This page is available in following languages: English │ 日本語 │ 한국어 │ 繁體中文 │ 简体中文 │ ไทย │ Tiếng việt │Italiano │ Русский
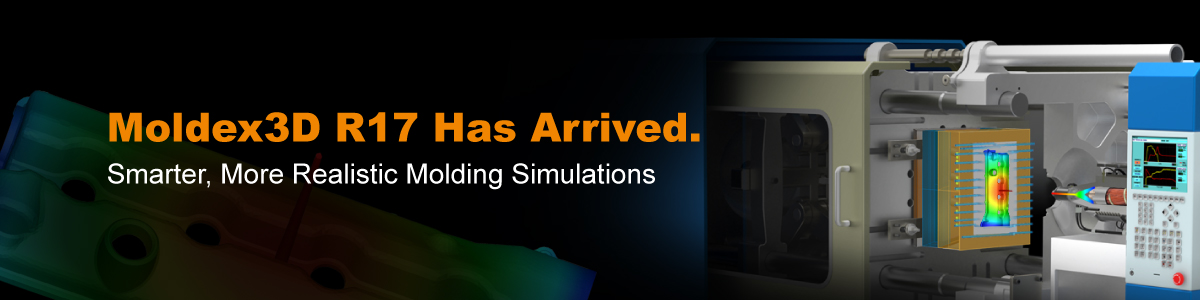
What’s New in Moldex3D R17
Next-gen molding simulation solutions designed to pave the way for smart design and manufacturing with realistic simulations, critical insights.
![]() |
Unified Platform, Greater Insights |
![]() |
Breakthrough Composites Simulation Capabilities |
![]() |
Get Closer to Real-world Manufacturing |
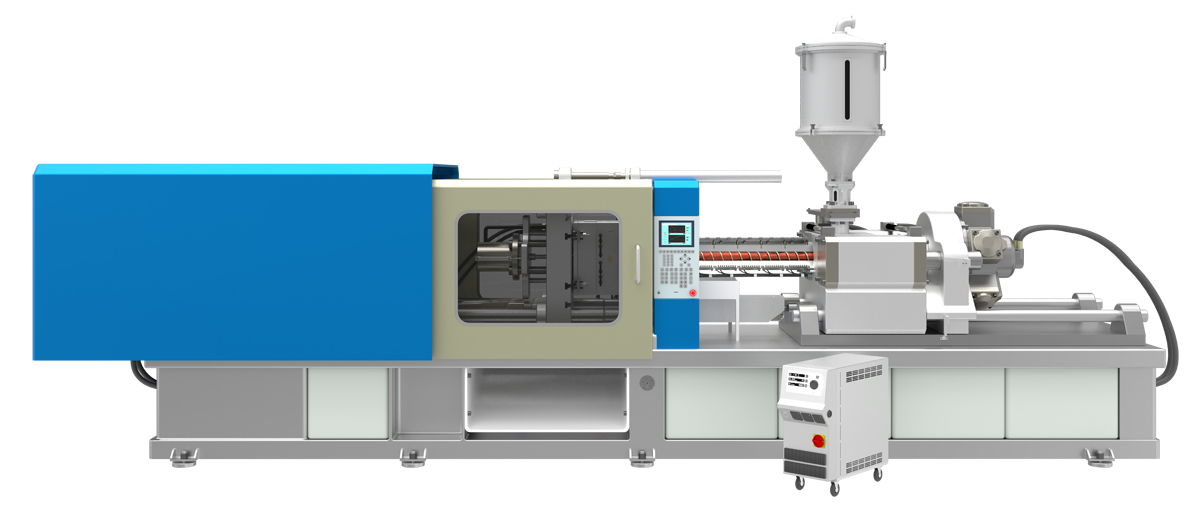
Bringing Simulation One Step Closer to Reality
Using the newly released Moldex3D R17, engineers can better integrate the physical world into the digital world to accurately reflect real-world manufacturing conditions in simulations.
Simulate Real-World Machine Response
Since machine response varies from one machine to another, Moldex3D R17 enables users to consider the dynamic characteristics of an injection molding machine in simulations to more closely represent the real world conditions. The optimized processing conditions obtained from the simulation can then be directly applied on the shop floor, bridging the gap between simulation and manufacturing. With barrel compression functionality, users can simulate the compression behavior inside the barrel and nozzle to take into account its effect on material compressibility when injecting into the cavity, producing a more accurate injection pressure prediction.
