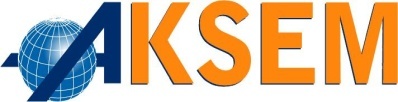
- Customer: AKSEM Plastik Metal Kalip San. ve Tic. Ltd.Sti.
- Industry: Automotive
- Solution: Moldex3D eDesign
- Country: Turkey
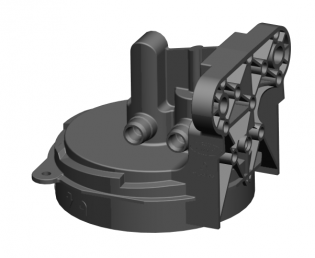
This case features an automotive part–oil filter head. Due to the safety requirements of the part,
the part has very little tolerance for warpage and dimensional deviation.
Executive Summary
This case features an automotive part–oil filter head and due to the safety requirements on the part, it has very little tolerance for warpage and dimensional deviation. Firstly, parts made by the Plastic Injection Molding (PIM) process have been widely used in the automotive sector in order to reduce physical weight and manufacturing costs. The shrinkage ratio is an important variable to consider for mold production. However, keeping the shrinkage ratio in an acceptable range can be quite difficult for some parts if they are sensitive and have little tolerance for dimensional deviation, such as cylindrical parts. Thus, having mold-filling simulation analyses to help identify problematic shrinkage areas, and keeping the shrinkage ratio in a reasonable range is an essential task. Secondly, utilizing Moldex3D analyses provided valuable information for actual mold design and construction. It proved to be a more economic approach than using a conventional trial-and-error method in terms of time and cost savings. Moreover, with the aid of Moldex3D DOE (Design of Experiment) module, not only could the crucial manufacturing parameter that has the greatest impact on the processing stage be pinpointed, but also the most optimized set of manufacturing parameters were be easily computed by the software for product processing consideration.
Challenges
The oval-shaped deformation in the cylindrical region of the part, planarity (surface flatness) and cold weld lines are three major critical factors to consider in this case. As uneven shrinkage will result in a potential oil leaking problem, it is necessary to resolve the oval-shaped deformation and other product defects in advance to avoid an oil leaking problem in the future. However, visualizing molding behaviors inside the mold cavity to effectively address potential molding issues is definitely a challenge. Therefore, the major goal of this case is to find an appropriate solution to ensure product quality and minimize the likelihood of multiple and unnecessary mold trials.
Solutions
To achieve its goal of attaining better product quality, Moldex3D DOE (Design of Experiment) Technology was employed to identify the most optimized manufacturing parameters prior to production. Through the actual mold trial, Moldex3D simulation analyses were proven to be closely correlated with the results from the actual mold trial. That is, based on the analysis of Moldex3D Solution, ASKEM successfully managed to identify the allowable displacement values and was able to control the product surface flatness which ultimately led to significant savings in time and overall production cost.
The most optimized parameter values were identified by Moldex3D DOE.
Case Study
First of all, the most important task of this case was to find out the real dimensional values of the finished part, and this data could be attained by analyzing the simulation results of Moldex3D and the DOE module. Knowing the dimensional results could help address potential shrinkage issues and make corresponding adjustments in the design of the mold dimensions to correct the shrinkage ratio and deviation of the part. In other words, the oval-shaped deformation in the cylindrical region of the part could be corrected and greatly improved by machining the mold steel accordingly based on the Moldex3D analyses.
Warpage_Total Displacement: 0.102mm~1.53mm
Steel and part data had been modified according to warpage data from Moldex3D during mold design stage.
Secondly, another major task was to determine the best locations for air venting in the mold design in order to reduce warpage and cold weld line problems on the part. Based on the Moldex3D analysis, possible air trap locations were visualized in advance; thus, modifications of the air venting layout design were made to better tackle the potential air trap problem and reduce its occurrence on the part. The better air venting layout design was validated by the significant improvement on the planarity (surface flatness) of the finished part. And, the cold weld line problem was under control since those locations will not pose a risky effect on oil leakage in the future.
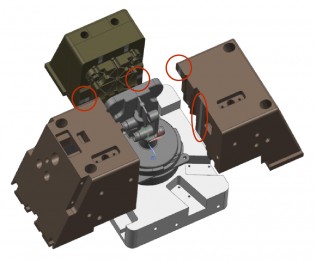
The air venting layout (right) in the mold design was machined based on the air trap prediction (left) by Moldex3D.
Moreover, in this case, the plastic-made oil filter head part will be assembled with another bowl part, so the precision of the part is crucial. Therefore, checking each point and making sure all potential problems were considered before starting manufacturing the mold is very important to avoid unnecessary production costs and to shorten the manufacturing lead time.
In summary, utilizing Moldex3D analyses, ASKEM could not only predict problematic areas beforehand but also determine crucial processing parameters to further help tackle potential issues and correct them accordingly prior to the mold making. Furthermore, with the help of Moldex3D DOE module, the most optimal processing parameters could be predicted by the software in advance and that is valuable information for engineers to provide quicker turnaround time and deliver high quality end-products.
Results
Moldex3D simulation analyses provided useful insights into good mold design. Comparing the Moldex3D simulation results with those from the actual mold trial, it was proven that Moldex3D offers solid and reliable simulation data for its users. More importantly, the goal of improving product quality and productivity was successfully accomplished, and overall production cost was reduced thanks to the accurate simulation analyses. In conclusion regarding in this case, Moldex3D successfully demonstrated its high caliber plastic injection molding simulation. Moldex3D served as a viable platform between the product design stage and mold manufacturing stage and was a reliable source for design optimization and validation.