- Customer: Fortify
- Country: USA
- Industry: Manufacturing
- Solution: Moldex3D Professional
Fortify is transforming the 3D printing industry with its patented DCM (Digital Composite Manufacturing) platform. DCM delivers new levels of additively manufactured part performance by introducing functional additives to photopolymers. By combining a deep understanding of material science with high performance mixing, magnetics, and polymer physics, Fortify is able to produce custom microstructures in high-resolution 3D printed parts. (Source)
Summary
Molding simulation is often used to get starting parameters for a production process as well as evaluate problems that may arise for certain areas of a part given a gate location/design. However, for prototype run quantities where defect free parts are more important than a perfectly centered process, these starting parameters may be all you need.
Challenges
Molding process development alone can take 10-20 shots for basic materials, and the limited lifetime of a 3D printed mold means that using fewer shots to get a defect-free part is crucial for maximizing the yield of functional parts.
Solutions
Using the properties of Digital Tooling (DT) and molding resin, Moldex3D can simulate the defect free process for a Nylon 6/6 demo part.
Benefits
- Reduce process development time at molding machine.
- Maximize output of functional parts off 3D printed mold.
- Save Process Engineer’s valuable time.
Case Study
Given the limited life of soft tools, how to maximize the number of good shots from a soft tool. How to speed up the product development process even more than we already do.
3D printed soft tooling has many benefits including reduced lead times, design flexibility and cost savings, however it lacks the extended lifespan when compared to metal counterparts. It’s true that hundreds and possibly thousands of parts could be produced off a soft tool, but it is much more common to have 50-200 parts produced in its lifetime. The challenge for using a soft tool for production of this number of shots is that process development for injection molding can itself take 10-20 shots for prototype parts, so how can you maximize the number of functional parts off of a tool? Fortify provides a shot count calculator to help customers determine the expected life of their tool, however this accounts for the number of shots, not the number of parts. If developing a process for a tool that is estimated at 50 shots takes 10-20 shots to get a defect free part, then you are nearly 50% through the tool’s life before you have representative parts. Not only does this affect the number of usable parts, but it also takes the time of a process engineer in order to develop the process.
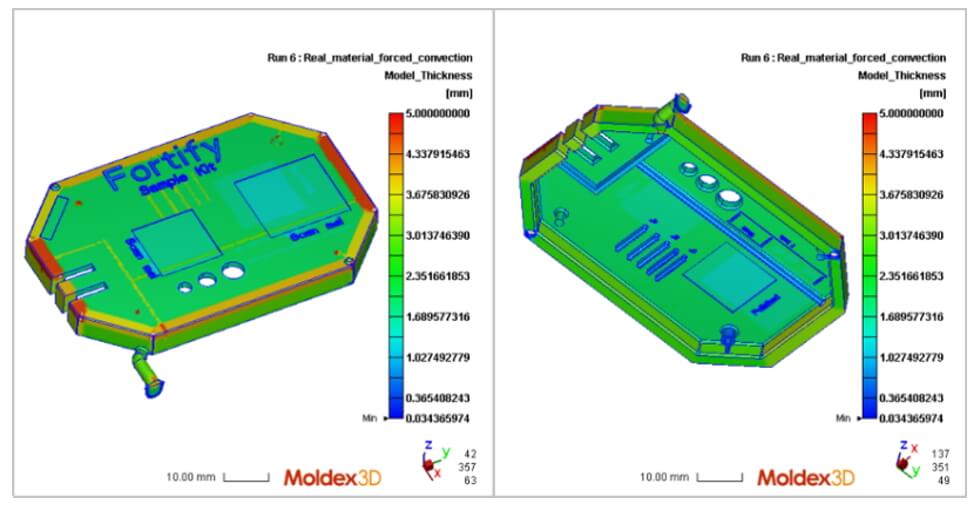
Fig 1. Part geometry wall thickness distribution utilizing Moldex3D
Using the properties of Digital Tooling (DT) and molding resin, Moldex3D was able to simulate the defect free process for a Nylon 6/6 demo part.
