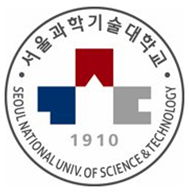
- Customer: Dept. Mechanical System Design Engineering,
Seoul National University Science Technology - Industry: Academy
- Solution: Moldex3D Advanced Package
- Country: Korea
Executive Summary
Since 2005, Seoul Tech started to utilize Moldex3D simulation results to conduct experimental verifications with concentration on mechanical systems design and numerous papers were published with significant impacts on both academic and industrial development. The following research was one of the papers that Professor Keun Park from Seoul Tech co-worked with world-class company, LG Electronics Mold Technology Center, to co-develop study investigating the cooling performance by using pulsed mold temperature control. Both Seoul Tech and LG Electronics leveraged Moldex3D simulation results to optimize product design and manufacturability.
Challenges
Today many manufacturers struggle to find new approaches for making thinner, lighter and better electronic products with enough structural strength. To ensure product quality during injection molding process, the mold temperature will be raised to avoid potential problems such as weld line or residual stress. Though the surface quality of the part will be improved, cooling time and cycle time will also be relatively increased with higher mold temperature. Therefore, how to shorten cooling time while maintaining mold temperature is a crucial issue for mold designers who consider for efficient and cost-effective manufacturing.
Solutions
The dynamic control of mold temperature is adopted to deal with such issue. In this study, a pulsed mold temperature control was proposed to improve the part quality as well as the productivity by alternatively circulating hot water and cold water before and after the molding stage. In the cooling stage, the temperature can be lowered down quickly without affecting the cycle time. The simulation results were compared with conventional mold cooling system in terms of the heating and cooling efficiencies.
Case Study
In this study, Seoul Tech investigated the transient temperature of the mold based on the accurate simulation capabilities of Moldex3D. Pulsed mold temperature control techniques were adopted and the mold surface temperature results were compared with conventional cooling system. As shown in Fig 3, the total cycle time is 21 seconds when using conventional cooling system and 60°C water is injected continuously during each cycle. On the other hand, with pulsed cooling system, 80°C water is injected in the beginning, and the coolant is changed to 40°C water and injected continuously for 11.5 second after 0.5 second of filling stage,. During the cooling stage, 80°C water is re-injected for 9 second.
Fig. 3 Comparison of Cooling time with conventional cooling and pulsed cooling methods
With Moldex3D’s three dimensional transient heat transfer simulation capability, temperature distribution at any specific time can be precisely predicted. Fig. 4 and Fig. 5 show the variations of mold temperature distribution with conventional cooling and pulsed cooling system, respectively. With pulsed cooling method, as hot water and cold water can be circulated alternatively, the mold temperature could be raised without increasing the cycle time.
Fig. 4 Variations of the mold temperature distribution with conventional cooling method (℃)
Fig. 5 Variations of the mold temperature distribution with pulsed cooling method (℃)
As shown in figure 6(a), with pulsed cooling system, the molding cycle time could be shortened around 20 seconds which shows the high efficiency achieved by adopting pulsed cooling method. Compared with the final temperature of the cooling phase, the highest temperature of the pulsed cooling control is 3.2℃ higher than that of the conventional cooling. And the lowest temperature of the pulsed cooling control is 7.3℃ lower than that of the conventional cooling as shown in figure 6(b).
Fig. 6 (a) Total molding cycles Fig. 6 (b) The final molding cycle
Results
With Moldex3D’s three dimensional transient temperature distribution results, users can accurately predict the effects of the variotherm technology and avoid potential problems prior to mold making stage. In this study, heating and cooling efficiencies could be easily visualized and the simulation results provide an effective way for fast experimental validations. By using Moldex3D Advanced Package and solution-add-on modules, Seoul Tech is able to conduct experimental verification for different kinds of special manufacturing process, such as Compression Molding, Gas-Assisted Injection Molding, etc. Now Moldex3D has been implemented by many global leading academies for not only educational research purpose but also for supporting students stay competitive academically, economically, and technologically.
*Note: This paper was presented at 2012 International Conference on Manufacturing, Machine Design and Tribology.