Thomas Chiu, Senior Architecture Manager at Product R&D Division of CoreTech System (Moldex3D)
Introduction
Compression molding is commonly used for thermosetting plastics. The plastic is preheated and placed into an opened mold cavity. During the process, the mold compresses the plastic to fill the cavity while applying heat for curing. Common applications include mechanical parts, tableware, electric vehicle batteries, etc.
Factors that affect compression molding before mold closed:
Before compression molding, the distribution and geometry of the charge significantly impact the molding result. In contrast to injection molding, where the melt is injected into mold cavity after mold closure, gradually filling the cavity and solidifying due to mold temperature, the molding outcome primarily depends on the mold-closed status. In compression molding, results are affected by the position and shape of charge before mold is completed closed. The varying contact area between the charge and mold leads to temperature variations. (refers to Fig 1 and Fig 2)
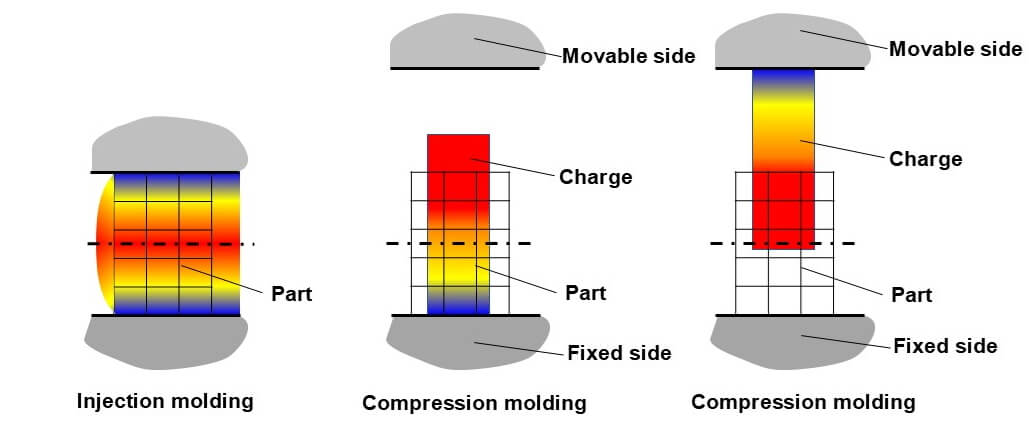
Fig 1 Initial contact positions of plastic on the mold in various scenarios.
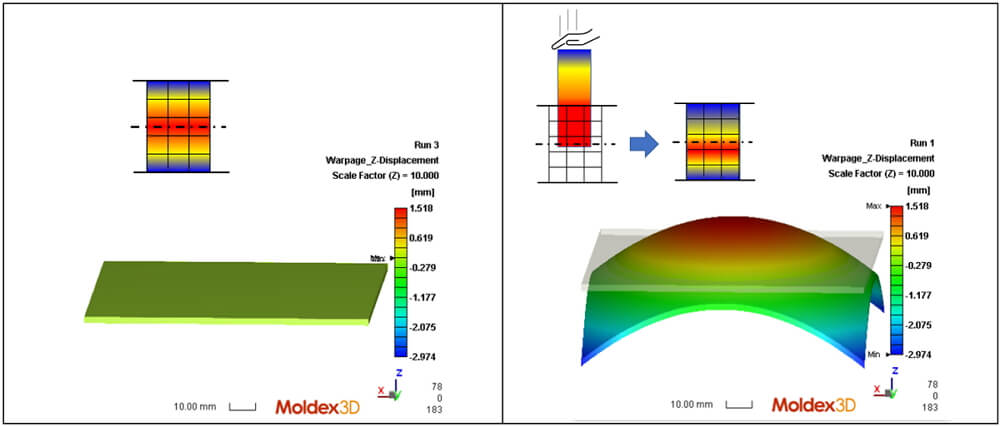
Fig 2: Warpage direction affected by initial temperature distribution of plastic
Impact of Mold Closure on Compression Molding Results:
After mold closure, plastic is completely enclosed by the mold, resulting in a different interaction with the mold boundaries compared to pre-closure state. The influences of cooling channel on the plastic also varies. Taking a plastic plate as an example, a mold can be designed so that the plastic equally contacts the core and cavity under mold-closed status. However, mold opening results in one side of cooling channels moving farther away from the plastic part. During simulation, if the mesh is calculated in mold-open status to place charge, the distance between cooling channels (or heating elements) and plastics will differ. This leads to temperature deviations between two mold sides, which will affect warpage results.
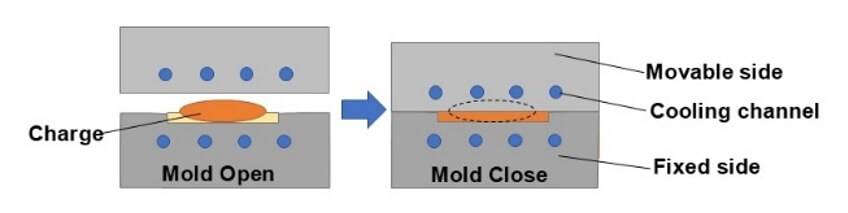
Fig 3: The warpage direction is affected by the initial temperature distribution of the plastic.
Considering both the position of charge before mold closure and the location of cooling channels after mold closed, should the pre-processing utilize a mold-open mesh or mold-closed mesh?
The Cooling Channels (or heating elements) Move through the Mold
Moldex3D provides a solution that users can create a mold-open mesh to decide the mesh movement distance and automatically proceed mold-closing calculations from mold-open state. This approach avoids the issue of in-mold constraint between charge and mesh under mold-closing condition. Through post processing function, users can observe mold temperature distribution while also visualizing the mold movement over time, providing a more intuitive molding process.
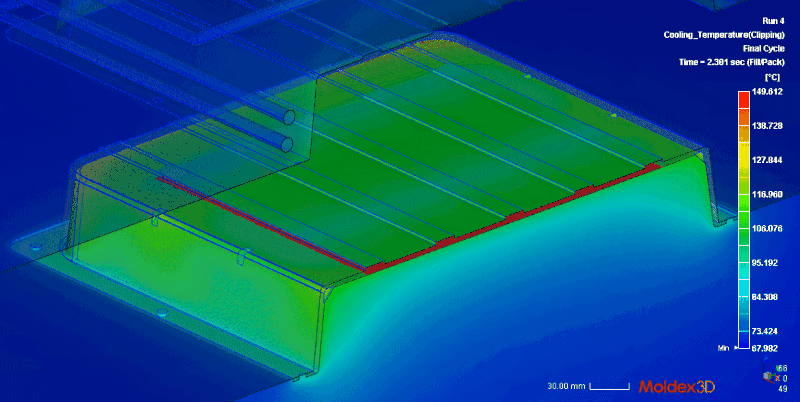
Fig 4: Dynamic mold temperature distribution display during mold movement
Conclusion
Compression molding is highly affected by the mold’s open and closed phases. Unlike injection molding, more factors need to be considered during compression molding. Moldex3D provides a solution where users can define mold-open status and mold movement. Then, software can automatically simulate the process of mold-open to mold-closed, offering users more detailed compression molding results and assisting them in gaining a better understanding of the compression molding process.