During injection molding process, the mold base and its components would have to withstand several external loading issues; the temperature and the pressure, for instance, are two major influential effects that impact the mold condition. Over the length of time the mold is used in the injection molding process, these effects will eventually contribute to mold deformation problems. This is a major concern as the deformation of the mold changes the cavity dimensions and decreases the precision of the final molded parts. As a result, the analysis of mold deformation has become a valuable reference for mold designs, especially for optimizing the manufacturing of high-precision products.
In the latest R13.0 release, Moldex3D introduces a new module to simulate mold deformation and its effect. After entering the custom processing conditions, users may set user-defined boundary conditions in Computation Parameter, and run an analysis to obtain specific results on mold displacement field and stress concentration field. Through the mold deformation analysis, users are able to detect potential problematic areas in the mold and make necessary changes to address these issues before the mold is machined. Thus, users can take advantage of utilizing this useful data to optimize the mold design by adjusting the processing parameters, the geometry model, and the mold material. This way, the mold structural strength can be further enhanced in order to extend the durability of the mold as well as to ensure the precision of the final molded products.
The example below will demonstrate how to run a Mold Deformation analysis in Moldex3D R13.0:
1. After the completion of filling and cooling analyses, users can proceed to run a Mold Deformation analysis. Mold deformation behavior induced by the pressure loading in the filling stage and mold thermal loading in the cooling stage can be analyzed and visualized for the mold defect detection.
Pressure distribution at the end of filling
Temperature distribution at the end of cooling
2. Set user-defined boundary conditions in Computation Parameter under Mold Deformation tab
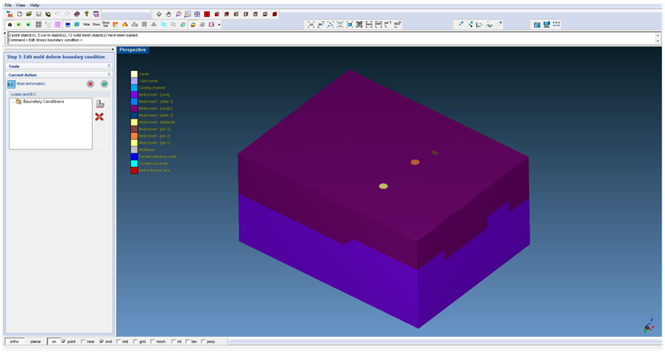
In Designer interface, users can set displacement constraints of the mold
3. Run Mold Deformation analysis
4. Obtain Mold Deformation analysis results:
- Mold displacement field
- Mold stress concentration field
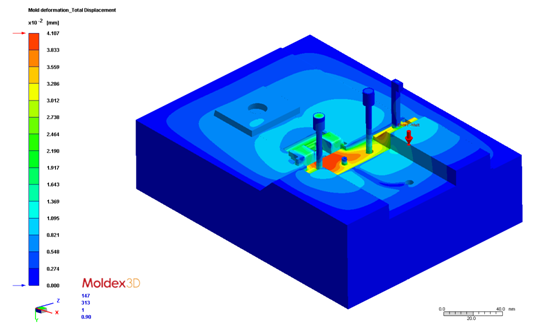
Total mold displacement field-1
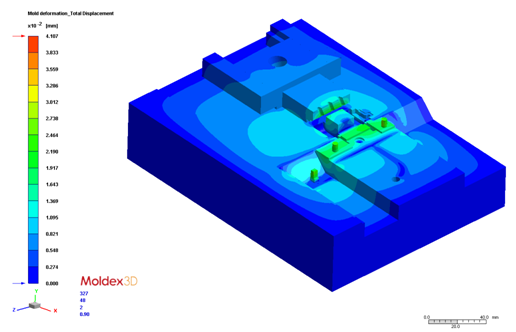
Total mold displacement field-2
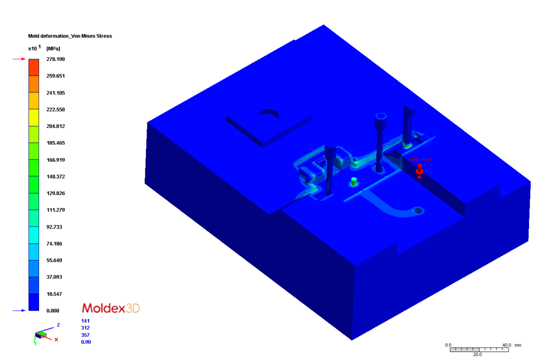
Von Mises stress field-1
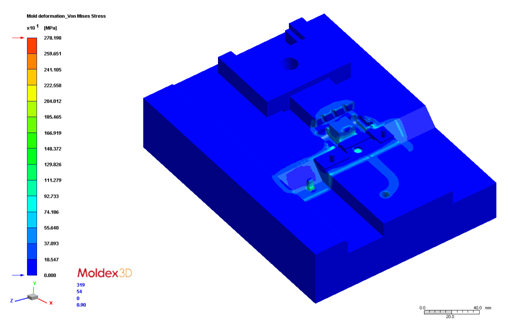
Von Mises stress field-2
In the above case, we know that the total mold displacement field ranges from 0 mm to 0.004 mm and the stress distribution field ranges from 0 to 2781 MPa, the maximum.
The area that has the largest displacement value, shown in the mold displacement analysis is an indicator of the most deformed area likely to occur on the final molded part. And, the stress concentrated areas, shown in the stress distribution analysis are the areas where they are most likely to encounter fatigue and suffer damage after the mold is used for some time. Consequently, after obtaining the mold deformation data, users can make a corresponding geometry adjustment and select the appropriate mold material to optimize the mold design and strengthen the mold structure. As a result, the mold deformation analysis proves to be a valuable reference for mold designs and optimizations. That is, having a proper and functional mold not only ensures a precise adherence to final product requirements but also prolongs the overall mold life.