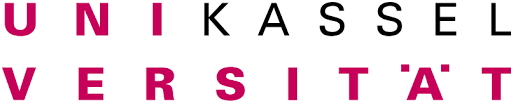
- Customer: University of Kassel
- Country: Germany
- Industry: Educational/Academy
- Solution: Moldex3D Advanced Package; Foam Injection Molding Module
- View PDF Version
Executive Summary
In this project, the University of Kassel investigated the local core-back technique to achieve higher expansion ratios for creating less dense parts and to achieve a homogeneous foam structure in foam injection molding. Different from the standard core-back, the cell growth and density reduction were mainly restricted to the locally expanded areas with the local core-back technique. Boundary conditions and process parameter settings greatly influenced the formation of the foam structure in both expanded and non-expanded areas. With Moldex3D Foam Injection Molding Analysis, University of Kassel was able to obtain a better understanding of the structure formation during the process and further optimized the process conditions.
Challenges
- The complex interplay between materials, process settings and geometrical boundary conditions will affect the core-back result.
- Unable to observe the actual foaming process
Solutions
Using Moldex3D to simulate the core-back operations in the foam injection molding and predict the foaming behaviors inside the cavity to optimize process parameters and obtain the desired core-back result.
Benefits
- Provided a better understanding of the local core-back technology for foam injection molding
- Enabled the visualization of the foaming process
- Successfully validated the qualitative experimental result via simulation
Case Study
In this project, the University of Kassel used Moldex3D to provide an in-depth insight of the structure formation during the foam injection molding process. Moldex3D supports boundary condition settings for the local core-back process and is able to simulate the cell size, cell density, and part density at different times during the filling and packing process. In addition, Moldex3D’s sensor nodes are also very helpful in describing the relationship between the pressure and the cell size in expanded and non-expanded areas.
The cells were first created during the filling stage and re-dissolved due to the packing pressure before the second cell formation took place. Fig. 1 is the cell size prediction in this case. It is found that the cell size will expand to a larger size when the core-back is done. The Fig. 2 shows that the larger the cell, the lower the cell density would be.
Fig. 1 Cell size during filling and packing phase (before volume expansion) and at the end of filling (after volume expansion)
Fig. 2 Cell density during filling and packing phase (before volume expansion) and at the end of filling (after volume expansion)
Fig. 3 shows the changes of the product density. The cell formation in the expanded area leads to a huge density reduction in these areas while the density of the non-expanded area is similar to the non-foamed material density.
Fig. 3 Comparison of the density during filling and packing phase (before volume expansion) and at the end of filling (after volume expansion)
With Moldex3D, users can easily observe the foaming behaviors inside the cavity. The sensor node function also provides a detailed understanding of the foaming behavior inside the cavity (Fig. 4)
Fig. 4 XY curve – pressure and cell size at sensor nodes in expanded area A (SN5) and non-expanded area B (SN7)
With the help of simulation, the effects of foam injection molding with core-back technology were investigated. Thus, parameter variations for SCF content (blowing agent content), expansion ratio (core-back distance), delay time, core-back speed, holding pressure and holding time were included.
Fig. 5 shows the simulation results of different process settings. The influence of SCF content (blowing agent content) is shown and compared with real structures. Both simulation and experiment shows that when the SCF content is higher, the cell size will become smaller. The simulation results showed good agreement with the experimental data.
Fig. 5 Cell Size in dependency of SCF content
Results
Through Moldex3D, the University of Kassel obtained a better understanding of the local core-back technology for the foam injection molding process, visualize the foaming process, and successfully verify qualitative experimental results.