Download What’s New ⤓ |
Watch On-demand Webinar: What’s New in R17 > |
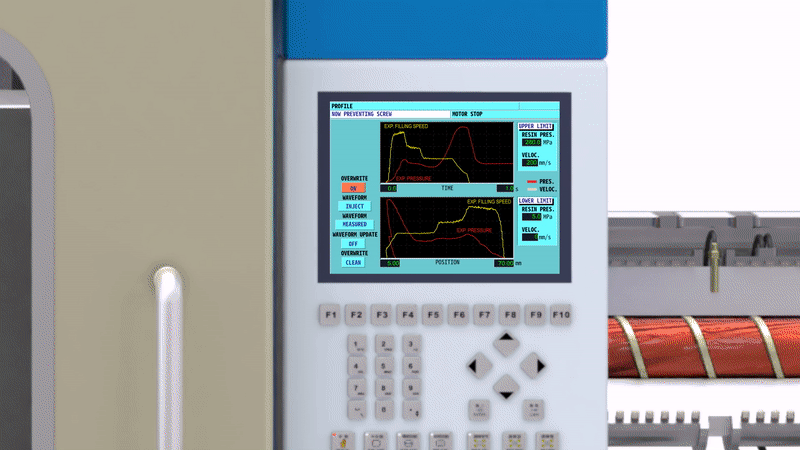
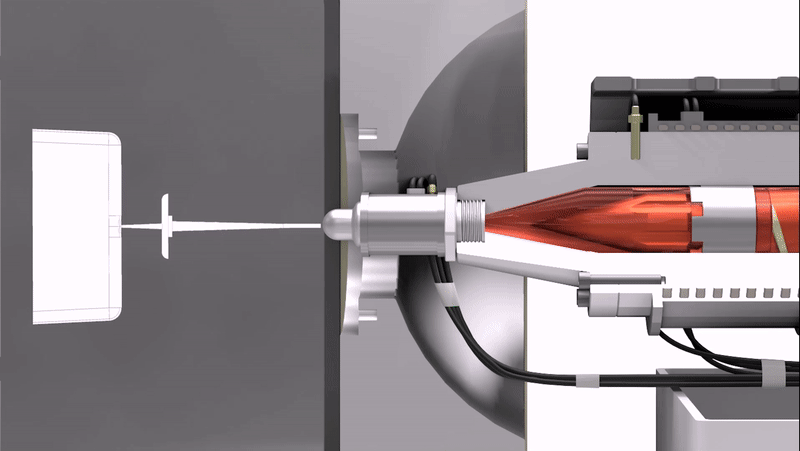
Mold Temperature Controller Advisor
Moldex3D Cooling Channel Analysis provides crucial data, including maximum pressure drop, total flow rate and heat dissipation, all of which help users to better evaluate the performance of mold temperature controllers and ensure all requirements are met.
Download What’s New ⤓ |
Watch On-demand Webinar: What’s New in R17 > |
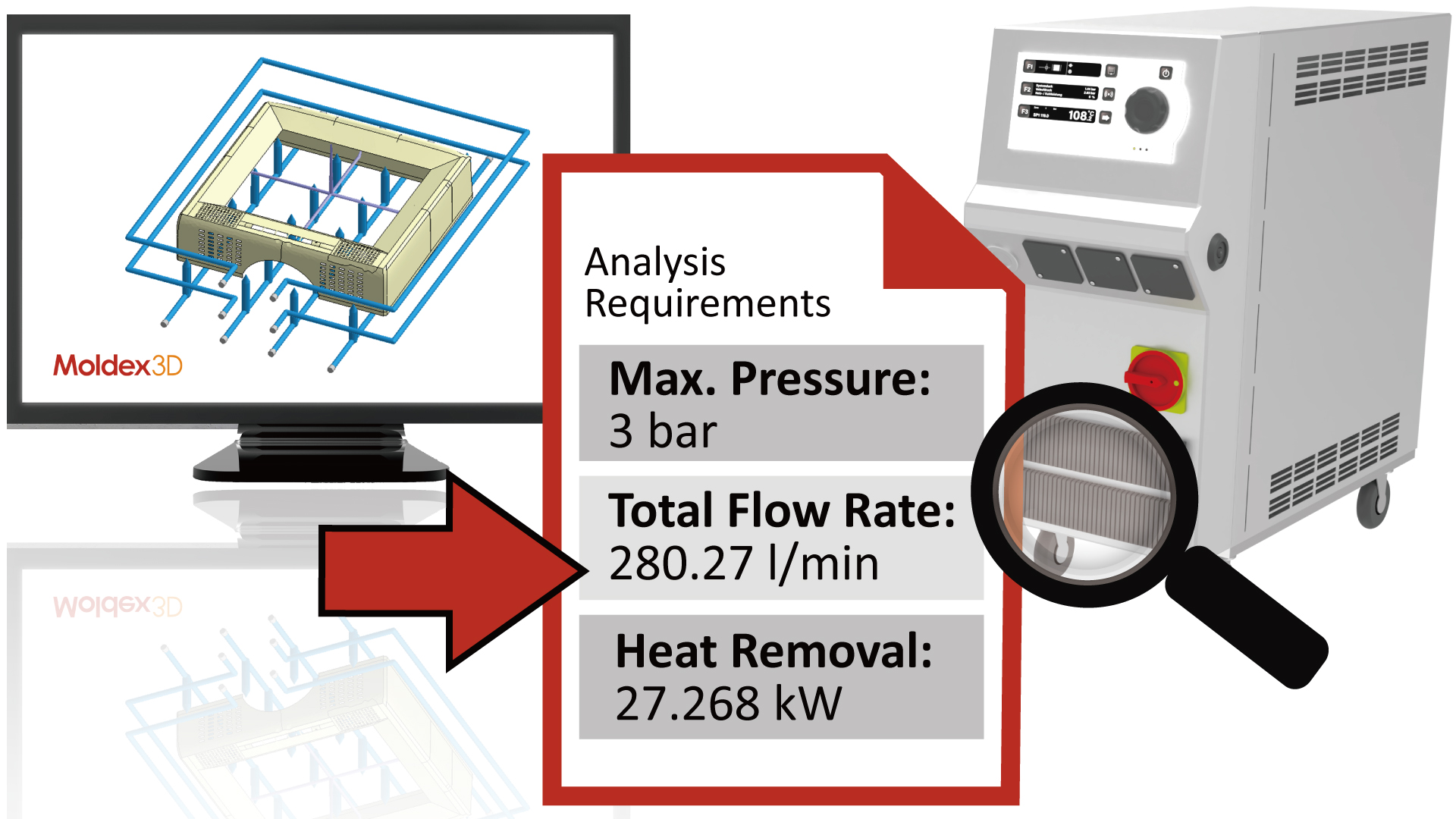
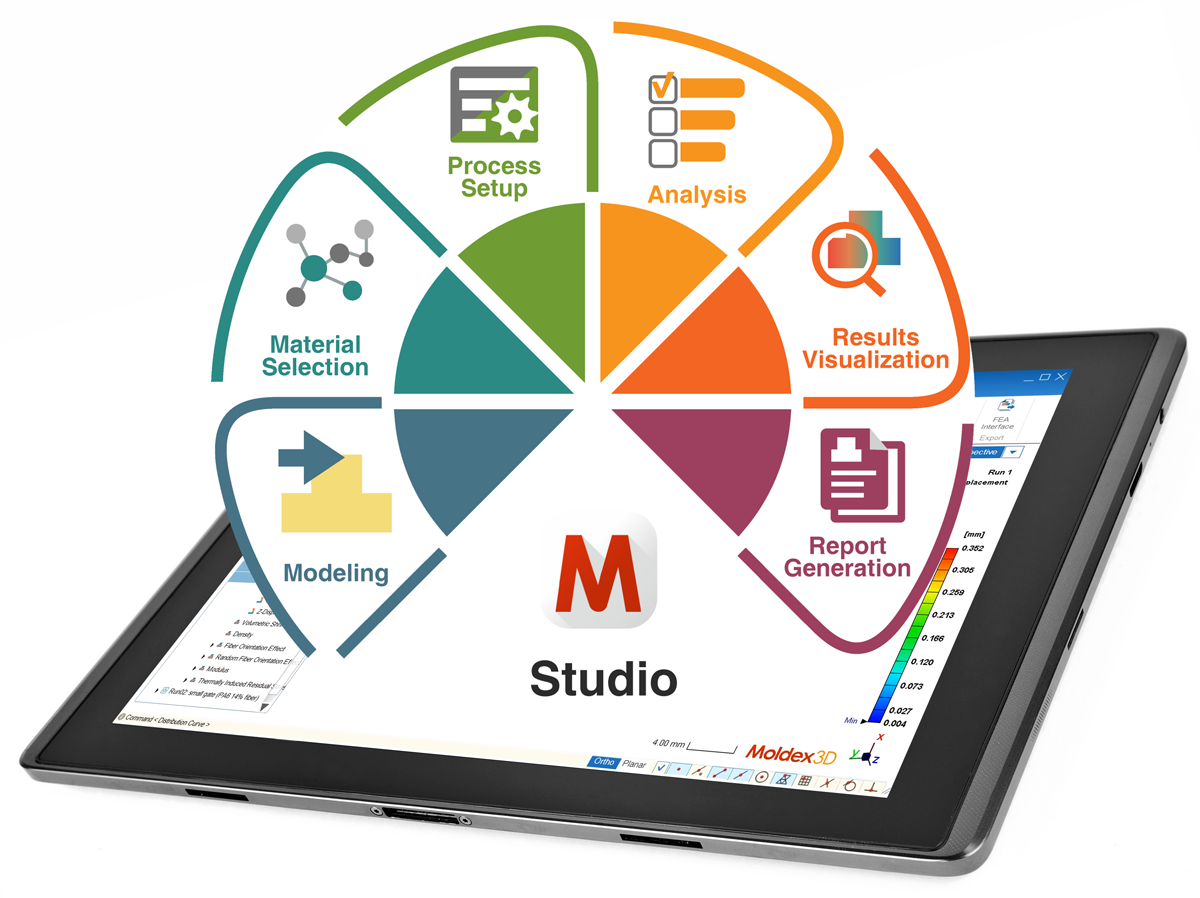
A Unified Platform for Deeper Insights,
Better Decisions
