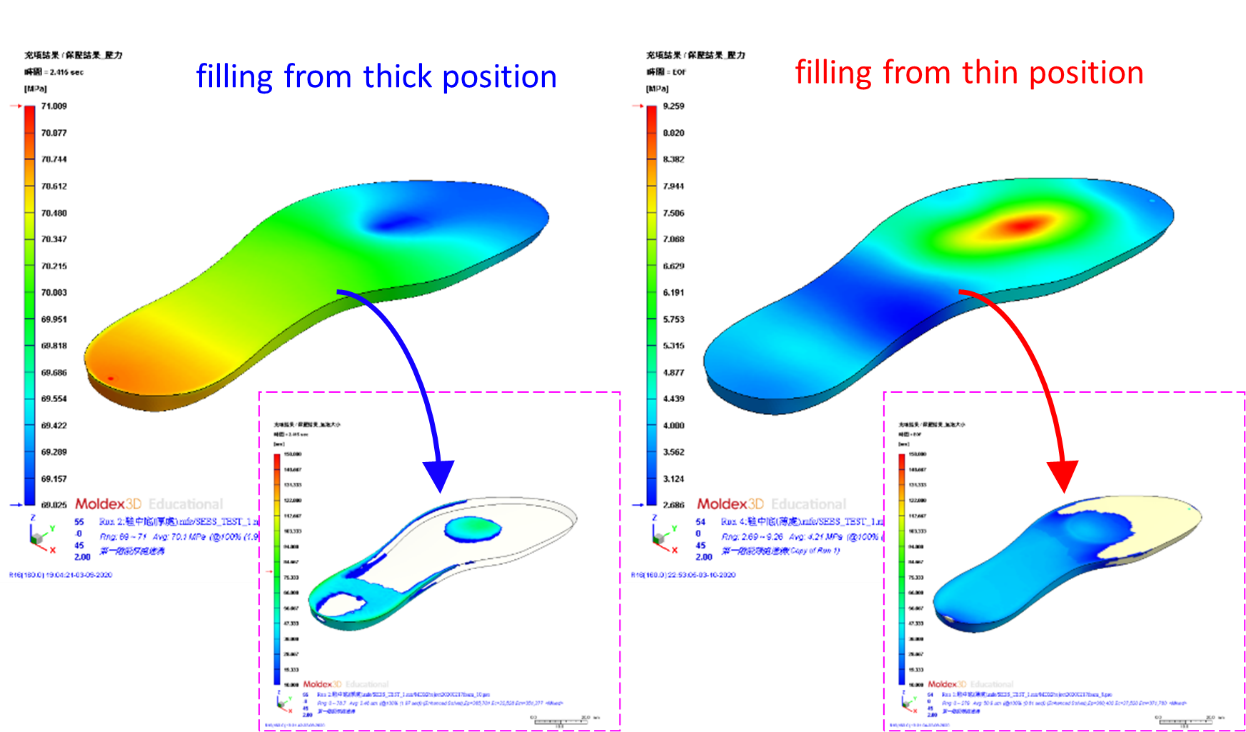
Fig. 3 Cavity pressure and the corresponding cell size (a) filling from thick position (b) filling from thin position
The filling pattern from Moldex3D was confirmed by practical FIM experiments (Fig. 4). The melt front progression from simulation and FIM experiments are highly consistent. The uneven thickness also influenced cell size and cell density as gate locations varied from right to left. The difference of product thickness and filling pattern changed the cavity pressure distribution, which limited the growth of bubbles. Results suggested that filling from both sides would have a better foaming effect comparing to filling in the middle of the shoe insole (Fig. 5).
