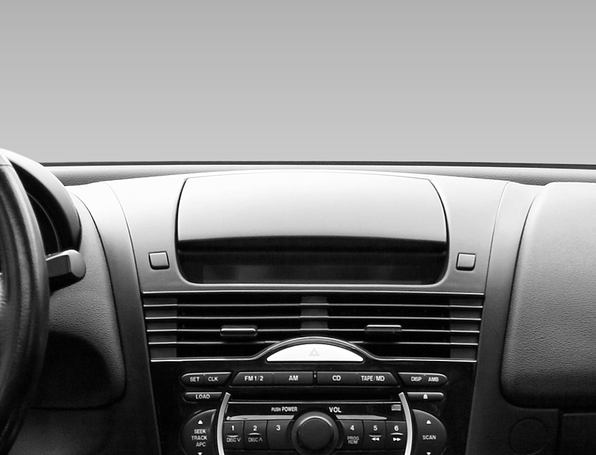
- Customer: Lon-so Plastic Injection Molding Co., Ltd.
- Industry: Precision Plastic Injection Molding Industry
- Solution: Moldex3D eDesign
- Region: Taiwan
Challenges
The cover of the automotive dash compartment is a component part which requires high quality surface appearance. A single gate is used to fill the mold in order to prevent weld lines and shrinkage from forming on the appearance.
Solutions
With the help of Moldex3D eDesign simulation solution package, Long-so manufacturers are able to identify product shrinkage problem areas and effectively minimize trial and error by validating and optimizing the design of plastic before production. This not only improves the quality but also facilitates the selection of machines and the production planning.
Case Study
It is hard to detect potential design defects at the earliest development phase, especially for exterior parts. In the past, the mold has to go through multiple iterations due to the inevitable occurrences of weld lines and sink marks during the development stage. Therefore, Lon-so was hoping to get the evaluation result of surface appearance before the production through the accurate simulation capabilities of Moldex3D software, generating analysis visualization result for product design review with customers.
Through the implementation of Moldex3D, the thickness of the rib area on the interior side of the product was found too thin and had flow hesitation problem, which would result in excessive injection pressure and partial short shots. After the production, the short shot did occur on the same area predicted by Moldex3D.
The part requires assembly after the injection molding ,and therefore multiple grooves and ribs were designed on the interior side of the part. With the accurate prediction of Moldex3D, it is found that due to the excessive thickness of the ribs, it’s more likely to result in continuous shrinkage and cause significant sink marks on the appearance.
The visualization of Moldex3D simulation analysis results can fully facilitates the communication process between Lon-so and its customers. As a result, Lon-so is able to provide improvement suggestions based on the early detection of possible surface problems. Using the insight gained from the early detection, Lo-so can help customers not only in solving product design problems, but also in reducing trial-and-error iterations. Moldex3D is definetly helping Lon-so ensure on-time delivery and product launch, and significantly increase competitve advantage.