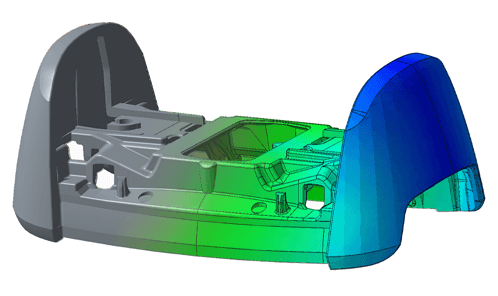
CAD & MESH
CAD (Computer-Aided Design) and CAE (Computer-Aided Engineering) are two important tools used in modern engineering and design. CAD is used to create digital models of products while CAE is used to analyze the behavior of these products under different conditions. To transfer a CAD model to CAE, a mesh is generated and this process involves several steps including CAD import, geometry preparation, mesh generation, mesh optimization. CAE analysis need sophisticated mesh to achieve accurate result. The combination of CAD and CAE tools allows designers and engineers to create more innovative and optimized products.
Moldex3D meshing technology is a powerful pre-processing tool with robust meshing technologies and different mesh elements combinations to boost the work efficiency in mesh preparation, which can generate very fine mesh for complicated 3D geometry. It also provide auto-check and auto-fix functions to ensure the mesh quality for the accuracy of analysis.
We also have Moldex3D SYNC – CAE tool in CAD software – which provide seamless CAE analysis in CAD software to help engineer modify product design based on complete analysis result, without data transfer.
Overall, the combination of CAD and CAE tools allows designers and engineers to create more innovative and optimized products with greater efficiency and accuracy.
Capabilities
- Moldex3D support geometry/mesh import, creation, repair, attribution and wizards to create runner, gate, part, cooling channel, moldbase, etc.
- CAD Geometry Model: CAD model can import from Rhino, Creo Parametric, NX, CATIA V5, and, as well as CAD file like Parasolid, STEP, IGES, STL, JT.
- Moldex3D CADdoctor: CAD model repair for fine mesh generation
- Mesh Technology: 2.5D Shell & 3D Solid (eDesign, BLM, Hybrid)
- Mesh types: Tetra, Pyramid, Prism, Hexa, Voxel
- Support automated or customized mesh generation
- Non-Matching Face Technology
Features
Moldex3D CADdoctor
- Geometry check and auto/manual geometry healing
- Simplification:auto remove small features
- Integrated with Solid solution
Shell (2.5D Mesh)
- Suitable for most conventional parts with over 75% thin part (L/D > 10)
- Moldex3D simulation with Shell mesh is numerically efficient and robust.
- Easy for design change
Auto 3D Meshing Engine (eDesign)
- Auto-meshing features and powerful wizards
- User-friendly interface with intuitive setting guidance
- Simple, fast, and efficient modeling and variant mesh preparation
High Resolution 3D Mesh Technology (BLM)
- Auto mesh generation with more precise quality for model preparation, especially for complicated 3D geometry
- Enhance solver accuracy for viscous heating, pressure simulation, and warpage prediction
- Support tetra, pyramid, prism, and hexahedral for boundary layer mesh (BLM) and robust non-matching technology
- Accurate, precise, and efficient for advanced molding processes
- For more information, please check BLM
Hybrid Structure Mesh Technology
- Manually create mesh for customized purpose
- Increase mesh resolutions significantly with acceptable element count
- Control uniform or biasing mesh pattern and element layer count in thickness direction
- Support tetra, pyramid, prism, and hexahedral elements
- Flexible, delicate, and accurate for complex geometry shapes
Non-Matching Face Technology
- No need to match the contact face mesh so making the mesh becomes easier and less time consuming
- Reduce the barriers to simulate between different materials for better resolution and analysis accuracy
- Non-matching mesh is based on BLM mesh
- Support non-matching mesh topology on the contact faces between part, part insert, mold insert, cooling channel and moldbase / mold plate