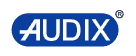
- Customer: Audix
- Region: Taiwan
- Industry: Electronics
- Solution: Moldex3D Advanced Package
- View PDF Version
Audix is a semiconductor/electronic component distributor and expanded to certification and manufacturing. Manufacturing Group within Audix produces back light modules, relays, transformers, precision molds, plastic injection products, and also electroplating and automated machinery. A joint venture with Japanese enterprise located in Wujiang produces large-sized CCFL for TVs and monitors. (Source: www.audix.com/index_en.aspx)
Executive Summary
This case features a high voltage connector made from PBT, a thermoplastic crystalline polymer ideal for connector applications. Because of its crystalline nature, serious shrinkage problems may occur. The challenge lies in the fact that the product size accuracy is highly demanded to meet the stringent electronic assembly requirement. Also, visible appearance defects such as air traps or short shots are not allowed. Therefore, how to simultaneously achieve the size accuracy and eliminate appearance defects is the main issue in this case. Audix used Moldex3D to analyze the volume shrinkage distribution and adjusted the thickness in the high volume shrinkage region. Audix also adjusted the gate size to eliminate air traps. Audix was able to successfully solve the shrinkage problem and eliminate visible appearance defects in time to enable an effective workflow forproduct mass production.
Challenges
- Improve size accuracy
- Eliminate visible appearance defects
Solutions
Audix used Moldex3D to evaluate the part thickness and gate design and was able to achieve the optimal product optimization in the early product development stage.
Benefits
- Improved size accuracy up to 77%
- Reduced mold trial cost and development time
Case Study
The purpose of this project is to solve the shrinkage problem around the holes on a high-voltage connector in order to meet the accuracy requirement (as shown in Fig. 1). The unexpected high shrinkage around the holes exceeded the pre-set tolerance. In the meantime, air traps would occur if Audix tried to improve the product shrinkage by slimming down the part thickness. Thus, how to achieve the size accuracy and eliminate the visible appearance defects simultaneously would be the primary objective of this project.
Fig. 1 Shrinkage problem around the holes
After finding the high volume shrinkage region, Audix proposed a new gate design by increasing the gate number from a single gate to a doubled-gate design, one gate on each side (Fig. 2). The doubled-gate design reduced the maximum volume shrinkage from 17% to 14% according to Moldex3D’s simulation results.
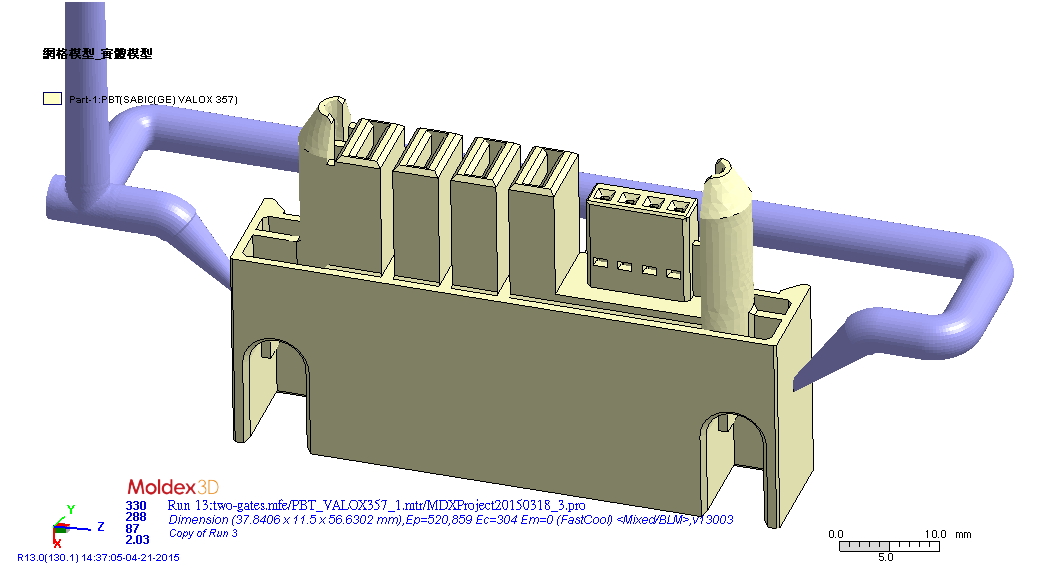
Fig. 2 The original design (left) has only one gate. The gate number in the revised design (right) is increased to 2 gates
Apart from the gate design, the part thickness was modified as well. Audix proposed two different thickness reduction designs. In Design 1, the part thickness at both core and cavity sides are reduced separately in order to meet the geometry aesthetic requirement. Fig. 3 highlights the reduced material locations and the volume shrinkage result. However, the volume shrinkage was not improved as much as expected in Design 1.
Fig. 3 Design 1: Reduce materials at the core side and cavity side
In Design 2, the part thickness is further reduced by modifying the slider based on Design 1 (Fig. 4). The simulation results showed that Design 2 can effectively decrease the volumetric shrinkage values at the specific regions. Besides, the volume shrinkage distribution became more uniform after the modification. However, this modification would cause the occurrence of air traps at the side wall (Fig. 5). Hence, Audix enlarged the gate size from 1 mm to 1.5 mm in an attempt to move the air trap location from the side wall to the parting surface.
Fig. 4 Design 2: Reduce materials from sides
Fig. 5 Air trap problem in Design 2
According to the simulation, Audix measured the length of the 4 holes at the top and the bottom of the part to evaluate the size accuracy after shrinkage. The simulation results showed that the length at bottom 1 and bottom 4 after shrinkage exceed the requirement in the original design. In Design 2, the accuracy successfully improved up to 77%, qualifying the part for production.
Audix had conducted a short shot test to verify Moldex3D’s reliability. As shown in Fig. 6, the melt front simulation accurately displays the flow behavior during injection. Furthermore, when Audix compared the actual mold trial with the simulation results of Design 2, they found that the air trap location is coincident with the simulation result as shown in Fig. 7.
Fig. 6 Melt front comparison between the experiment and simulation results
Fig. 7 Air trap comparison between the experiment and simulation results in Design 2
Results
With Moldex3D simulation, Audix could understand the flow behavior inside the mold and find potential problems before an actual molding. The accurate prediction helps Audix reduce the cost of mold trials and development time as well as improve the product quality.