Dr. Huan-Chang (Ivor) Tseng, R&D Program Manager at CoreTech System (Moldex3D)
Fiber-reinforced thermoplastic (FRT) composites have been commercially available for reducing vehicle weight and improving fuel efficiency in the automotive and aerospace industries. They can be processed by fast, highly-automated methods such as compression molding and injection molding. The fibers and the resin are transported into the mold cavity. The anisotropic flows of fiber-reinforced melts depend significantly on fiber orientation states. For the practical compression-molded glass-mat thermoplastics (GMTs), it is important that the fiber-orientation-induced anisotropic flow is found in a circular disk squeezed and deformed into an elliptical shape (Fig. 1) [1]. Typically, the injection-molded melt front of a neat resin is smooth and the continuous shape is maintained in the propagation of the free surface (Fig. 2) [2]. Some peculiar, irregular filling patterns for short/long fiber-reinforced melts at high fiber concentrations are known to occur: the free surface advancing faster along the sidewalls of the cavity.
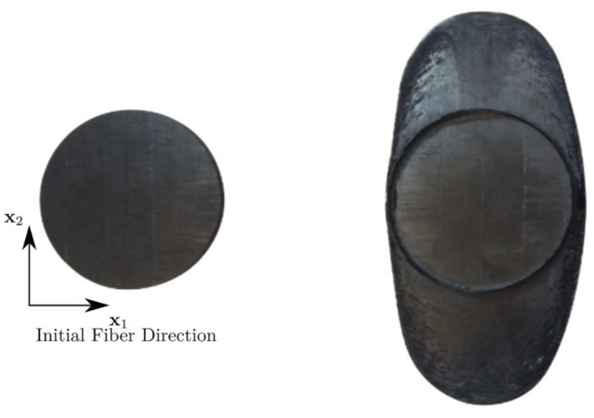
Fig. 1 A circular disk is squeezed and deformed along the 1-axial direction into an elliptical shape for the 1-axial uni-directional charge [1].

Fig. 2 Schematic of mold filling behavior for (A) neat resin; (B) FRT [2].
In the Purdue-Moldex3D research cooperation, the informed-isotropic (IISO) viscosity developed by Dr. Favaloro and Prof. Pipes (Composites Manufacturing and Simulation Center, Purdue University in the US) has been implemented in the Moldex3D simulation software. It is important to validate an anisotropic flow simulation for injection molding and compression molding in Moldex3D. More recently, it is significant that the details of the IISO model have disclosed in the US patents [3, 4] and published in the scientific journals [5, 6].
In Moldex3D’s simulation, the compression molding system wherein the initial orientation distribution of the charge is the X-axial uni-directional (Fig. 3). The material of interest was Polypropylene melt (200°C) filled with 25 volume percent long glass fibers (aspect ratio, L/D = 360). The final melt front is an obvious ellipse from the original circle charge (Fig. 4). In addition, the simulated melt front primarily exhibits a free surface advancing faster along the side walls in the injection molding simulations for the 50wt% short glass fiber (aspect ratio, L/D = 20)-reinforced Polyamide66 (Fig. 5).
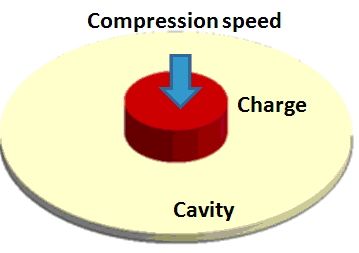
Fig. 3 The Moldex3D compression molding simulation.
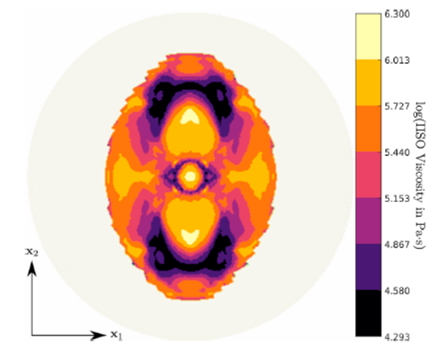
Fig. 4 The final melt front for the X-axial uni-directional charge [5].
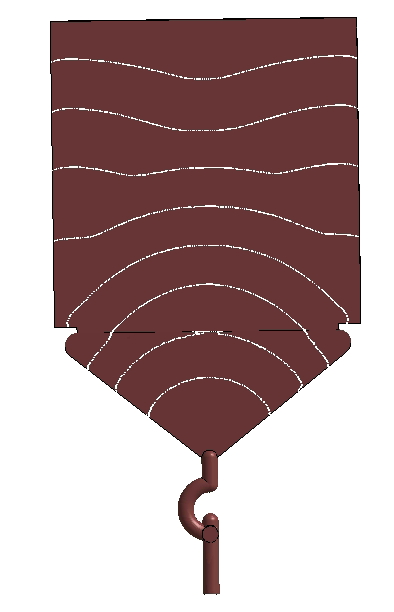
Fig. 5 The simulated melt front of anisotropic flow in injection molding [6].
So far, simulating such a fiber-orientation-induced anisotropic flow has still been a challenge for state-of-art CFD software, indeed. Therefore, the ability of the IISO viscosity is critical to dominate the anisotropic flow. In the current Moldex3D version, the NEW fiber coupling function will be widely available for the industries of the injection and compression molding processes of fiber composites.
Reference Source: