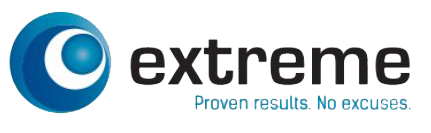
- 고객: Extreme Tool and Engineering
- 국가: 미국
- 산업: 금형 제조
- 솔루션: Moldex3D Advanced, 유동분석 모듈, 보압분석 모듈, 왜곡분석 모듈, 3D Coolant CFD
개요
Extreme이 Moldex3D를 접하기 전에는 “충진 시간은 대체 얼마나 오래 필요한가?”, “사출기의 스프루 압력을 요구치에 맞출 수 있는 방법은 없을까?”, “형체력은 얼마나 커야 하나?”, “이 재료통에는 얼마나 많은 재료를 담을 수 있는가?” 등과 같은 문제에 자주 직면했었다. 제조 과정에서 발생할 수 있는 수많은 불확실성을 해소하기 위해 Extreme은 Moldex3D의 도움을 받아 적합한 솔루션을 찾고, 제조 전에 각 상황을 더욱 확실하게 만들고자 했다.
목표
- 적합한 벤트 위치 설정
- 가장 적합한 냉각수 온도 결정
- 가장 효율적인 보압 시간 결정, 제품의 치수 안정성 충족
솔루션
Moldex3D Advanced 솔루션(유동, 보압, 냉각, 변형 모듈) 및 3D Coolant CFD)를 사용해 최적의 성형 조건 설정
장점
- 적합한 벤트 위치 확보
- 제품 수축 최소화
- 냉각 시간 및 생산주기 최적화
사례
Extreme은 Moldex3D의 도움을 받아 성형 과정 중의 불확실성을 해소하고자 했다. 테스트 몰딩 전 가장 적합한 배기 위치를 찾고, 몰딩 머신이 요구 조건을 충족하는지 평가하며, 최대 제동력과 합리적인 충진 시간을 찾을 뿐만 아니라 왜곡 현상 등을 예측하고자 하였다.
Moldex3D의 충진/보압 시뮬레이션 결과를 통해 충진 압력이 머신의 최대치 이하이며, 최대 형체력 및 최대 전단율 역시 수용 가능 범위 내에 있음을 확인할 수 있었다. 이에 따라 머신이 제조 요구 사항을 충족함을 확인할 수 있었다(그림 1).
그림 1 Moldex3D 충진/보압 시뮬레이션을 통해 Extreme의 머신이 제조 요구 사항을 충족함을 확인할 수 있었다.
Moldex3D의 유동선단 시뮬레이션 결과로 Extreme은 통제 가능한 솔루션을 마련함으로써 적합한 배기위치를 결정하고 제조 초기 단계에서 정확한 툴을 설계할 수 있게 되었다. 덕분에 미충전 문제가 발생하기 전에 후속 수정을 진행할 수 있었다(그림 2).
그림 2 Moldex3D의 미충전 시뮬레이션이 실제 결과와 일치한다.
Extreme은 이어 냉각수 온도를 낮춤으로써 표면 평균 온도를 대폭 낮출 수 있었다. 총 3가지의 냉각수 온도 시뮬레이션을 통해 제품 수축에 미치는 영향을 관찰했다. 최종적으로 117°F의 온도에서 수축량이 요구 사양을 충족함을 확인할 수 있었다(그림 3).
그림 3 3가지 다른 온도의 냉각수 시뮬레이션을 통해 117°F의 온도에서 수축량이 요구 사양을 충족함을 확인할 수 있었다.
Extreme은 보압 시간을 연장하고 4가지 서로 다른 보압 시간을 시뮬레이션하였다. 이를 통해 17초의 보압 시간에서 가장 이상적인 수축 결과를 얻을 수 있었다(그림 4).
그림 4 시뮬레이션 결과를 통해 17초의 보압 시간에서 수축량이 가장 이상적임을 확인할 수 있었다.
결론
Moldex3D는 효율적인 시뮬레이션 툴을 제공함으로써 문제가 발생할 수 있는 구간을 확인하고 Extreme이 확실한 솔루션을 결정하는 데 도움을 주었다. Extreme은 시뮬레이션을 통해 획득한 정보를 바탕으로 냉각효율을 최적화하고 최적의 생산주기를 결정하였다. 이를 통해 소모성 비용인 몰드 수정 및 재구축 작업을 생략함으로써 추후의 제품 디자인 운영에도 큰 도움을 받을 수 있었다.