Millie Lin, Engineer at Technical Support Division
- Customer: Voestalpine Technology Institute (Asia) Co. Ltd
- Industry: Manufacturing
- Solution: Designer BLM、3D Coolant CFD
Voestalpine Technology Institute (Asia) Co. Ltd specializes in the advanced applications of high-performance metal materials and the integration of related technologies. The core technology focuses on innovative development and research service of 3D printing/additive manufacturing technologies and R&D services. Its main applications include high-performance molds for precision plastic injection and aluminum high-pressure die casting, as well as other high-value-added products. The company also engages in the integration and development of new technology such as heat treatment and surface coating.
Summary
This study employs a monitoring system consisting of thermographic camera with a pressure/flow meter to conduct real-time monitoring on surface temperature of inserts produced by additive manufacturing (3D printing) and the flow performance of conformal cooling channels. By comparing the results with Moldex3D simulation results under identical conditions, the simulation results closely aligned with the actual test., effectively reducing the development costs of complex products.
Challenges
- Confirm the benefits of replacing beryllium copper with stainless steel in the design of conformal cooling channels before production.
- Ensure that the simulation results closely match the reality.
- Utilize the monitoring system to validate performance of 3D printed conformal cooling channel molds.
Solutions
Utilize a mold preheat module to reproduce the temperature distribution of the conformal cooling channels.
Benefits
- The simulation results are highly consistent with the actual test results.
- The lifespan of the mold has doubled.
- The manufacturing cost of the mold is half that of the original beryllium copper mold.
Case Study
The design of cooling channels is crucial in plastic molding, significantly affecting mold temperature and warpage. Produced conformal cooling channels through additive manufacturing (3D printing) can improve the disadvantages of traditional molding, such as reducing hot spot temperature and decreasing cycle time. However, the manufacturing cost is higher and more precise simulation analysis is required to enhance its adoption. In this study, a monitoring system will be established to monitor the mold temperature field and flow field. It will utilize actual heat then transfer performance assisting in model creation and parameter settings to enhance the design efficiency of conformal cooling systems.
The original cooling system design, as shown in Fig. 1, utilizes beryllium cooper. Although it offers the advantage of high thermal conductivity, there are concerns about its environmental impact. Additionally, since the part material contains glass fiber, the wear resistance of beryllium copper is insufficient, which can reduce the lifespan of mold and consequently increase the manufacturing costs.
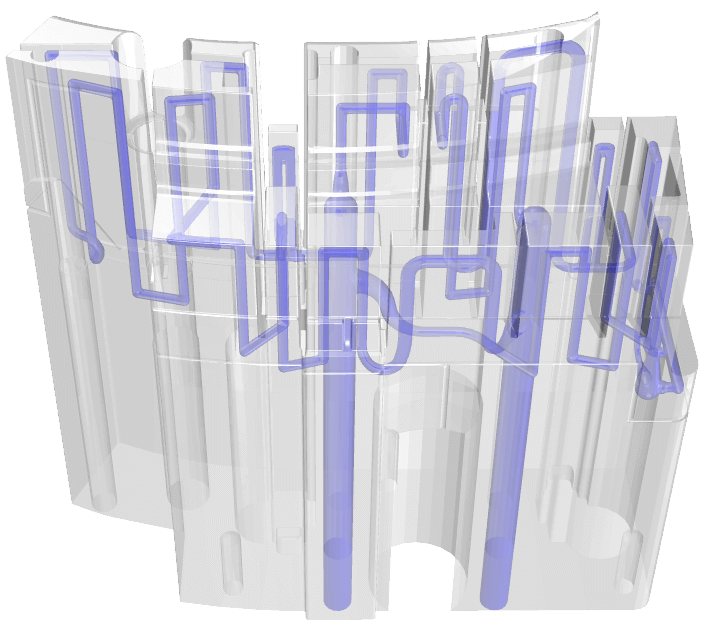
Fig. 1 Original cooling system design
Based on above considerations, another mold will be manufactured using 3D printing to achieve both a longer lifespan and excellent cooling efficiency. The selected mold material is high-hardness stainless steel. Before production, Moldex3D simulation will assist customers in determining whether specific areas of the mold meet expectations. Evaluation criteria include temperature distribution and the flow of conformal cooling systems. The settings are shown in Fig. 2.