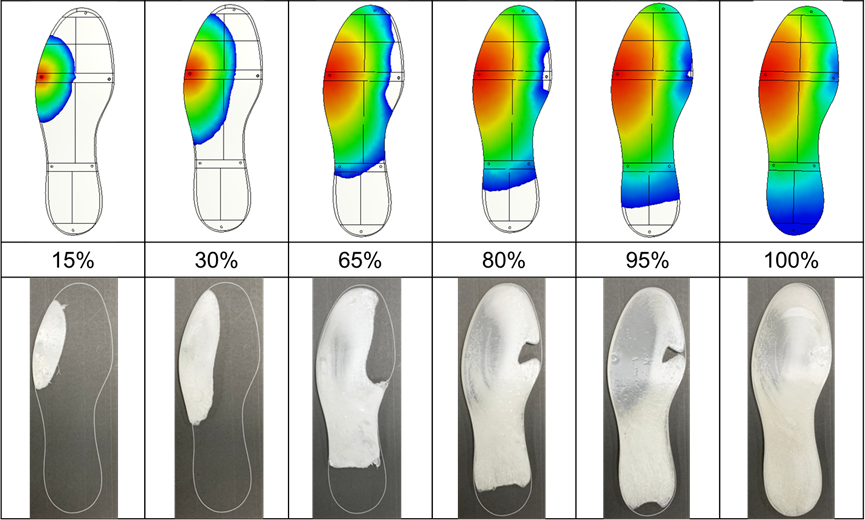
Fig. 4 Melt front from Moldex3D (above) and short shot test (below)
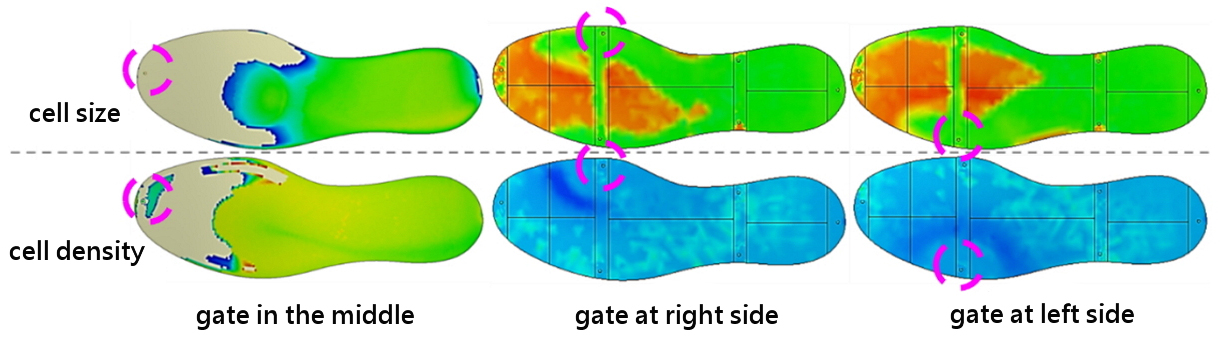
Fig. 5 Size and density of bubbles affected by gate location
The microstructure of bubble distribution can also be researched by practical experiments (Fig. 6). Through the comparison of simulation and experimental results, the foaming process’s effect on cavity pressure and flowing pattern can be better understood. It can be observed that bubbles nucleate better in core layer than in surface layer. In addition, insoles made by FIM can weigh 10% less than conventional injection molding, showing the purpose of product lightweighting.
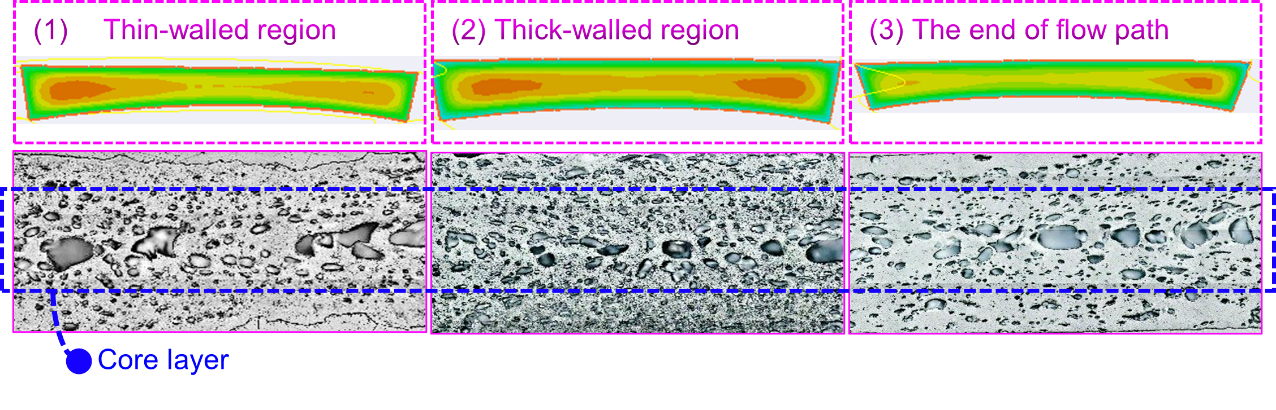
Fig. 6 The microstructure of bubble distribution
Results
In this study, gate location and uneven thickness of products affected the sprue pressure, cavity pressure and flow pattern, which led to different cell size and cell density distributions. With the highly consistent results from Moldex3D simulations and FIM experiments, the FCU research team optimized the gate location to better understand foaming characteristics. By utilizing SEBS/FIM manufacturing, the shoe insoles industry can reach the goal of a green circular economy and lightweighted products.