- Customer: Chung Yuan University
Mold Automation Education Resource Center (MAERC) - Region: Taiwan
- Industry: Research & Education
- Solution: Moldex3D Advanced / Gas-Assisted Injection Molding
- View PDF Version
Executive Summary
MAERC utilized Moldex3D’s simulation technology to visualize a potential wax injection scenario with GAIM implementation. Through Moldex3D’s analyses, MAERC was able to get an in-depth look at the implementation of gas-assisted injection molding in the wax injection stage of the investment casting process, and further proved it a viable option for its competitive advantages over the conventional wax injection molding.
Challenges
Defects like short shots, flash, cracking, bubbles, shrinkage, etc. are some common defects in the wax injection stage of the investment casting process. Moreover, the following problems are most likely to occur for wax parts generally with varying wall thickness:
- Inconsistency in meeting the product specification requirement
- Product warpage induced by severe shrinkage
Fig. 1 The common defects in the wax injection stage of the investment casting process
Solutions
With Moldex3D’s gas-assisted injection molding (GAIM) module, the team could observe the injected wax filling patterns and the gas penetration behavior inside the mold cavity. Various parameters including gas holding time, pre-filling percentage (short shot), and melt temperature are important factors to understand the gas penetration behavior in the wax injection molding.
Benefits
This case study shows that
- The gas penetration behavior in the wax injection stage of the investment casting process can be accurately predicted by Moldex3D which serves as a great reference for future technology implementation and mold design.
- Applying GAIM technology in the wax injection molding can significantly reduce the volumetric shrinkage by 48%.
Case Study
Gas-assisted injection molding (GAIM) has been widely applied in the plastic product manufacturing industry and it offers a number of benefits including reduction in weight, material, cycle time, and cost while increasing quality and efficiency. The gas penetration behavior contains two parts (See Fig. 2):
- Primary Gas Penetration: During filling stage, gas penetrates the material and further advances the melt front. Gas penetration completes when the mold cavity is filled with the injected material and gas.
- Secondary Gas Penetration: During packing stage, gas core out continues to expand forward to compensate the volumetric shrinkage of the plastic as it cools.
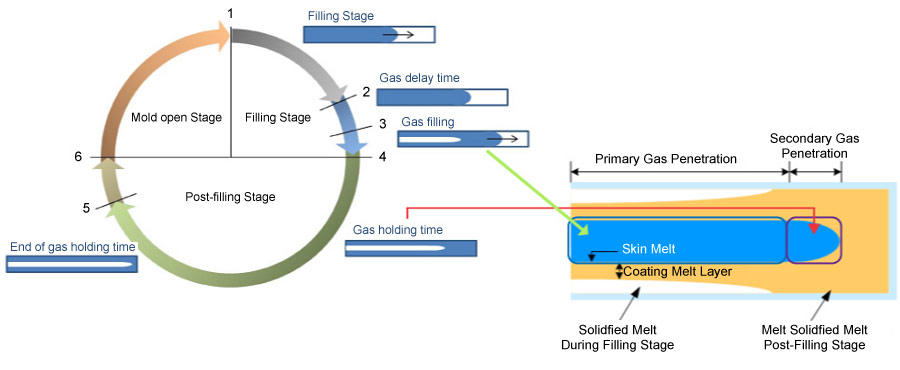
Fig. 2 Gas penetration behavior in the GAIM process
The purpose of this study is to focus on the implementation of GAIM technology in metal product development with the goal of taking advantage of the benefits GAIM offers to improve the investment casting process and product quality. Wax injection is the first step in the investment casting process (Fig. 3); if we are able to control the wax injection precision at this stage, the overall investment casting process and product quality can be greatly elevated and enhanced.
Fig. 3 Wax injection is the first step in the investment casting process.
First of all, MAERC conducted a full spectrum of wax material testing including viscosity, PVT, heat capacity, thermal properties and other measurements. Then, the material property data was imported to Moldex3D CAE software to simulate the wax injection and gas penetration behavior. After attaining the simulation analyses, MAERC compared the simulation results with the experiment results; important parameters that have a direct impact on the gas penetration including gas holding time, pre-filling percentage(short shot), melt temperature are studied here in order to get a comprehensive understanding on applying GAIM in the wax injection stage of the investment casting process.
1. Gas holding time vs. Total penetration length (See Fig. 4): The total penetration length including both primary and secondary gas penetration is increased as the gas holding time increases.
Fig. 4 Gas holding time vs. Total penetration length
2. Pre-filling percentage (short shot) vs. Total penetration length (See Fig. 5): The total penetration length including both primary and secondary gas penetration is shortened as the pre-filling percentage (short shot) increases.
Fig. 5 Pre-filling percentage (short shot) vs. Total penetration length
3. Melt temperature vs. Total penetration length (See Fig.6): Higher melt temperature results in a thinner solidified surface layer which makes the primary penetration length shorter; however, higher temperature in the core region would increase the secondary gas penetration length.
Fig. 6 Melt temperature vs. Total penetration length
From the comparisons above, MAERC concluded that Moldex3D’s GAIM simulation analyses on the wax injection had a high correlation with the experiment results; thus, demonstrating the value of using Moldex3D to accurately predict the molding behavior. Moreover, this case study further shows that under the same circumstances, implementing gas-assisted injection molding in the wax injection stage of the investment casting process can greatly improve the volumetric shrinkage by 48.7% when compared to the traditional casting process. As a result, MAERC was able to prove that applying GAIM technology in the wax injection stage, the stability of the part dimensional control of an investment casting product can be significantly enhanced.
Fig. 7 Implementing GAIM technology in the wax injection can greatly improve the volumetric shrinkage by 48.7%
Results
Furthermore, through Moldex3D’s simulation analyses, the product deformation problem, either the volumetric shrinkage (Fig.8) or the total displacement (Fig.9) can be greatly improved when applying the GAIM technology in the part with varying wall thickness design. Thus, the product defect ratio can be drastically lowered. In addition, GAIM possesses the ability of hollowing the core of the part, making it effective for cooling. In this way, the production cycle can be substantially shortened compared to the traditional casting process. In short, with the help of Moldex3D’s simulation capabilities along with the actual experiment results, MAERC was able to establish a systematic study on the gas-assisted wax injection molding and further proved its viability in today’s modern manufacturing, specifically for parts with varying wall-thickness design.