Designed as a single, unified platform for greater efficiency and usability, Moldex3D Studio empowers engineers to unlock hidden insights from simulation data and make better design decisions faster and easier than ever before.
Faster Visualization with Less Memory Usage
- Up to 50X faster rendering performance
- 60% reduction in memory usage
New Ways to View, Interact, and Interpret Your Simulation Data
- Get deeper insights into product design with more powerful result visualization capabilities, including History Curves, Distribution Curves and Thickness Distribution Curves
- Easily predict deformation and make design changes with Measurement and Scale functions to compensate for shrinkage
Meet All Your Simulation Needs
- Support a wide range of advanced molding processes, such as Compression Molding, Gas/Water-Assisted Injection Molding, Powder Injection Molding, Co-injection Molding, Injection Compression Molding and more.
Download What’s New ⤓ |
Watch On-demand Webinar: What’s New in R17 > |
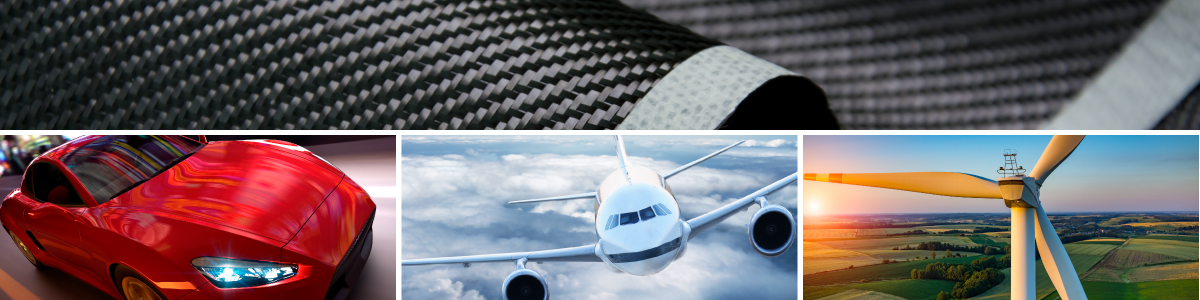
More Realistic Modeling of Material Behaviors
and Molding Processes
Moldex3D has always inspired continual innovation in simulation. In R17, Moldex3D presents new capabilities with a higher level of accuracy, which enable engineers to make confident predictions of actual material behaviors and molding processes, taking a significant step forward in shaping the future of plastics molding.
