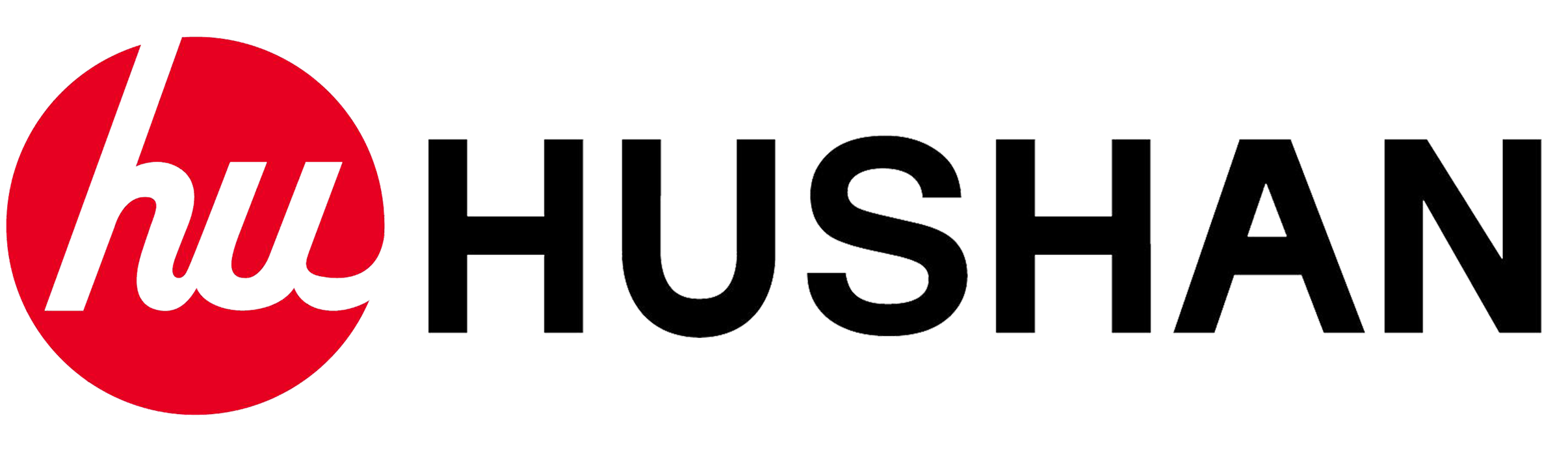
- Customer: Hu-Shan Auto Parts Inc.
- Industry: Automotive
- Solution: Moldex3D eDesign
- Region: Taiwan
Executive Summary
Facing serious weld line problems, Hu-Shan sought ways to enhance the appearance of door handle parts and hoped to achieve the following goals:
- Identify weld line locations
- Decrease weld lines through design changes
- Assess the manufacturing feasibility of various design options
Challenges
There’s an obvious weld line appearing at the end of filling. The mold manufacturer tried several times but failed to avoid the occurrence of the weld line. Hu-Shan hoped to use Moldex3D molding simulation software to verify designs and understand the cause of the defect.
Solutions
Using Moldex3D eDesign Package to generate true 3D meshes and changed the gate location and product thickness to improve the product design. The optimized design successfully reduced the wall thickness from 3.0mm to 2.0mm. Through adjusting the product thickness distribution and changing the cylinder from solid to hollow, Hu-Shan successfully reduced the weld line length from 9.5 mm to 4.3 mm.
Values
The cost to modify a mold like this is around $1,600 – $3,300 and $16,000- $33,000 for a set of molds. In this case, Hu-Shan used Moldex3D simulation software to evaluate 46 design options without making any actual tryouts, saving tremendous cost and time.
Case Study
In this case, Hu-Shan was trying to optimize the design of the interior door handle. The part was manufactured in single gate configuration and had weld line problem. Due to the demand for durability and aesthetics, the presence of weld-lines will reduce the mechanical strength and affect the surface appearance of the door handles. The presence of the weld line was found after the tool was built. In order to reduce cost and effort in fixing or rebuilding the mold, it’s important to identify the cause of weld lines and how to avoid it through Moldex3D simulation analysis. Through part adjustments, the weld line was reduced within the part tolerance.
The melt front time of the original design is shown in Fig. 3. And Fig. 4 shows the location of the weld line and its filling time. The meeting angle and the length of the weld line therefore can be identified.
Fig. 5 The meeting angle and the length of the weld line of the original design
The flow front meeting angle is an important indicator of weld lines. According to the meeting angle of the flow fronts, we can obtain the length of the weld line. Judging from the analysis result, when the meeting angle reaches 90°-135° above, the orientation of the plastic molecules becomes uniform with no presence of weld lines. Therefore, by testing multiple designs of gates and wall thickness, the optimal design and its design methods are shown below.
Wall Thickness Design Change:
Increased the wall thickness around the center and decreased the thickness of the middle plane to accelerate the flow front on the center. The design made the two fronts meet at the edge of the part, creating larger meeting angle and shorter weld line length.
Oblique Fillet Design Change:
Using the oblique fillet design to create wall thickness variation to speed up the melt flow at the center and slow down the melt flow on the periphery. This design made the two fronts meet each other with larger meeting angle and shorter weld line length.
Boss Design Change:
Changing the boss design from solid to hollow near the location where the fronts meet to reduce the melt volume filling in and avoid the flow hesitation happen on the left side.
The optimized flow result is shown below:
Fig. 12 The meeting angle and the weld line length after design changes
Conclusions
Through Moldex3D CAE simulation results, Hu-Shan found that changing thickness distribution can adjust the melt front advancement speed and further solve weld line problems.
In this project, Hu-Shan made changes on the structure, the thickness distribution and the gate location. The meeting angle was improved by the changing the structure and the gate location to reduce the wall thickness and the structure angle. The original weld line length was 9.5 mm. It has been decreased by around 50% to 4.3 mm after making design changes.
Using Moldex3D simulation tool, Hu-Shan conducted 46 groups of designs to understand the cause of weld lines and to further verify an effective design method to avoid weld lines taking place on the surface of door handles.
Using Moldex3D CAE simulation, Hu-Shan was able to verify changes in wall thickness and gate locations before actual manufacturing, avoiding costly tool tryouts. Based on the simulation result, Hu-Shan was able to optimize the design and the weld line length, significantly improving the product appearance and product strength affected by weld lines.