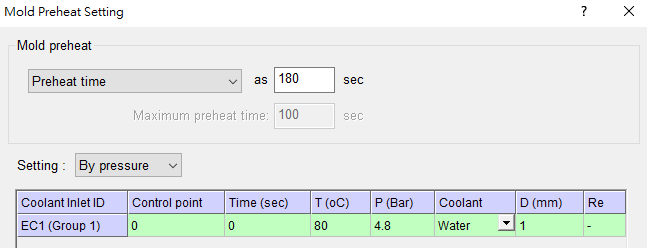
Fig. 2 Cooling system setting
After the analysis is completed, the simulated velocity result of cooling system in the figure below indicates the flow velocity of outlet is about 84.35 cm/s. When converted to flow rate, this equates to 3.97L/min. The measured flow rate is 3.80 L/min, which closely matches the simulated result.
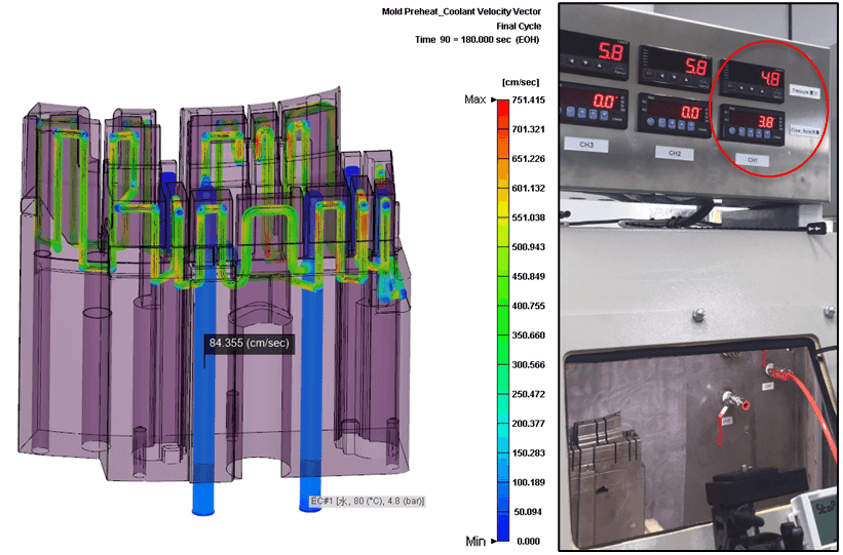
Fig. 3 Simulated outlet velocity vs. actual flow rate
The experiment utilized thermographic cameras to record the temperature distribution during the mold heating process. Comparing the temperature results from figure below, it can be observed that the simulation and experiment results are consistent and exhibit similar trends. Over time the temperature distribution gradually becomes uniform and stable. The temperature data captured by thermographic camera was plotted into a curve and compared with the simulation results, as shown in Fig. 5. The trends are generally consistent, with some discrepancy in the initial values. When comparing the temperature at the last second, the temperature difference between the experiment and simulation is approximately 1.3°C.