Breakthrough Flow-Fiber Coupling Analysis
A novel coupling approach to more realistically and accurately describe the anisotropic flow behavior induced by fiber orientation. This functionality is important for composites applications with high concentration of fibers and high accuracy requirements.
Download What’s New ⤓ |
Watch On-demand Webinar: What’s New in R17 > |
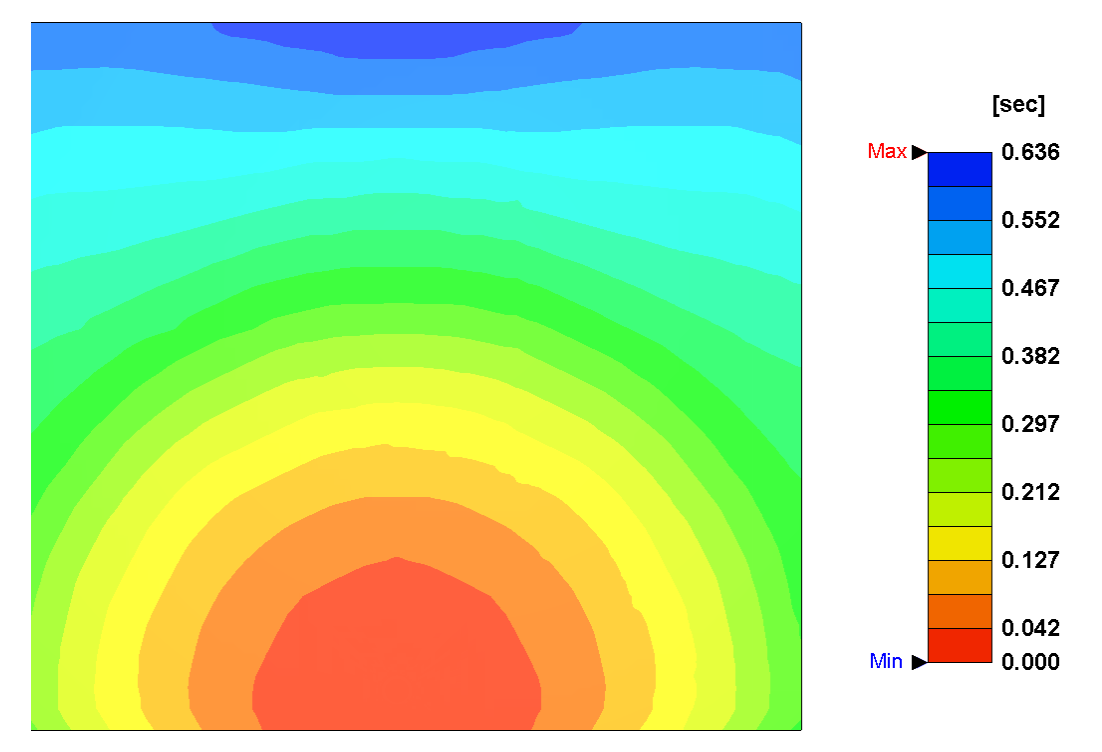
Flat Fiber Orientation Simulation
The fiber orientation simulation capability has now been extended to support a new filler type—flat fibers. The fiber orientation analysis for flat fibers will enable greater design freedom and help achieve better mechanical properties and improved dimensional stability.
