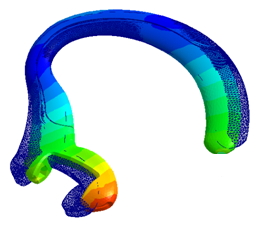
Why Co-injection Molding Simulation?
Co-injection molding process produces a plastic part with a skin and core laminated structure. The skin material is firstly injected into the mold, followed by the core material, and the machine injects skin material again to encapsulate the core. Therefore, a product can be made with desired appearance of outside skin material. With this character, co-injection molding is widely used to enable regrind and reprocessed materials as the 2nd shot core material, which brings environment benefits and cost reduction. Furthermore, the process is able to provide product strength and performance with high-impact plastics as core materials.
In addition to the fact that building a co-injection machine may requires hot runner system, control valve gates, and two barrels, which produces higher cost than a traditional injection molding machine, the main challenge faced today is to determine the optimal ratio of skin material to core material and track interface shape and distribution of individual components at any time and location in a cavity, which is critical for mechanical properties. Moldex3D provides powerful modeling solutions that allow users to obtain insights of critical characteristics of the process such as material interface and distribution, and therefore benefits companies on process optimization and development cost savings.
Challenges
- Optimize the combination of two material properties
- Determine the optimal distribution ratio of skin material to core material
- Avoid core surfacing problem, such as blow through
- Maximize overall flow performance ratio of skin to core materials
What Can Moldex3D Do?
- Visualize the flow behaviors of skin and core materials before and after breakthrough happens
- Predict the core expansion region near the breakthrough area
- Optimize geometry thickness and process conditions based on blow through prediction
- Consider temperature imbalance and pressure resistance variations of skin layer and center core
- Predict potential defective locations under high temperature and stress.
![]() |
![]() |
End of skin filling |
End of core filling |
Applicable Industries
- Electronics
- Automotive
- Medical
- Consumer Product
Applicable Moldex3D Package
- Moldex3D Professional Package
- Moldex3D Advanced Package