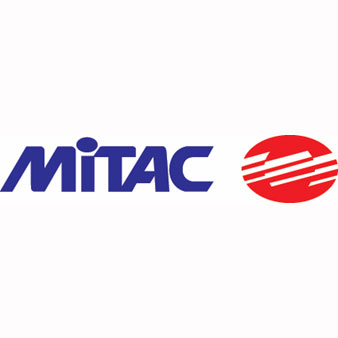
MiTAC Inc., founded in 1974, is the first member in the Group family and the largest IT system integration provider in Taiwan. With extensive backgrounds in all aspects of hardware, software, communication, networking, integrated testing, training, maintenance and consulting services, MiTAC is dedicated to helping industries and the government to achieve targets in productivity and quality with a total solution.
(Source: https://www.mitac.com.tw/en/index.html)
Challenge
The designs of runners, gates and thickness layout are crucial to product quality.
Solution
Leverage on Moldex3D analysis to evaluate the gate location and optimize runner and thickness layout.
Benefits
Enhance product quality and significantly reduce trial-and-error iterations. Optimize cross-department coordination and the integration of various development procedures
MiTAC Precision Technology Corporation (MPT)’s primary business includes tooling and mass production, ranging from design, mock-up, tooling to plastic injection, stamping to coating, as well as printing and post-production assembly services.
Through professional injection molding simulation software Moldex3D, now engineers of MiTAC are able to quickly check the manufacturability of the injected plastic part design. This time-saving, highly accurate and user-friendly function of Moldex3D mold filling simulation enables the R&D team to facilitate efficient discussion and commutation on the confirmation and optimization of the product and mold design. Thus, Moldex3D unquestionably plays an extremely important role in “Quality control of mold design” and “Communication platform of the design.”
As a result, Moldex3D has been well-appreciated by its customers for its remarkable achievement in 3S (Software, Service, Solution). In 2006 and 2007, Moldex3D was awarded by two of the leading technology companies: ASUS Computer Inc. and MiTAC Precision Technology Corp., in their 2006 and 2007 annual event with the prestigious honor of “excellent supplier of the year” and “The best software supplier of the year”.
Evaluate runner and gate design using Moldex3D
The design of runner and gate is one of key factors which significantly have impacts on product quality, especially for gate location selection and runner layout. Therefore, engineers of MiTAC usually adopt Moldex3D analysis to evaluate the design of runner and gate.
1. Observe the simulation of melt front, and users can understand the injection behavior of the melted plastic material from nozzle to cavity. As the melt front analyses show, users can acquire the pressure required for runner and gating and evaluate pressure drop condition to determine adequacy of runner layout and gate type (Fig. 1~3).
2. Observe whether the melted plastic material is evenly filled in the cavity.
3. Observe uniform and even filling in the cavity and prevent short shot or excessive filling.
4. As the warpage analyses shown in Figure 4~6, users can observe whether the pressure evenly transmit to each plastic part, and accurately perform packing to manufacture the product with condense filling and a clear-cut shape
5. In the system of multi-cavities, proper runner and gate location shall achieve balanced filling so that the plastic material may be filled in each cavity at the same to ensure the consistency of the finished product of each cavity.
![]() |
![]() |
![]() |
Fig .1 The melt front simulation of cover component of 3C products |
Fig. 2 The melt front of the frame component of 3C products |
Fig. 3 The melt front simulation of cover component of 3C products |
|
|
|
Design thickness layout
The design of thickness layout is another important factor on product quality. Proper design will prevent problems of flow hesitation and short shot, and further improve the part quality.
1. Observe the simulation of melt front, and users can understand the influence of various thickness conditions in the flow process. Figure 7 shows the flow analysis of multi-gate product.
2. Investigate heat dissipation phenomenon in different thickness zones with the display of temperature and evaluate whether thin-wall may cause the flow hesitation and short shot. Figure 8 shows the analysis result of temperature. If the gates are located at the central area of thin thickness, it might cause the problem of short shot due to the temperature undergoes a rapid drop.
![]() |
![]() |
Fig. 7 The flow simulation of cover part of laptop |
Fig. 8 The temperature distribution of cover part of laptop |
Moldex3D-Mesh: mesh creating made easy
Besides, to meet the specific needs for a wide array of injection simulations, Moldex3D is proud to provide the multi-functional pre-process mesh known as “Moldex3D-Mesh”. The advanced functions of Moldex3D-Mesh allow the users to create/export/fix/edit mesh models effectively, determine the runner layout and cooling system and prepare different meshes required for various types of analysis in advance. As the complicated model shown in Figure 9, Moldex3D-Mesh allows the users to mesh the model efficiently and quickly.
Fig. 9 The big size cover part of 3C products
MiTac’s Appreciation
Moldex3D can be used for enhancing the quality of design and significantly reducing the times of mold testing while optimizing cross-department coordination and the integration of various development procedures. Finally, Moldex3D would like to thank AsusTek Computer Inc. and MiTac Precision Technology Corp. for their support and appreciation.
* This case was published in July, 2007. Moldex3D News No. 17