Download What’s New ⤓ |
Watch On-demand Webinar: What’s New in R17 > |
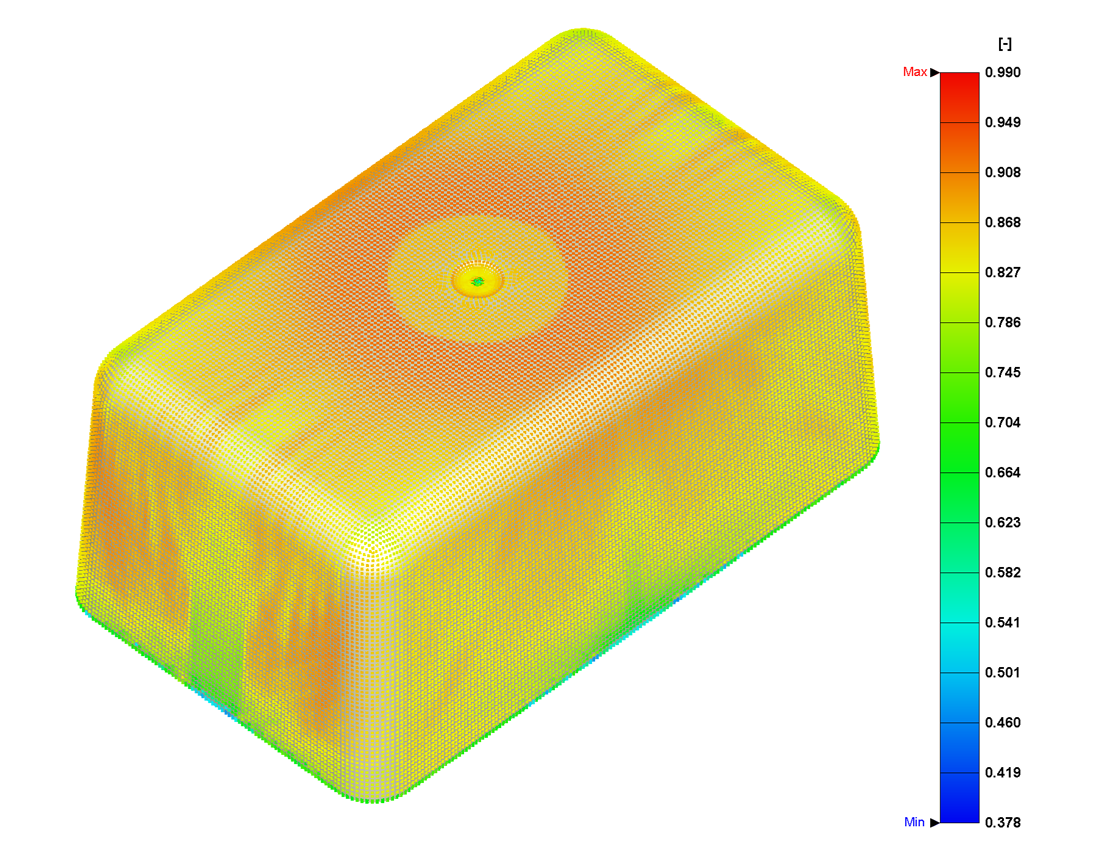
Consider Expansion Ratio in PU Chemical Foaming Analysis
Moldex3D Material Lab provides comprehensive material testing services for characterizing the expansion ratio of the polyurethane foam, enabling users to consider the expansion ratio in the PU Chemical Foaming analysis, achieving greater accuracy in predicting foam height and shape, to ultimately achieve a more optimal foaming process.
Download What’s New ⤓ |
Watch On-demand Webinar: What’s New in R17 > |
![]() |
Fluid-assisted Injection Molding with Push Back Simulation
Moldex3D GAIM and WAIM modules now support simulating push back by visualizing how the melt is pushed by the gas/water back into the molding machine barrel. With R17, users can better investigate the gas/water penetration behaviors to produce hollow, lightweight parts, reducing material waste and providing better surface quality than the short-shot method.
Download What’s New ⤓ |
Watch On-demand Webinar: What’s New in R17 > |
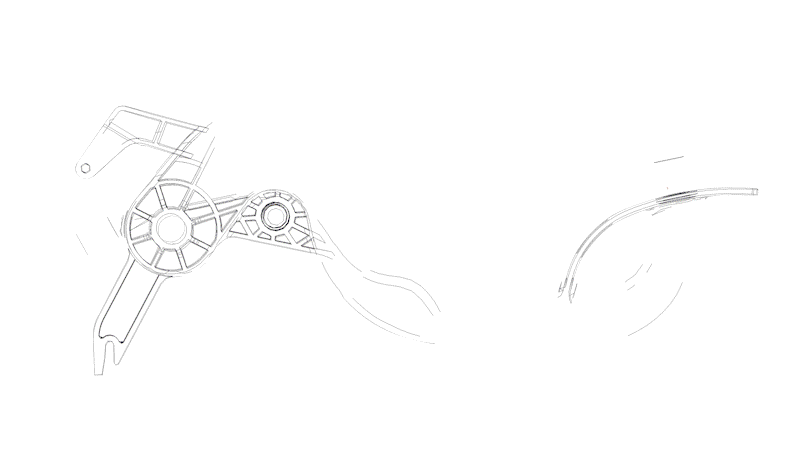
Try Moldex3D R17 Now & Download What’s New
Fill out the form to download the what’s new document and have a Moldex3D representative contact you to help you learn more about Moldex3D’s features and functions.