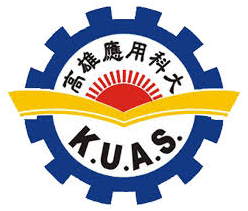
- Customer: Kaohsiung University of Applied Sciences
- Region: Taiwan
- Industry: Research & Education
- Solution: Moldex3D Advanced; MCM Module
- View PDF Version
Executive Summary
Common injection molding defects such as surface sink marks, jetting marks and voids often occur on thicker plastic parts due to the fact that thicker plastic parts require longer cooling time. Longer cooling time will definitely affect production efficiency. The following case study features an optical lens with a wall thickness of 12mm. The concept of multi-component molding (MCM) sandwich molding was implemented in the form of B-A-B molding sequence layer design. Moldex3D MCM module was utilized to investigate how the thickness of each layer affects cooling time and optical properties. The final goal of this case is to find the best combination of layer thickness to achieve optimal product quality with shorter cycle times.
Challenges
- To find the optimum layer thickness combination to reduce the cooling time
- To achieve better optical properties such as transparency and residual stress
Solutions
Utilizing Moldex3D MCM module to optimize layer thicknessto reduce cooling time
Benefits
- Cooling time was drastically shortened by 50%-60%
- Sink displacement was decreased by 85%
- Residual stress was significantly eliminated
Case Study
This project focuses on how to adjust the thickness ratio of the middle layer and side layer to obtain shorter cooling time and better optical properties. The major problem is that cooling time of the 12 mm optical lens (Fig. 1) is too long. According to Moldex3D cooling analysis, the original design required 384 seconds to reach ejection temperature. In addition, serious sink marks were detected in Moldex3D warpage analysis due to poor heat dissipation.
Fig. 1 The case features an optical lens with 12mm thickness
To solve the above problems, the KUAS Team used MCM process to manufacture optical lens. The first shot generates the middle layer (Layer A) of the thick lens, and then the second shot injects the side layers (Layer B) to complete the 12mm lens part (Fig. 2). The question then arises: how do you define the optimum layer thickness of each shot? 4 sets of layer design are proposed and examined by Moldex3D, whichprovides the cooling time estimation of different layer thickness for design guidance. The cooling time results reveal that the revised design with 6mm middle layer and 3mm side layer has the minimum cooling time of 172 seconds. The cooling time has been reduced by 55% (Fig. 3).
Fig. 2 Two shots will generate the middle and the side layers
Fig. 3 The cooling time has been reduced from 384s to 172s.
The residual stress measured in the original design matched well with Moldex3D fringed pattern analysis (Fig. 4). Furthermore, the sink mark and optical properties such as transparency are examined as well. Fig. 5 shows the sink mark and transparency measurement results. The sink mark displacement was reduced greatly and varied proportionally based on the thickness of the top and the bottom. The transparency of the revised design is closely similar to the original design.
Fig. 4 The residual stress measurement of the original design matched well with Moldex3D fringed pattern analysis.
Fig. 5 The sink mark and transparency measurement results
Results
Moldex3D can help predict the cooling time and further investigate the optical properties to improve lens quality. The simulation result of residual stress is correlated with the experimental data, thus, validating the accuracy and reliability of Moldex3D simulation. With Moldex3D’s help, the KUAS Team successfully identified the best combination of layer thickness and reduced 55% of cooling time to attain optimal optical quality.