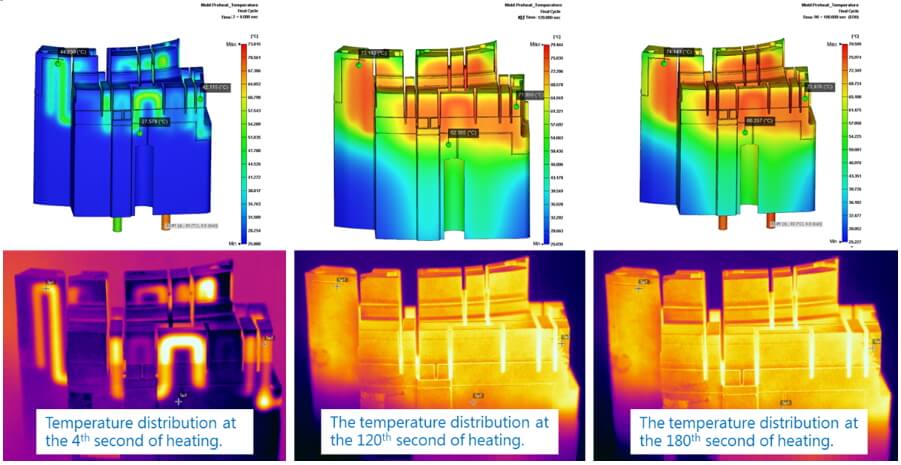
Fig. 4 Comparison of temperature distribution
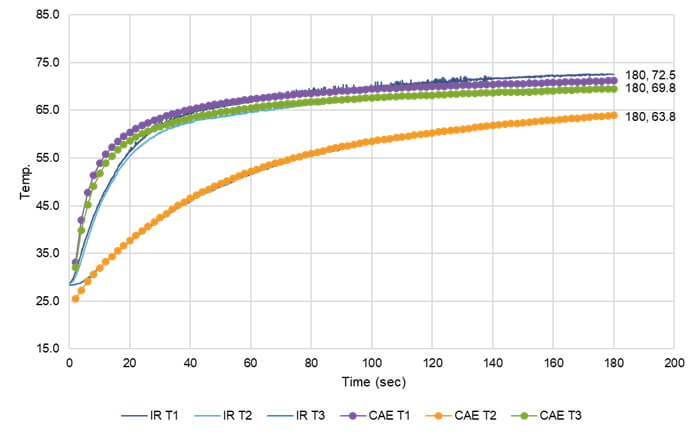
Fig. 5 Comparison of temperature history
Comparing the original design (beryllium copper) to the optimized design (stainless steel), although stainless steel’s thermal conductivity is lower than beryllium copper, the design of conformal cooling system compensates for the disadvantage. Additionally, the high hardness of stainless steel improves the mold’s wear resistance and increases the lifespan. Through customer testing, it has shown that the mold can achieve the same cooling effect within the same cycle time, and the optimized design results in a more uniform mold temperature distribution. Moreover, the uniform temperature distribution reduces product warpage caused by mold temperature differences.
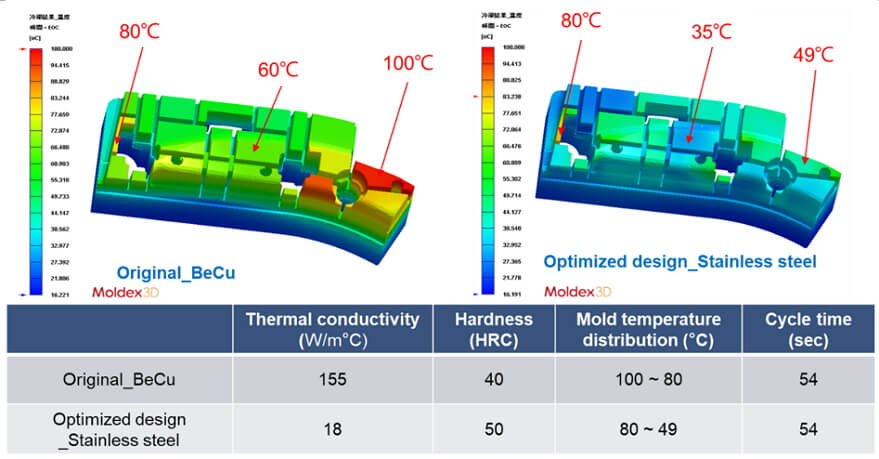
Fig. 6 Original (BeCu) vs. Optimized design (stainless steel)
Results
In the study, Moldex3D was used to predict the temperature and flow field of conformal cooling system, which were validated through on-site testing. The high-cost beryllium copper mold was successfully replaced with a more cost-effective stainless steel mold. This not only reduced the environment impact but also doubled the mold’s lifespan, while achieving a more mold temperature distribution.
By exploiting Moldex3D for mold development and optimization, particularly for complex products with higher development costs, users can significantly reduce development time, minimize development errors and enhance overall efficiency.