This allowed the process development time to be reduced from 10-20 shots to 1 shot. 3D printed tooling has a limited lifetime, using less shots to get your full, defect free prototype means you can get a greater quantity of prototype parts.
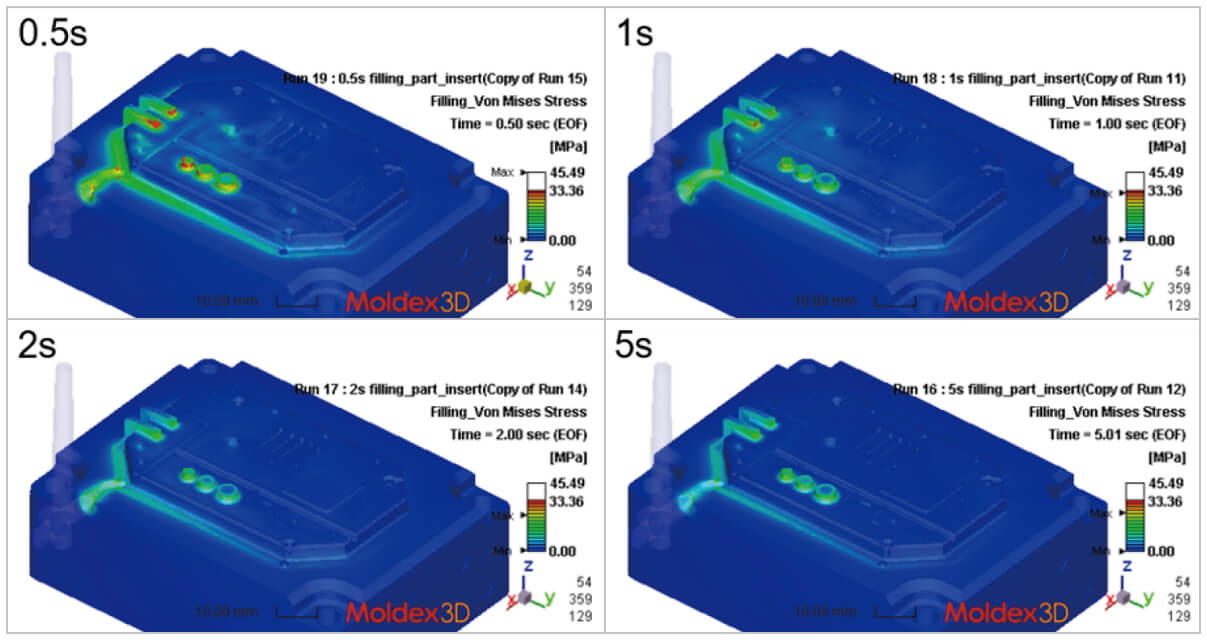
Fig 2. Comparison of the Von Mises Stress on the Fortify DT mold cavity insert
Moldex3D is a high-quality simulation software that can accurately simulate the injection molding process for a given part and provide the user with process parameters for a given part, material, gate location and mold material. While molding simulation is often used to help determine mold design and locate possible defects, vent locations, gate locations and some starting process parameters, it is not often used early in the prototyping process. Fortify decided to leverage this simulation software to maximize the lifetime of soft tooling.
Moldex3D is able to input molding material, mold material and the press information and export process parameters that would result in a complete, full part. By utilizing simulation software, the molding team at Fortify was directly able to hand a process sheet to the operator and produce defect free parts on the first shot, without the need for a process engineer and without wasting half of the tools’ expected life.
Results
The results of the simulation gave the Fortify molding team extensive processing parameters including injection pressure, cooling time, fill time, pack pressure and the packing time. This information was compiled into a process sheet and handed off to a process technician at Fortify HQ. This simulation saved nearly 25 shots on the lifetime of the mold and roughly 2 hours of process development time, freeing up engineers to work on other projects and allowing the molding technician to immediately make good parts.